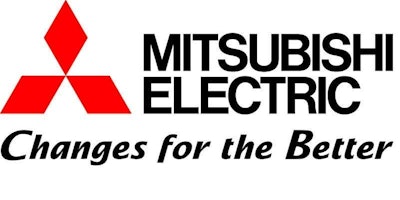
Automation is becoming more and more common in the manufacturing sector as companies begin to understand its many benefits. Alex Bonaire, the Robot Product Manager at Mitsubishi Electric, provided IMPO with some expert insight into the evolving world of industrial automation.
Maura Falk: Could you speak to some of the main benefits of implementing automation on the plant floor?
Alex Bonaire: I don’t know where to begin, there are so many. On the very basic level it allows companies to produce more products with more consistency, higher quality and at an increased rate so you get a higher net throughput compared to traditional manual operations.
READ MORE: How Technology is Making Manufacturing Profitable...Again
MF: With regards to safety and efficiency, Mitsubishi has a new robot safety controller that allows for some very unique robotic solutions. Can you please describe some of these solutions and some of their most significant benefits?
AB: What the new product allows customers to do is to apply robots in a wider range of scenarios, which results in more application options for the customers. It also changes safety equipment, before a more traditional means of safety guarding would be required, but now with Mitsubishi’s new product [The Advanced Robot Safety Monitor] you can monitor the robot’s speed and position with virtual boundaries. Before you would have to have guarding barriers that would take up a lot of space in the plant environment. Now you can actually shrink that significantly because the robot itself is monitoring its own speed and position at all times and it is safety rated which means it has redundancy to ensure safe operation in the event of hardware failure.
When a robot is equipped with the safety monitor, you also gain the ability to incorporate external sensors that allow for advanced scenarios where the robot can be zoned. For example, it can function at a high speed in a certain zone that is far away from the operator but as the robot approaches the secondary zone where there is an operator present or is less guarded — or not guarded at all — by a physical barrier, the robot could then operate at a reduced speed that would be safe for a person to be in a much closer proximity to that robot. Whereas if it were to run at full speed or a higher speed in that same close proximity, it would not be safe for the operator.
There is also a function of the Advanced Robot Safety Monitor that checks and controls how much force the robot is applying. So in collaborative situations where a person is interacting with a robot directly, the robot can monitor the level of force being exerted and not exceed a level that could be potentially hazardous or harmful to a person. This is key because by monitoring and controlling force (along with speed), the safety system allows any of our normal industrial robots to run in a collaborative fashion.
MF: Can you describe how automation is changing and evolving in manufacturing facilities today?
AB: A lot of the new developments in the recent years have been geared towards getting people and robots — and automation in general — working more closely together. Historically, it has always been very separate. Either it is a manual process or it is an automated process, but now as operations, applications and manufacturing facilities are evolving and becoming more flexible, the need for human and machine collaboration to take place is really coming to the forefront.
This is particularly evident as companies begin to develop collaborative type systems and products that allow people to interact directly with robots. The other trend that I am seeing is enhanced intelligence in robots. For example, application of technologies like 2D/3D vision and bin picking, where robots can identify items that are not fixed by traditional means, and instead, just loose parts are presented to the robot which can then determine based on sensor feedback, how best to pick them. Another trend is software that has a certain degree of artificial intelligence that helps eliminate the need for expert programmers and that does some of the programming for the end user.
MF: Do you find that there is still resistance to automation coming into manufacturing facilities or is it something that is being generally accepted?
AB: I think that once a particular company begins to automate they embrace it wholeheartedly. However, when you have a company that has not had any experience with automation, it is more of a challenge to get them to embrace it because they don’t have any familiarity with it. It is a very foreign concept and there often is a certain degree of fear. But, I have yet to encounter a company that has automated and is not happy with the results.
MF: Other than potential cultural resistance, what are some challenges to implementing automation for manufacturing businesses?
AB: What we often see is that when a company has an existing process and they go to automate it, there are often questions of retrofitting their existing tools and processes to the new automation. And because they were originally designed to be executed in a manual way, it doesn’t necessarily always lend itself to being automated. So companies will often end up discovering inconsistencies in their products and will be tasked with improving their overall manufacturing process. The reason this happens is because humans have an incredible ability to adapt to the variations and inconsistencies that a product might have; whereas if the process is automated, the automation expects that a part or process to be exactly the same every time. So companies often end up with more consistent products, and of higher quality after automating, not just because the automation is executing processes the same every time, but because the company has addressed inconsistencies in the product design and/or process itself.
Although these scenarios can be challenging for a machine to adapt to, technologies like machine vision and force sensing, along with advanced programming techniques enable robots to more easily adapt to changing conditions, so the amount of engineering required when automating can be reduced.
MF: How do you see automation changing in the future, can you share any predictions, and how does Mitsubishi fit into the mix?
AB: I expect there to be a lot more integration between different types of hardware to make it easier for customers to connect devices together. There are several industry wide initiatives, like factory 2.0 and other protocol based initiatives to have different pieces of hardware seamlessly connect to each other, essentially making devices “plug and play.” Historically, it has always been that you have one component, and then you have a full machine and then another machine, etc… So you had to figure out how to have them all communicate with each other. They all often talk different “languages” so there are a variety of different ways you could connect them, not all of which are easy to do. There are lots of different possibilities so companies are beginning to move towards seamless integration where you are able to just plug a robot or device in and it already understands what it is talking to and how, making it very easy to implement.
Mitsubishi in particular is very mindful of this need for easy connectivity. Therefore, in all of our products we try to make sure that whatever is connected within our product line is very easy for one product to connect to another even if it is an unrelated type of product. For example, if you have a robot and you connect it with an auxiliary servo amplifier or HMI, each device knows that the others are connected, so then the parameters for each device are made available and configured, which makes it very easy to get up and running.