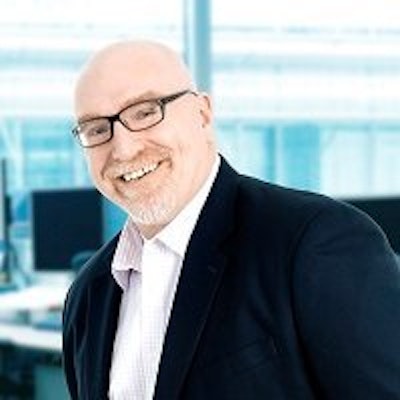
Maximize customer value while minimizing waste; at the most basic level, this is what it means to go lean. Because we are living in an age where increased efficiency is not only desired, but also required in order to stay competitive, every manufacturing company can benefit from implementing a sustainable lean strategy.
First, let’s bury the common misconception that lean manufacturing is only applicable to large manufacturers. The truth is, the benefits of lean manufacturing are far too significant to be overlooked by even the smallest of manufacturing companies. So whether your organization is a large enterprise, or a manufacturing company comprised of just two people, going lean should be at the forefront of your business strategy.
Going lean is meant to simplify processes, so it is important to not over complicate the implementation process. At the same time, we must remember that going lean is a cultural change and a journey that takes time and careful planning to implement correctly, and must not be rushed. In this article, we will lay out five simple tips that will help your business successfully go lean.
Understand Your Current State and Culture
Before you attempt the operational or tactical aspects of lean, take some time and understand your company’s current culture and business state.
1. Involve the Entire Company from the Start: Choosing to go lean means choosing to make a cultural change, one that everyone needs to be a part of. The sooner you can get your employees onboard and embracing this change, (even if you only have one or two) the better. Implementing a successful lean manufacturing strategy needs to be a group effort. The entire operation could be in jeopardy, if even one person in your company is not willing to embrace a lean mindset. To prevent this, try to get your employees excited about going lean and include them every step of the way.
2. Determine What Works Best for You: It is important to understand that one size does not fit all and a one-off approach may not work. Concepts, such as value stream mapping, one piece flow/continuous flow or 5S initiatives can be helpful tools, but keep in mind that these “tools” are not meant to exist in isolation. At the same time, success depends on a comprehensive, but not necessarily complicated, strategy that is uniquely suited to your business. Not every rule or tool associated with lean will apply to your business, so take the time to figure out what works best for you.
3. Take Adequate Time to Plan: Owners and key stakeholders should develop a three year business plan that provides a roadmap and structure for their lean journey. Three years should be just enough time for you to start seeing the long term benefits of your lean strategy. Start creating the plan by determining what your business is good at doing, what you want to improve and, most important, how you’ll get all employees on board.
Implement Key Operational and Tactical Aspects of Lean
Once your company has gone through the exercise of understanding its culture and current strengths and weaknesses (and then adjust based on your findings), you are ready to get more tactical.
4. Don’t forget the Basics: Many small manufacturers are challenged with trying to manage hundreds or thousands of part numbers. This can be especially challenging in relation to lean. Therefore, I recommend developing part families. Many people skip this step and jump right into creating lean cells, but taking the time to first develop part families will make things much easier for you down the line. That’s because part families help you to further refine your core competency and eliminate unnecessary and disruptive parts, creating a more automated production flow. To create part families, start by looking for parts that are similar in shape and geometry or ones that are produced using similar material or processes.
5. Run Each Cell Independently: Ultimately, all of these part families you have analyzed and created above should now be mapped in terms of reducing total flow and production time and eliminate waste. You can do this by converting your current shop layout into some key manufacturing cells. These cells can further streamline your overall manufacturing flow. However, it is not enough to just create these cells, you must also test and run each cell independently. This will help you see things like overproduction, enabling you to eliminate waste and cut costs. These results can then be implemented in other areas across the shop floor.
There is no doubt that if you follow the steps listed above you will be on your way to going lean, however it is important to set attainable and realistic expectations for your company. These expectations should also be measurable to ensure you are getting the most out of your lean solution. Understand that going lean will take time and there are bound to be some bumps in the road before you see a pay-off, but no doubt, you will see the return. Going lean results in increased profits, decreased costs and long term efficiency gains, not to mention environmental benefits through the elimination of waste, including overproduction, defects and inventory.
Dave Lechleitner is Principal, Product Marketing, at Exact and the Chair of the Software Technology Council, Fabricators & Manufacturers Association. For more insights, visit www.exactonline.com.