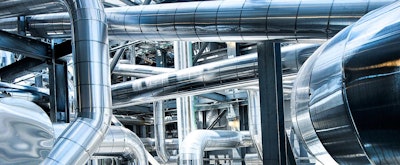
ExxonMobil and Polytechnic University of Valencia's ITQ researchers are developing a zeolite which will allow users to separate ethylene using 25 per cent less energy than with current methods.
Scientists from ExxonMobil and the Institute of Chemical Technology (ITQ) of Valencia's Polytechnic University and the Spanish National Research Council (CSIC) have developed a new potentially revolutionary material which could significantly reduce the amount of energy and emissions associated with the production of ethylene. This new material, along with other separation processes, could lead to a reduction of up to 25 per cent of the energy currently necessary for the separation of ethylene, as well as the associated carbon dioxide emissions. Results of the investigation have been published in the Science magazine.
Researchers at ExxonMobil and the ITQ have discovered that the new material, composed of a silica zeolite with a unique structure, can be used in gas separation processes such as recovering ethylene from currents that contain ethane and ethylene. Zeolites are microporous materials commonly used for adsorbent and catalytic purposes in chemical processes. In the case of the ITQ-55 zeolite, separation is performed with an unprecedented degree of selectivity at room temperature. Investigation results could also apply to the design of new materials to be used as adsorbents or membranes in different applications of gas separation associated with the fabrication of chemical products.
"Cryogenic distillation, the procedure which is currently used to separate ethylene on a commercial scale, is a process which consumes a lot of energy," explains Vijay Swarup, research and development vicepresident for the ExxonMobil Research and Engineering Company. "If this new material is applied at a commercial scale, it could significantly reduce the amount of energy and emissions associated with ethylene production. This is another excellent example of collaboration between industry and academy, centered on promoting solutions to improve energetic efficiency and reduce the carbon emissions of industrial processes."
Ethylene is a vital component in the production of chemical and plastic products frequently used in day-to-day life, making the search for alternate technologies to separate ethylene from ethane with a low energetic consumption turn into a very active field of investigation. Although chemical product manufacturers have evaluated a series of alternatives to cryogenic distillation, including new adsorbents and separation processes, the majority of these alternate technologies are hindered by low selectivity and efficiency, as well as the impossibility to regenerate adsorbents as they decompose with use due to the presence of contaminants.
The new ITQ-55 material is capable of selectively separating ethylene from ethane thanks to its exclusive porous and flexible structure. Created by heart-shaped units interconnected by large and flexible channels, the new material enables flatter ethylene molecules to pass, while negating access to the rounder ethane molecules. Therefore, the new material acts as a flexible molecular sieve.
"The ITQ-55 is a very interesting material, whose unique combination of pore sizes, topology, flexibility and chemical composition leads to a highly stable and chemically inert material which is able to adsorb ethylene and filter out ethane," explains CSIC research professor Avelino Corma, coauthor of the investigation. "We are thrilled with this discovery and hope to continue our fruitful collaboration with ExxonMobil," he adds.
Additional research must still be done before the new material can be considered for large-scale commercialisation. Further research will be centered on incorporating the material to a membrane for its industrial use, as well as developing new materials for gas separation.
"Our end goal of replacing cryogenic distillation is a long-term challenge that will require many more years of research and tests in and outside the laboratory," Gary Casty, head of ExxonMobil Research and Engineering Company's catalysis section adds. "Our next steps will be focused towards a better understanding of the potential of this new zeolitic material."
Chemical plants represent approximately eight per cent of the worldwide energy demand as well as approximately 15 per cent of the projected demand growth through 2040. As the planet's population and standards of living increase, so will the demand for consumer goods, construction materials, electronic devices and other petrochemical by-products. ExxonMobil's goal is to improve industrial efficiency to meet the increasing energy requirements of the world while mitigating the environmental impact.