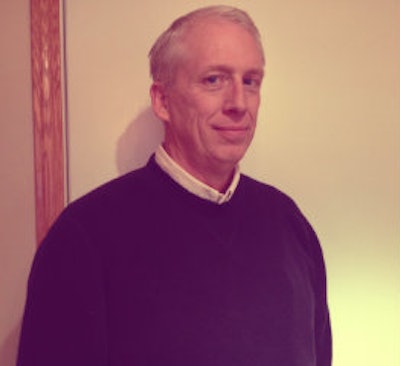
For 31 years Wes Dean has been supporting production, maintenance, IT and warehouse operations – the majority of that time being spent in the Coors and MillerCoors family. He currently serves as the Senior Asset Care Systems Engineer for MillerCoors where he provides technical leadership for assets and material management to ensure compliance with the associated processes. He’ll also be a featured speaker at the upcoming SAP-Centric EAM Conference taking place March 8-11.
Wes recently sat down to discuss a number of trends and challenges impacting maintenance and asset management for manufacturers.
Jeff Reinke: Looking at the industrial marketplace as a whole, what do you see as some of the most significant trends impacting asset management?
Wes Dean: I think the following will have the greatest impact:
· Aging production machines and vehicle, combined with a massive exodus in the next five -10 years of an aging maintenance workforce. This is compounded by the trend of many younger workers staying in positions for shorter amounts of time. Should there be plans for retaining younger workers?
· Newly designed equipment is becoming more independently run by computers, so start-ups and repairs require continuous training. This is coupled with a lack of new training programs set up for the maintenance staff in certain manufacturing or utilities areas.
· Data analytics will continue to have a greater impact on traditional maintenance roles. How do we prepare our people and our programs for machines that tell us when they need maintenance?
JR: Managing a global team can be daunting – what are some best practices you can share with others in a similar role?
WD: Communications between different age groups, cultures, nationalities or even different areas of the U.S. is sometimes challenging. One of the biggest hurdles to leap is getting people to work together on the same platform to accomplish a business task. Try to get them to work together as one team to accomplish a task, with each person having a stake in the game - just like the nine players on a baseball field.
Depending on how a company is staffed in certain areas or shifts, there might be a lack of manufacturing or maintenance experience. One of the steps to help bring on new people into a position is to have them work with seasoned workers who can bring them up to speed rather quickly for that job.
Finally, leveraging standards, policies and practices through audits can help get everyone working in the same direction
JR: What are some of the most significant challenges you face in managing maintenance personal and resources?
WD: First, improving communications between the staff and yourself. Continuously steering the team’s focus towards the same set of goals. Providing new learning opportunities related to areas they support and trying to help retain good workers.
JR: What advice could you offer on the use and implementation of remote monitoring technologies?
WD: Remote Monitoring is a newer technology that many companies have started using at their sites over the past decade. Rather than having people walk around and manually read meters and document temperatures, pressures, testing vibration analysis, etc., remote monitoring has several benefits for maintenance:
· It saves time so people can be assigned to do other maintenance tasks.
· A near real-time work order can be system-generated in warning the maintenance staff to investigate a problem right before a failure.
· Remote monitors can feed data into computerized systems where graphs, flowcharts, etc. can be developed to start analyzing future maintenance trends for similar equipment or material.
JR: Finding qualified personnel for plant maintenance and planning positions continues to be a challenge for many U.S. manufacturers. What advice can you offer in either finding high-quality individuals or training internal staff to handle greater responsibilities?
WD: The newer generation is very computer savvy. Interests that the Baby-Boomer generation had are different from what the millennial generation focuses on. For example:
· They are more likely use public transportation versus owning a car.
· As opposed to looking at putting in overtime, they want to explore ways of accomplishing the same tasks in less than a traditional 40-hour work week.
· Instead of physically maintaining a production line, they’re more inclined to sit and use handheld controls.
Some key things to think about is whether or not planning or maintenance training can be taught in high schools or junior colleges, with the understanding that most are still trying to figure out what they want to do.
Setting up learning programs related to the whole manufacturing process in your company can also help people understand why they are essential to keep the business running. Examples could include planning academies, maintenance training or electrical and mechanical classes at a junior college – all of which can help retain quality workers.
JR: If you could give your peers one thing (piece of advice or guidance), what would it be?
WD: Develop communications with other businesses to share findings, experiences and victories related to maintenance of similar processes and/or equipment.
JR: What do you feel will be the most significant takeaway for attendees at the SAP-Centric EAM Conference?
WD: The realization that the other companies attending have most of the same problems, questions and ideas that you have. Start talking with people from other companies in similar business sectors regarding how they resolved issues you’re facing. There are also many vendors showing business processes or systems they developed that have helped simplify or improve certain maintenance opportunities.
Click here for more information on the upcoming SAP-Centric EAM Conference.
ENTRIES OPEN: Establish your company as a technology leader. For 50 years, the R&D 100 Awards, widely recognized as the “Oscars of Invention,” have showcased products of technological significance. Learn more.