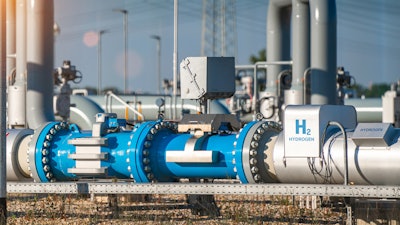
Hydrogen is the most abundant chemical element in the universe, but it does not exist as a discrete substance, and must be processed before it can be used as an energy carrier. Renewable hydrogen production has a key role to play in enabling countries to reduce carbon emissions and meet global targets.
Hydrogen is enjoying a worldwide resurgence of interest as a potential green energy source, since it does not emit carbon dioxide, and air pollution resulting from its use is virtually zero. The only by-products are oxygen and heat, which can be harvested for further use. This promising alternative to oil and gas features heavily in the green energy strategies of countries around the world.1
Today, hydrogen-based technologies are firmly in the spotlight as potential options for generating and using energy in all parts of heavy industry and transport. Its use is also being explored for power-to-x conversion technologies – electricity conversion, storage, and reconversion pathways that use surplus electric power – and for heating and powering homes, as part of a wider decarbonisation strategy.
Hydrogen can be used as a feedstock, a fuel, an energy carrier and for energy storage, with numerous possible applications across various sectors. This makes it a promising solution for the decarbonisation of industrial processes and economic sectors where reducing carbon emissions is both urgent and hard to achieve. However, its environmental friendliness depends entirely on how much carbon is released during its generation.
The vast majority of global hydrogen production is ‘brown hydrogen’. Generated during fossil fuel processing, among other industrial operations, it arises from processes that release large quantities of carbon into the atmosphere. In many sectors, these harmful emissions can be reduced via carbon capture, resulting in the production of ‘blue’ hydrogen.
However, the most environmentally friendly means of hydrogen production use renewable energy sources – wind or solar power – to separate water into its constituent oxygen and ‘green’ hydrogen components by electrolysis. This green hydrogen is frequently seen as the only truly carbon neutral way to generate hydrogen, and could be a key driver towards a cleaner future.
There are several distinct types of electrolysers commonly used for the generation of green hydrogen, and all of them work on the same basic principles. A direct current electrical supply is applied to a pair of electrodes – typically separated by a membrane – in contact with a pure water supply. Pure oxygen is liberated on the anode side of the membrane, and pure hydrogen on the cathode side. Examples of this type of electrolyser included alkaline electrolyte membrane (AEM), polymer electrolyte membrane (PEM) and solid oxide electrolyte cell (SOEC) systems.
A Partnership with Electric Chemistry
A more recent development is the novel membrane-free electrolysis (MFE) and cryogenic separation process from Clean Power Hydrogen (CPH2). The manufacture of these self-contained oxygen and hydrogen production systems – or ISO units – offers a truly green alternative to traditional electrolysers. Such systems are of particular interest to hydrogen fuel cell manufacturers – who are tightly bound by ISO purity specifications2 – making it imperative to accurately measure and declare impurity levels.
MFE generates a mixed output stream, which is then dried and separated into hydrogen and oxygen using cryogenics. Typically, the purity of the hydrogen and oxygen produced is determined using discrete gas analysers. These monitor oxygen and water levels in the hydrogen outlet, and hydrogen and water in the oxygen stream.
However, these relatively low-cost options have limitations, as they usually offer single component analysis of a gaseous species in a specific gas matrix, such as hydrogen in air. This means that at least two analysers are required – one for the oxygen outlet and one for the hydrogen stream – significantly increasing the overall cost as the number of electrolyser systems is scaled up. Gas analysers are also typically only accurate to within ±2 % – which is insufficient for some of the most stringent hydrogen generation applications – and there will always be a degree of uncertainty in the measurements, due to analyser-to-analyser variability.
The Mass Spectrometry Advantage
High precision, magnetic sector mass spectrometers offer a number of advantages over gas analyzers for monitoring the purity of the hydrogen and oxygen generated by the MFE and cryogenic separation process. Instruments with the ability to perform rapid multipoint sampling – such as the Thermo Scientific™ Prima BT Bench Top Process Mass Spectrometer and Thermo Scientific™ Prima PRO Process Mass Spectrometer – can be used to eliminate any measurement variability between streams.
At the same time, the implementation of mass spectrometry analysis enables simultaneous measurement of multiple gas species at several locations in the process, all within a single unit, drastically reducing the complexity of the analytical set-up. The use of high precision magnetic sector technology allows confirmation of the purity of the MFE-generated hydrogen and oxygen streams to within ±0.1 percent. This means that factory acceptance testing can be performed on every ISO unit leaving the production facility, and certificates stating the exact level of impurities in the product stream can be issued. Production plant efficiencies can also be estimated, providing operators with an accurate prediction of the power consumption per kg of hydrogen produced.
Endorsing Eco-Electrolysis
Magnetic sector mass spectrometers have been used to measure hydrogen in a wide range of processes for many years, demonstrating the highest levels of precision and stability. In the race to replace fossil fuels with renewables, green hydrogen produced by electrolysis has emerged as probably the only truly carbon neutral process for the generation of hydrogen.
Magnetic sector mass spectrometers are already being used to provide fast off-gas analysis for electrolytic hydrogen generation across the spectrum – laboratory research and pilot plants to full-scale production – offering highly precise and complete gas composition measurements that are easily incorporated into process control systems. The success of this technology has been amply demonstrated by its implementation in the MFE and cryogenic separation process, where it is providing the analytical capabilities required to boost renewable hydrogen production and provide a truly decarbonised future.
1. European Commission, A hydrogen strategy for a climate-neutral Europe, (EUR-Lex - 52020DC0301 - EN - EUR-Lex (europa.eu))
2. International Organization for Standardization, ISO 13687:2019 Hydrogen fuel cell quality – product specification, ISO 14687:2019. Hydrogen fuel quality – Product specification