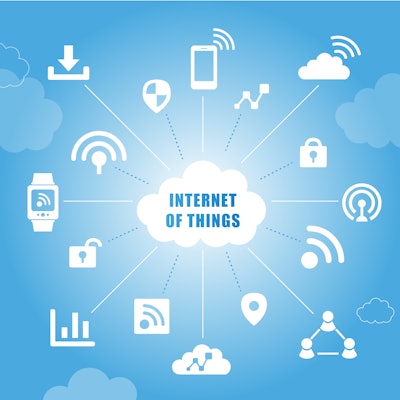
Meet the new job requirement for industrial facility and IT operations professionals — extrasensory perception, a.k.a. ESP.
Not the supernatural or psychic phenomena kind. But, real power to perceive things not present to the senses. It's the power of foreknowledge, or knowing about an event before it occurs so it can be quickly and intelligently resolved. It's a skill that is, or will soon be, table stakes for successful facility and IT professionals.
So how do professionals develop their power of ESP? Through IIoT, or the Industrial Internet of Things. IIoT is transforming management of facility and IT operations and is an integral element of manufacturing intelligence.
Relieving 'Pain Points'
IIoT is a powerful analgesic for a long list of facility and IT operational 'pain points.' It can help produce higher, better quality yields, reduce costs, monitor and control remote manufacturing operations, and improve preventive maintenance.
For critical power management systems (CPMS) (Fig. 1) that ensure reliable power for operational continuity, complying with regulatory reporting requirements, automatically testing systems and recording data, and eliminating facility rounds and manual documentation are important benefits.
IIoT comprises an array of sensors that combine advanced electronics with a wireless connection to a central computer or the Internet. The sensors are integrated into a range of facility devices, components and systems. The devices have local intelligence and compatible, two-way communication pathways and streamlined network topology protocols. IIoT can be designed for a single building, a multi-building campus, or geographically dispersed facilities, and could comprise hundreds or thousands of sensors.
Sensors stream data that each is designed to monitor and measure to highly specialized and hyper-fast software applications that aggregate, analyze, store and even act autonomously on the data without human intervention. Or, they can be remotely controlled and interact with facility personnel when necessary.
Proactively managing operations in this way is especially useful where failure of critical systems can cause catastrophic consequences to a facility's manufacturing and IT operations. HVAC, safety, security and critical power management systems are examples. For critical power, monitoring and controlling today's complex systems with precision, accuracy and reliability can mean the difference between a potentially catastrophic power outage, and business as usual.
Managing Clusters
IIoT is transforming these respective systems into management 'clusters,' or ecosystems (Fig. 2). Each streams data to an overarching system, such as a building management software, SCADA or an enterprise resource planning platform.
Multi-manufacturer equipment and devices within each cluster need to be completely compatible, share information freely, and otherwise operate seamlessly. They should be robust, follow similar network protocols and standards, and provide high-speed operation, remote access and control, and security.
The volume of data that clusters produce so quickly can be a facility and IT professionals' best friend, or worst enemy. A single industrial machine, for instance, can produce 1TB of data hourly.
Making Data Valuable
Combining data from multiple machines or other sources produces Big Data, which can be a monetizable asset, if properly captured, curated, analyzed, interpreted and shared.
Auto insurance rates based on driver behavior that's monitored by car sensors measuring braking, acceleration and other factors are an instance of monetizing Big Data. Careful drivers realize lower rates and insurance companies lower their risk level.
Remote monitoring and control of home lighting, heating, security and video surveillance systems is another. Homeowners gain enhanced efficiency, comfort and safety.
For CPMS, it's a change agent for reducing energy consumption, projecting capacity requirements, streamlining maintenance, resolving operational issues, and meeting reporting requirements.
To be truly useful, however, Big Data need to be fingertip available. The solution is dynamic visualization, which presents Big Data in easily and quickly understandable groups. Dynamic visualization of the electrical one-line (Fig. 3) of a critical power system, for example, shows power flow, which facilitates identification, diagnosis and resolution of issues.
Effectively visualizing information makes data more predictable and enhances productivity. Data analytics also avert issues via real-time trending, which help identify insights into process operations, such as problems like bottlenecking and quality issues. Data analytics also can supplant running reports that reflect a 'point-in-time' picture of a process for satisfying compliance reports, but may not accurately represent a process's "as-is" status.
Data analytics for critical power systems focus on power quality (Fig. 4). Such analytics help ensure manufacturing and IT operational reliability by monitoring power issues and helping operators correctly diagnose the 'real problem' so it can be resolved quickly. Facility and IT professionals know about operational issues sooner, understand why they are happening, and can act decisively to solve the issues. The ability to analyze, diagnose and act, both from an operator and a machine perspective, improves asset management. Operational efficiency, reliability and predictive maintenance all benefit.
Protecting Big Data
A self-healing network that avoids disruptions or overcomes disruptions instantaneously assures data continuity. Data security must be protected by multiple levels of encryption--application layer, native database object, network, and point-to-point. Programmable cryptography, digital certificates, and time stamping also should be part of a data protection program.
The key to successfully implementing IIoT in manufacturing and IT environments is to partner with a resource that has accomplished much of the legwork in developing a cohesive solution that accommodates many if not all devices in a cluster. For critical power, some manufacturers have made inroads on building their ecosystems. Facility and IT professionals can evaluate existing systems and leverage the expertise, development, and field experience that went into creating them. Once in place, facility and IT professionals can put their new-found extrasensory perception, or ESP, to work.
Bhavesh S. Patel is Vice President of Global Marketing at Emerson Network Power's ASCO Power business.
To read more manufacturing and technology news, sign up for our newsletter. You can also follow Manufacturing Business Technology on Twitter @MBTwebsite.