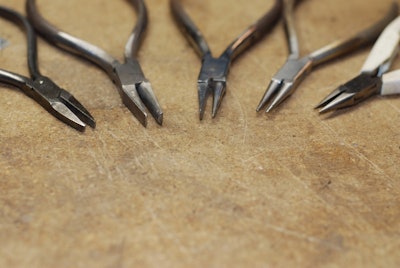
Although many manufacturing processes have become automated over the past 20 years, there is still a fair amount of manual or hand assembly and rework required. Gone are the days when electronic and industrial assembly required row upon row of technicians carefully assembling circuit boards, electronic modules or entire assemblies without the assistance of automated or semi-automated equipment. Today, lean manufacturing procedures are accepted and implemented by most companies to help reduce expenditures, improve quality, shorten lead times, and improve the bottom line. Cost saving measures need to be carefully reviewed to insure they can deliver without sacrificing quality.
One cost saving option that seems to fly well below the radar within many companies is Hand Tool Reconditioning. The term “Hand Tools” covers a very wide spectrum, so let’s zero in on just a few items for consideration. Within the electronics manufacturing industry, cutting pliers and cutting or precision point tweezers are still used extensively for a wide variety of applications. When you consider a high quality cutting plier can cost anywhere between $40.00 to $150.00, and quality cutting tweezers can cost between $30.00 to $125.00, it becomes obvious that simply disposing of these tools when they get dull or no longer function properly is a waste of money. The same issue applies to crimpers, probes and other similar tools.
Refurbishing or reconditioning services are available that, when done properly, can provide extended service life to these tools by as much as 4x. Typically, the cost to refurbish a tool is about 75% less than the cost of buying new, and in many cases, the refurbished tool will function as good as (or often better than) a new tool. In addition, reconditioning pliers will usually include; resharpened jaws, new grips, new springs and a complete buff, polish and lubrication. In effect, the tool is like brand new at a fraction of the cost.
Before you consider a reconditioning program for your electronic or industrial hand tools, do your research. Most tool manufacturers do not offer or promote reconditioning tools, for obvious reasons. High quality (and expensive) cutting pliers and tweezers are manufactured to very high standards, especially in regards to the cutting edge itself. Reproducing the original cutting edge profile, without affecting the temper of the steel, is a true science and requires a technician with vast knowledge of grinding techniques and equipment, as well as an extensive knowledge of the various manufacturer’s specifications. When considering a reconditioning service, ask the vendor to recondition a few of your tools for evaluation and test, at no charge. This will provide you with a base line of what you can expect in the future, and you can then compare the functionality of the reconditioned tool as compared to a new tool. If refurbished properly, tool life should be equal to or better than new. You should expect nothing less.
Anatomy of Hand Tool Reconditioning
Electronic Cutting Pliers
First of all, the term “cutting” is a misnomer. When a cutting plier is used on wire (solid or stranded), the tool is actually “fracturing” the wire. Most materials have a tensile strength rating, and the cutting edges of the tool are actually stressing the wire until is fractures under the pressure. For this reason, the edge profile of a cutting plier is critical. Cutting edges are often referred to as Flush Cut, Semi-Flush Cut, Ultra-Flush Cut or Center Cut. The cutting style selected is dictated by the material being cut. Flush, Semi-Flush & Ultra-Flush cutting pliers are typically used on mild wire, such as copper, annealed nickel or brass, as well as plastics (gate cutting). Center cutting pliers are most often used on hard, solid wire. Proper tool selection for the wire or material being cut will greatly extend tool life.
When reconditioning cutters and pliers, the following procedures are followed:
- Remove old grips, handles or tape from the handles.
- Adjust (tighten or loosen) the joint. This is the weakest part of most tools. Typical joint construction is either: (a) screw, (b) pin or (c) rivet. Joint or bearing wear is accelerated if this is not adjusted properly. This also ensures proper jaw alignment for the grinding process to follow.
- Cutting edges are then ground using a variety of abrasive belts and cutting wheels, depending upon the profile and construction of the tool. A small amount of material is removed from the apex of the cutting jaw to allow for tool closure as material is removed to support a crisp cutting edge. The grounded surface produced is based solely upon the type of tool and cutting edge required for the customer’s specific application. This process requires a highly trained technician, as the bulk of the grinding and polishing is still done by hand. In many cases, this is exactly how most tool manufacturers still produce the original cutting edge on the tool. High quality cutting pliers are heat treated (hardened) to 56-61 Rockwell, so improper grinding techniques could easily generate excess heat which can easily alter the rockwell hardness specifications of the tool, resulting is short or unacceptable service life.
- After grinding is completed to remove most of the flaws, the tool is honed and polished to restore the tool to that “like new” or “better-than-new” condition. This is a process that requires a very experienced technician, as the final cutting edge is now being fine-tune. If the customer requires a very specific modification to the cutting edge (tip cut, center cut, etc.), that process is done at this time. In many cases, the tool will now perform the customer’s specific task better than the original OEM tool.
- The tool is now checked for proper cutting performance.
- New grips and springs are installed. The tool is lubricated and packaged for return to the customer.
- Note: A customer should never be charged for tools that cannot be reconditioned. Examples of tools that may not be refurbished include; Excessive wear or chipped edges, excessive joint wear, bent or broken jaw tips, etc. Once refurbished and reconditioned, all tools should perform as if they were new, or in some cases, better than new.
Tweezers and Probes
Tweezer and probe reconditioning is less complicated than other tool refurbishing processes. However, the finishing process is more critical due to the small working surfaces, like the tips.
When reconditioning tweezers, the following procedures are followed:
- The process begins by thoroughly cleaning any residual contaminants from the tweezer, such as tape, epoxy, flux, etc.
- The tips are then straightened and inspected for damage.
- Holding the tweezer legs parallel, the inner surfaces of the tips are then trued using a fine grit belt, being very careful not to generate excess heat which could result in de-tempering the metal.
- The tweezer is now re-pointed using a fine grit abrasive. This process may require multiple steps.
- Final inspection is now done using a 15x loop or microscope. Tip thickness is difficult to measure and is usually a visual process that is learned through experience.
Most tweezers have square tips. There are a few that require rounded tips (I.E., N.E, N.F nomenclature) to allow the technician to pick up very fine wire from a flat surface. Imagine machining a radiused surface on tweezer tips measuring 0.010” diameter, and doing it by hand, visually, with a fine hone. This is where experience results in a perfectly reconditioned tweezer or probe.
Cutting tweezers are resharpened and reconditioned in a fashion similar to cutting pliers. The cutting surface on these tweezers are designed to do the bulk of the cutting at the tip, so they are ground to allow for more cutting surface clearance at the back (or throat) allowing pressure to produce more cutting force at the tip where it’s needed.
Summary
Taking a few moments to audit your expenditures for NEW tools during any given year will help put these cost differences into perspective. Saving 75% of your “new” tool expenditures over a given period should fit nicely within most lean manufacturing formulas. As mentioned earlier, this is truly a cost consideration that continues to fly under the radar within most companies. I’m betting your tool crib has bins full of non-useable tools. Or are they?
For more information about Custom Products & Services, Inc., please visit their website at www.custom-products.com.