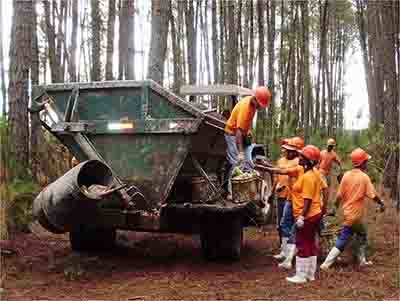
The pine chemicals industry is steeped in tradition and history. Tapping pine trees for gum resin goes back hundreds of years, when it was used for caulking ships. Today gum oleoresin continues to be collected through the tapping of pine trees and is refined into gum rosin and gum turpentine, both used in many consumer applications. Rosin and turpentine also are produced from crude tall oil (CTO) and crude sulphate turpentine (CST) co-products from pulping pine trees for papermaking. The CTO and CST are both separated into pure fractions in highly complex industrial biorefineries. In addition to rosin, fatty acids and pitch are also recovered when CTO is processed.
The rosin, fatty acids and terpenes from both sources are used in the manufacturing of adhesives, sealants, paints, coatings, soap, printing inks, papermaking chemicals, food additives, mining chemicals, disinfectants, perfumes, flavors, fragrances and vitamins, among many other common products. The global pine chemicals business is a multibillion-dollar industry.
Industry leaders in both natural forest settings and technology-driven manufacturing facilities share important goals: steady economic growth, implementation of value-added innovations; reduced environmental impact; stable workforces; and sustainable best practices. Why are these important? Companies are looking for ways to set themselves apart from the competition, but not only that — they want to build a more sustainable, innovative business. This is where lessons from the pine resin industry can help.
Innovation Takes Root in the Forest
In the 19th and early 20th century, pine tapping was big business in the U.S., where natural pine forests are plentiful. However, a growing, increasingly urbanized population and increasing labor costs took their toll, and tapping operations all but disappeared in this country.
Pine tapping today continues around the globe, primarily in emerging economies where labor costs are low. Traditionally, the collection of oleoresin has been done through a subsistence-like model: individuals working for themselves in communally owned forests, often in difficult terrain, working for low wages, and with limited or no mechanization or modern safety equipment.
Although the gum resin supply has steadily grown, the traditional model was reaching a critical juncture, as gum resin farmers were choosing to leave the forests for better paying jobs in cities, thereby causing labor and production shortages. Outdated forestry management practices further threatened resin output and in many cases threatened the survival of the forests themselves. In response, the industry began to develop new strategies and practices, with the goal of ensuring steady growth and long-term financial health.
Scientific Advancements
Identifying best practices began at the source — the trees themselves. Gum producers in Brazil began experimenting with selecting seeds from fast growing and high resin producing trees and reproducing these in nurseries and then planting new forests. They also began efforts to clone these more productive trees.
In the U.S., Gary Peter, professor of Forest Resources and Conservation, Genetics Institute, Plant Molecular and Cellular Biology Program at the University of Florida, has extensively studied new methods to increase the pine oleoresin flow within the trees through genetics. Peter has developed pine seedlings with genetic traits correlated with higher resin production. In a study of first-generation genetically bred trees, oleoresin flow was increased 1.4-fold and the number of resin canals within the tree increased 1.1 fold.
Historic tapping methods were also reexamined. One option — the “borehole technique” — involves drilling three small holes at the base of the trunk that intersect. Chemical stimulants, including methyl jasmonate and ethephon, are being applied to the tree during tapping, acting as tree hormones, if you will, to further stimulate resin output.
Growth of Plantation Forests
Brazil has now invested heavily in plantation forests planted from nursery seedlings selectively produced from high performance or cloned trees, and other countries are following suit. Rather than relying on natural forests, gum resin companies are buying or leasing land, and planting their own forests with optimal management and productivity in mind.
Many pine tappers are now working for companies that run the pine plantations. They receive a competitive salary, as well as safety protective gear and access to standardized equipment. Improved techniques allow the tapper to “touch” the tree less frequently. Now a single worker can productively tap 7,000-10,000 trees each year, compared to 1,500-2,000 trees tapped in a natural forest annually.
Best Practices in Processing
The industry has steadily become more efficient due to new innovations and state-of-the-art best practices adopted in the last several decades.
Manufacturers around the world have developed technologically advanced high-temperature and vacuum processes to separate and process the CTO and CST. Biorefineries are operating with substantially reduced energy and producing higher purity products with improved yields. This innovation has allowed the industry to create customer chemical solutions that meet the ever-changing needs of its customers.
The value of CTO and CST to customers is further maximized through “cascading.” Cascading is the use of biomass co-products as feedstocks to create another new product. It requires efficient use of resources throughout the value chain to take advantage of each new product’s co-products in order to create yet another product, until 100 percent of each co-product’s potential has been harnessed. Only then is the final residue suitable to be converted into energy or disposed of as waste. An example of this is the growing business in extracting sterols from tall oil pitch. These sterols are used in human food additives to reduce cholesterol. Formerly, the pitch was used as a fuel and today it is another valuable feedstock for value added products.
Quest for Continued Improvement
These advancements in the forest and factory help ensure steady supplies and solutions that have environmental as well as economic and social value. And the innovation will continue.
“The pine chemicals industry needs more sharing of gum resin research and best practices in order to continue to move forward,” says Alejandro Cunningham, founder of AR Eldorado, a pine resin chemicals consulting company and an expert in pine resin issues.
On that end, the Pine Chemicals Association will begin offering gum resin companies best practice training seminars, as well as continuing their educational courses on processes to more safely and efficiently recover CTO and CST.
In taking stock of their own innovation and sustainability efforts, manufacturers who use pine chemicals can rest assured that the global industry at the beginning of the value chain is continuously improving its stewardship of this valuable renewable resource. The pine tree continues to be an extremely valuable global resource for chemicals as well as for its many other uses.
Charles Morris is president and CEO of the Pine Chemicals Association, the only association dedicated exclusively to promoting the growth, success and sustainability of the global pine chemicals industry.