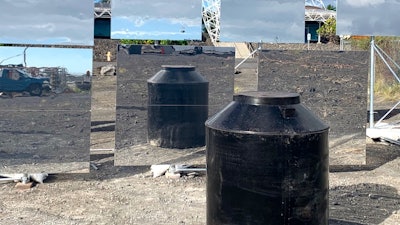
LightManufacturing, a solar technology company from Pismo Beach, California, promotes its solar thermal plastic molding systems as a new way produce sustainable plastic.
Similar to a magnifying glass burning a patch of grass, LightManufacturing's method involves using giant panels that reflect sun rays onto a rotating mold to create large plastic items such as kayaks and water barrels.
CEO Karl von Kries noted that rotomolding is common for large plastic products but asserted that LightManufacturing makes the process cheaper and cleaner. In this Q&A with IEN, von Kries discusses the method's cost savings, improved product quality, scalability and diverse applications, including use by the U.S. military.
Most Read on IEN:
- Hot Sauce Maker Halts Production Due to Chili Pepper Color
- Air Force Awards $13B for New Fleet of 'Doomsday Planes'
- Heineken Uproots Huge Apple Orchard as Cider Sales Slip
- Former Tesla Supercharger Staffers Reveal Details of Department Fallout, Aftermath
LightManufacturing
Nolan Beilstein (NB): How does LightManufacturing’s solar thermal plastic molding systems work?
Karl von Kries (KVK): Our Solar Rotational Molding (SRM) systems reflect heat from the sun onto a rotational mold to eliminate the need for fossil fuels.
Arrays of sun-tracking mirrors called heliostats concentrate thousands of watts of heat onto the mold, heating it quickly without the emissions and cost of natural gas.
NB: What advantages does this method have over traditional plastic molding processes?
KVK: Several. First, product costs are reduced by 15% to 30% depending on local market concisions, which is a huge savings in a commodity-product market.
Capital expanse of our systems is at 10% of traditional molding systems, because our systems are containerized and setup on bare land; no utilities or building required. Finally, we can reduce transport costs (and emissions) by locating our ‘factory-in-a-box’ solutions close to customers. Transportation is a big factor when delivering large water tanks or septic tanks to the end user. So we have disruptive savings in CapEx, OpEx and transport/delivery.
Part quality is outstanding. We can even control the rotation of the mold through the heat beam to intentionally make regions of the product thicker or thinner. For example, molding a water tank with an extra-thick bottom for durability, while molding the top of the tank thinner to save material.
LightManufacturing
NB: How scalable is the solar rotational molding technology and what types of products can be made with it?
KVK: Extremely scalable. Roughly 49% of the earth’s land area has sufficient sun for the solar molding process. Our largest system, at the moment, can rotomold tanks up to 2,000 gallons, boats up to 11 feet long and other useful products like furniture, toys, road barriers, playground equipment and much more. Most large plastic products are rotomolded, we just make the process cheaper and cleaner.
NB: Can you share any success stories or case studies that feature your solar thermal plastic molding systems?
KVK: We’ve molded for commercial customers since 2014 and have supplied end users including the U.S. military, all major cruise ship lines and hundreds of municipalities around the U.S.
Click here to subscribe to our daily newsletter featuring breaking manufacturing industry news.
Karl von KriesLightManufacturing