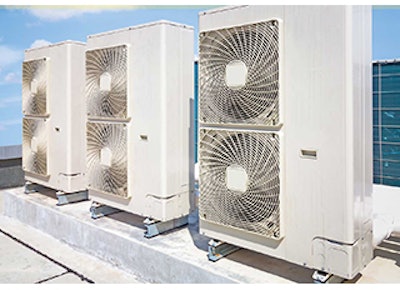
This article originally appeared in the March 2015 print edition of Industrial Maintenance and Plant Operations magazine, our sister publication.
This article originally appear in IMPO's March edition.
Everyone is familiar with the three main utilities — water, gas and electricity — however, there is a fourth utility that isn’t being recognized as it should be. That utility is compressed air. Unfortunately, this fourth utility tends be a costly expenditure for most manufacturers, but there are a few ways around those expenses and it starts with efficiency. An efficient compressed air system can be invaluable asset to a manufacturer. So in order to help, here are five tips on how to achieve the most efficient compressed system.
Tip #1
Be unique, think about your applications specific needs. According to Daniel Leiss, CEO of Jenny Products, “there is no cookie cutter model for compressed air systems. It all depends on what you need.”
In order to have an efficient compressed air system, it must be tailored to a specific operation. For example when considering a new compressed air system Wayne Perry, technical director at Kaeser Compressors, Inc., says that one should consult with a professional who understands compressed air and who can provide advice tailored to specific scenarios. “No two experts will give you the exact same advice, but that doesn’t mean one is bad and the other good,” Perry says. There are just several roads to efficient operation and it is up to the manufacturer to choose the most efficient system for them.
According to Daniel Leiss, CEO of Jenny Products, “there is no cookie cutter model for compressed air systems. It all depends on what you need.” And figuring out what system fits your needs can be a challenge, as Leiss points out when he says, “There is never going to be a one size fits all system.” Therefore, each manufacturer needs to think about their current system and what they want to change, keep the same or improve upon. Such questions could include: Are there leaks in my current system that could be fixed? Is the piping sized properly? Could the pressure be lowered? Are the filters clean and the correct size? Then, once that manufacturers specific needs are figured out, it can be determined what system will be most efficient.
Tip #2
Make sure to choose the right sized components for the system. The main factor for an efficient compressed air system is proper sizing. Chad Hill, a product manager of Transair, explains that if a system isn’t sized properly a manufacturer could experience significant pressure drops caused by an undersized system. Conversely, Perry adds that it is also extremely important not to over-pressure, over-dry, or over-filter the air as all these things waste money.
For example, in some cases it is actually more efficient to use multiple small compressors instead of one or two large ones. Compressors running at full load are more efficient than ones running below capacity and smaller compressors may also have the ability to turn off during times of lower demand.
Another example of the importance of sizing came from many personal experiences of Perry’s while working with customers. The customers often install a desiccant dryer (less efficient), rather than a refrigerated dryer because they say that water was being found in their lines with the refrigerated dryer. However, this is actually most likely a result of the original drying not being the proper size, instead of being ineffective. Therefore, it is extremely important to find the proper sizing of all the components of a compressed air system to achieve greater overall efficiency.
Tip #3
Choose the right design. There are many different designs for compressed systems however, there are a few specific things that can lend towards a more efficient system. For example, using a ring main as opposed to a straight run can greatly effect a manufacturer’s efficiency as it gives additional air from multiple points instead of one.
Another feature that promotes efficiency is the O-ring technology, which is a common sealant designed to be placed between two connecting surfaces where it then seals the surfaces together. A system with this technology will be able to overcome expansion, contractions and vibrations without breaking and causing leaks. Other key design features include dryers —which are used to take the moisture out of compressed air traveling into critical equipment — and storage tanks and pressure flow controllers. These two components of the system are particularly important — or “absolutely key” to increase efficiency says Hill — as they allow the generator to exert less effort to pressurize the air needed for the system.
The last design feature to pay close attention to when putting together a more efficient compressed air system is the motor. A variable speed drive is not necessarily always the right answer. Perry explains that a VSD compressor has a constant, unavoidable drive loss. “Therefore, if a plant’s demand is relatively constant or changes in demand occur at a slower rate, a VSD may be perfect fit. On the other hand, if the plant has sudden, intermittent high demand events, it may be better to use fixed speed compressors and storage,” he says.
Tip #4
Keep in mind where you are placing your compressed air system. According to Perry, “Compressors are easier to control and maintain when they are in a central location.” He explains that placing compressors in remote locations due to space concerns or pressure problems is rarely a good idea, and while there are some situations where a remote compressor dedicated to one particular end could work, single systems generally run more efficiently when they are in a single location.
Tip #5
Don’t forget about system monitoring and new technology. When it comes to running an efficient compressed air system it is important to maintain an on-going form of system monitoring. By having a closely watched system it is possible to avoid downtime, scrap and lower quality air.
This monitoring is also being made easier with the advent of new technologies related to compressed air systems. For example, Hill detailed a new technology on the market that is a wireless condition monitoring system for compressed air gas systems that can monitor — in real-time — pressure, temperature, humidity, flow and dew point of a particular system while sending users continuous alerts. Such technology gives users the information necessary to make intelligent changes and choices when it comes to their system.
People often don’t seem to understand the high costs and self-imposed inefficiencies associated with compressed air systems even though they are a crucial piece of an operation’s infrastructure. This disconnect needs to change, from now on put the emphasis on building an efficient system using these five tips as your starting point.