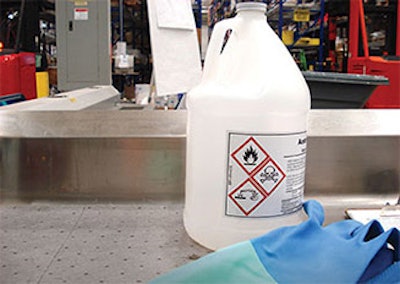
According to the National Association for Environmental Management (NAEM), regulatory compliance was 2014’s top priority in EHS management strategy, ahead of concerns about company reputation, image, or altruism. But even as compliance gains more attention, many senior leaders of chemical and manufacturing companies are still reluctant to expand budgets or implement safety data software to facilitate the GHS transition.
Why are executives opposed to more sophisticated means of hazard communication and chemical inventory management? Here’s a look at some possible hurdles EHS departments may be facing, along with advice on how to overcome them.
With the GHS June deadline approaching, manual re-classification and re-authoring of safety data sheets is expected to be the biggest EHS challenge of 2015.
A Focus on Immediate ROI
Many executives reserve budget for quick-win solutions — initiatives that can be directly tied to positive financial outcomes. In the long run, digitized safety data will certainly help reduce costly incidents (as employees will have easier access to more accurate hazard information). But even OSHA’s prediction of $266 million in savings (the annualized benefits associated with a revised HCS to align with the GHS) won’t be enough to sway every reluctant executive.
One possible solution would be to make the case for preserving competitive edge. Completing the GHS transition ahead of competitors — with a comprehensive library of up-to-date safety data sheets — could be a factor in maintaining (or even gaining) market share. In the process of due diligence, OSHA is actually asking OEMs to document “efforts to find other suppliers,” when existing suppliers are delayed in producing compliant safety data.
It’s also worth comparing the time and labor costs of manual SDS authoring versus using a third-party solution. The initial investment into a GHS software will likely provide a strong ROI compared to the costs of having SDS authoring done manually in house.
A “Get It Done” Mentality
Some of today’s most compliant organizations are still just addressing industry symptoms (OSHA/EPA regulations) rather than industry problems (unsafe/unhealthy workplace environments or practices). They do what’s required to follow the law, but not the logic of modeling and rewarding safety-conscious efforts. This is how strictly compliance-based EHS programs emerge, and why some may hamstring their own GHS transitions.
Pointing out the many unknowns in the industry’s regulatory future could be one way to appeal to compliance-focused executives. For now, manual re-classification of chemicals and re-authoring of material safety data sheets is both possible and permissible. But, for example, a manual GHS transition process discourages inventory managers from cross-referencing multiple sources of hazard data (something a digital platform could easily do). There’s no telling if multi-source requirements may inform the next wave of provisions. And there’s already good indication that regulatory agencies are moving toward digital standards in their compliance reporting and enforcement standards.
Interoperability Concerns About EHS Software
It’s tough to argue that disparate EHS platforms, housing disparate applications and data sets are much of an improvement over paper-based documentation and spreadsheets. But today’s EHS software is smarter and more comprehensive than ever before. Illustrating potential efficiency gains doesn’t have to be an uphill climb.
Best-in-breed solutions offer Material and Facility Modeling (MFM) in order to "future-proof" environmental health and safety compliance programs. EHS software that’s driven by the MFM methodology can collect your environmental and chemical data once, then leverage it across multiple applications to maximize ROI. Use cases might include applicable regulatory reports, GRI and sustainability reporting, chemical/substance phase-outs, process optimization, energy and waste optimization, plus SDS authoring and chemical inventory management.
A Reluctance to Empower EHS Employees
In many organizations, there’s a fundamental disconnect between EHS and risk management. Risk managers tend to speak the language of senior leaders, while EHS professionals speak the language of scientists and regulators. Risk managers buy the insurance, analyze the numbers, and advise top brass. EHS oversees employee safety, internal inspections and audits.
These groups don’t have to work at cross purposes.
In truth, EHS brings a wealth of critical expertise that can be used to reduce financial, operational, and strategic business risks (not just the terms that various agencies enforce). More than ever, it’s time to trust EHS experts. Convincing leaders to expand their roles (and buying power) may require some proactive research — for example, gathering data points on SDS authoring/management solutions, or inviting leaders to attend software demos.
In the meantime, don’t expect the manual hazard communication or chemical inventory management to get any easier.
Sarah Sajedi is CEO and Co-founder of ERA Environmental Management Solutions, which provides SDS software for GHS compliance.
Learn more about how to lower costs and gain efficiency in chemical manufacturing here.