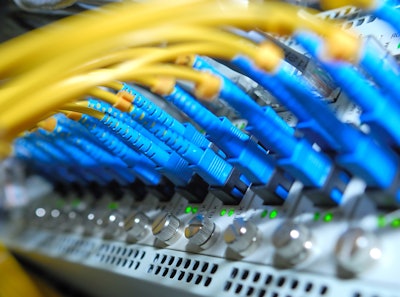
The factors that favor structured cabling systems over the traditional point-to-point approach are multiplying every day in plants.
Old industrial control systems – many of them proprietary and often based on point-to-point cabling using screw-terminal connections – have given way to the ease of ubiquitous Ethernet and IP technology. This shift has helped spark an explosion of digital devices on plant floors, and increased the demand for the higher performance, bandwidth and reliability offered by a highly structured, standards-based network infrastructure.
More devices mean more data racing at higher rates across modern networks. Industrial data rates have risen from kilobits per second, to megabits per second, and even gigabit per second in some shop floor applications. To effectively operate at those rates – ensuring plant uptime and keeping costs down – modern networks need a well-engineered and validated cabling structure.
Structured cabling systems also are capable of evolving with the future. Industrial data rates eventually will meet and potentially surpass the 10-gigabit per-second level already common on the IT side. Meanwhile, industrial processes and machines are becoming more intelligent, employing advanced instrumentation, sensors and wireless technology.
For all these reasons and more, structured cabling systems are replacing the often haphazard and ad hoc point-to-point approach. In a structured scheme, cabling is systematically laid out, and managed to accommodate all today’s and tomorrow’s industrial communication needs, including voice, data and video.
Gaining the full benefits of structured cabling requires an equally systematic approach to conceptualizing, specifying, installing, testing and maintaining plant-wide networks.
Defining the structured approach
Structured cabling systems comprise five subsystems in a facility:
- The demarcation point, where the telephone or Internet company ends and connects to the on-premises wiring
- The equipment or telecommunications room, which houses equipment and consolidation points
- Vertical or riser cabling, which connects equipment rooms, usually between different floors
- Horizontal wiring that connects equipment rooms to individual outlets or work areas, usually on the same floor
- The work area, where user equipment connects through outlets to the horizontal cabling system
Cabling in each of these subsystem areas follows a defined form, composed typically of an equipment cord (a patch cord at the equipment end), the permanent link (fixed, solid conductor cabling) and a work area cord (i.e. a patch cord connecting to a work station). This arrangement is called the channel. Other configurations featuring additional connections in the channel are permissible.
The permanent link is a pivotal feature of any structured cabling system. For example, it runs from the telecommunications room (TR) to a distribution point (e.g. outlet or a patch panel.) That permanent link allows the uplink to be tested from the machine to the higher-level network, helping ensure the connection and the machine both will perform as needed. Likewise, in a ring network that connects multiple processes, a structured cabling configuration allows each link to be tested.
Contrast this methodology to the point-to-point cabling system approach, which seldom – if ever – involves testing. Instead, when plant personnel need to add another machine or extend the reach of a cable, they may simply use a patch cord and plug it into a switch panel. Indeed, some experienced control engineers are accustomed to creating their own patch cords by stripping off the jacket on a wire and attaching a connector on each end. These patch cords terminate in a plug, rather than a jack.
Such point-to-point practices might suffice with shorter patch-cord lengths. But this “extension cord” approach can fail to deliver full performance if a patch cord becomes 80 or 90 meters long. The reason: Stranded conductor cabling – which is prevalent in point-to-point cabling approaches – has less conductivity, and hence, higher insertion loss than the solid conductor cabling used in structured cabling systems.
And in a whole factory, point-to-point connections can result in network sprawl. Surrounded by hundreds and even thousands of unstructured, non-standard and unidentified connections, automation and IT people can lose track of what’s connected to what.
Collaboration between IT groups and automation staff is key to the success of any structured cabling project. IT people are highly familiar with structured cabling at the enterprise level, while automation people best understand the factory environment around machines.
But the collaboration can’t stop there. Maintenance and operations personnel – as well as outside experts – can play essential roles in the implementation and smooth operation of structured network.
Follow these steps to implement and maintain an optimal structured cabling infrastructure:
1. Educate yourself. Get familiar with the standards and best practices established by organizations such as the Telecommunications Industry Association (TIA), the IEC, and ODVA, which offers information on machine-level EtherNet/IP best practices.
Common best practices for critical fiber and copper connections within network infrastructures include the ability to:
- Terminate horizontal runs to patch field connectors to form permanent link.
- Validate performance with standards-based tests and equipment.
- Easily replace patch cords if they are damaged or suspect. You do not need to touch the horizontal cable.
- Improve troubleshooting with well identified, structured connections that support staff can easily manage.
Standards organizations also have established parameters on network operating factors such as the error-rate performance. If the error rate starts to become too high, it slows down the network – and possibly could cause failure of the link.
Take advantage of structured cabling design guides from companies – for example the Fiber Optic Application Guide from Rockwell Automation, Panduit, and Cisco – that specify how to design and deploy structured cabling for fiber and copper systems. Seminars and other types of structured cabling training are also available.
2. Establish your goals and objectives. Assess your needs today, while keeping the future firmly in mind. Where will your operation be in five or 10 years? If you want to go to gigabit-per-second equipment-data rates, structured cabling offers the optimal support, and can be tested to validate that desired performance levels are met.
With structured networking, industrial plants become more scalable, especially if they invest in the recommended 30-to-40-percent spare cabling at the time of initial installation.
3. Design the infrastructure and draft specifications. Many standards-based tools are available to help design your structured cabling network, including Visio and CAD. Additionally, many highly experienced third-party qualified experts are available to help plants execute this critical step in the process.
Develop a specification document that establishes your structured cabling standards, and the materials required for your particular operation. Robust specifications will simplify the rest of the process, including installation, testing, operations and maintenance.
Specifications will cover how to implement the plant network for reliability, security and physical considerations. Those include the integrity of the cabling itself, since substandard cabling could come with serious consequences.
IT and automation personnel should collaborate on the specification document to drive best practices throughout their facility. Specifications often detail how to implement structured cabling to connect the enterprise level to distribution zones, and how to bring cabling into the process and individual machines.
This document also allows you to specify your standards on required bandwidth performance, so you have consistency for today and you’re future-ready. You also can specify where it’s critical to locate testing patch points and what your requirements are for testing.
Protecting the network from the environment is another key consideration in many plants. If you have electromagnetic interference (EMI) risks, then you may need shielded cabling or conduits. The TIA and IEC have established standards related to environmental assessment to help in the process.
You may also want to develop physical identification strategies, such as using color-coded cabling and jacks, and labeling ports. Such strategies will help reduce risks in installation, and far into the future because personnel will be able to clearly understand where various cables should connect.
Specifications should also include any necessary security tactics, including lockable enclosures, port block-outs and plug lock-ins that limit access and help prevent unauthorized connections or removal of patch cords.
4. Installation – Because of the many details included in installation, this is the step with the greatest potential for error. For example, plants that want to support gigabit per second communications may buy the correct Category 6 cabling, but it must be installed correctly to deliver that rate.
Make sure your installer understands the intricacies of working with structured cabling – details like bend radius and the twist of the cable, the routing, and protecting the network from noise sources. You can take advantage of third-party certified installers, or make sure your own installers have the necessary expertise by attending training classes that are available.
There also are integrated, standardized installation tools and products on the market to help reduce the amount of training and expertise needed. One example would be an enclosure that’s pre-wired using all the best practices for patching and cabling.
Keep your installations neat and clean. Bundle cables when routing both long- distance and short-distance cable. That way, you can easily troubleshoot the system, make any necessary changes to adjust to production demands, and properly maintain your system long-term. Ensure standards-based labeling schemes are used.
5. Testing. This is where a standards-based structured cabling network really shines. Testing equipment is readily available on the market to help ensure you’re getting the performance you paid for – and that you can count on it well into the future
Without testing, you risk startup delays, downtime, callbacks to the manufacturer and a host of other costly huge headaches.
But with successful testing results in hand to benchmark performance, you can use scheduled shutdowns or upgrading opportunities to retest and validate your network – the backbone of your automation system.
6. Operations and maintenance. While the design and installation of a structured cabling network is usually undertaken by a specialized group – often a third-party – the system ultimately becomes the responsibility of the industrial automation user.
To avoid subsequent degradation of the system, you have to keep leveraging the capabilities and best practices designed into the system – or risk losing control of it.
A common problem is the return of the old point-to-point practices. Someone on the plant floor may decide to put in a new cord to solve a problem or serve a temporary need. But more problems can arise if they don’t bundle correctly, or fail to identify the connection. Soon, you could have multiple dangling cords – and no idea why.
Or you may end up with surplus cabling on the floor because personnel used a 10-foot patch cord where they should have used a much shorter one.
Then there’s the chance that someone may go in and unblock a port and forget to block it up. Now you’re left with a potential access-point to the system.
Such patchwork problems can be avoided by clearly establishing and strictly enforcing operational and maintenance policies regarded structured cabling networks. Plants can also employ monitoring tools for the operational phase that can detect problems with your network traffic and physical infrastructure, such as the condition of your switches and servers, as well as environmental and security controls.
For more information, visit www.industrial-ip.org.