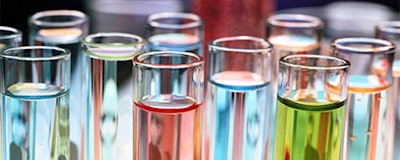
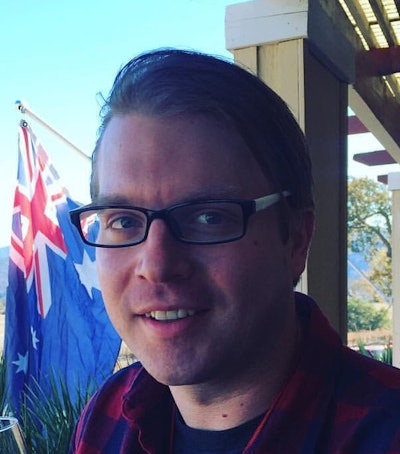
It seems as if almost every few months, there’s another story in the news about a tragic accident at a petroleum or chemical processing facility. In the first half of 2018 alone, there have been at least five such incidents resulting in untold millions of dollars in damages to facilities and surrounding communities, more than 180 injuries, and three worker fatalities.
Since 1998, the U.S. Chemical Safety and Hazard Investigation Board (CSB) has been tasked with investigating major petroleum and chemical processing-related incidents. Having investigated nearly 100 such incidents, the CSB has developed more than 800 recommendations targeted at improving the safety of operations at these types of facilities. Over the years, one recurring theme has emerged.
The CSB frequently cites process safety management (PSM) system improvements as a fundamental strategy for preventing process-related disasters.
Even though PSM standards are enforced by OSHA and are a key component of EPA Risk Management Plan (RMP) Rule requirements, government oversight alone has fallen short of fully preventing process-related disasters at covered facilities. Therefore, it’s up to facility owners and operators to actively pursue improvements to PSM systems above and beyond the level required by the regulations if they wish to protect themselves and the communities they serve from disastrous consequences of these incidents.
Management of Change (MOC)
MOC is a central component of any effective PSM system. Recognizing this, both OSHA and EPA specifically require facilities to manage changes to covered processes through the use of a formal MOC program. Even with processes that are not explicitly covered by these standards, the CSB has stated, "it is good practice to do so, irrespective of the specific regulatory requirements."
To satisfy MOC requirements, facility operators must establish and implement written procedures to manage changes to process chemicals, technology, equipment, and procedures, as well as changes to facilities that affect covered processes. Certain organizational changes (e.g. mergers and acquisitions, reorganizations, staffing changes, or budget revisions, etc.) that affect a covered process will also trigger MOC requirements. As a general rule, if an organizational change directly or indirectly necessitates changes to a covered process, an MOC procedure is required to ensure changes are implemented in a safe manner.
For each process change, operators must consider:
- The technical basis for the proposed change
- Potential impacts to safety and health
- Necessary modifications to operating procedures
- Time period for the change
- Authorization requirements for the proposed change
In addition, MOC reviews (whether for permanent, temporary, or emergency changes) should contain these basic elements:
- A description of the change, including technical specifications and business justification
- An assessment of risks and potential impacts [i.e. process hazard analysis (PHA)]
- A description of necessary modifications to operating procedures
- Any necessary training for employees, contractors, or other affected individuals
- An anticipated timeframe required to complete the change
- An established workflow for change implementation, including assigned individuals and approvers
- Formal procedures for notifications and approvals at each workflow stage
- Any necessary updates to process safety information (PSI)
- Pre-startup safety review (PSSR)
- Post-startup evaluation, including evaluation criteria and follow-up actions
- Systems for planning, scheduling, assigning, and evaluating change-related action items
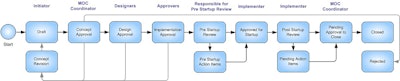
Figure 1 illustrates a simplified workflow diagram that can be applied to a planned process change. The workflow begins in the request stage, upon which the draft request proceeds through a series of approvals before entering the pre-startup safety review (PSSR) stage. If the change request is rejected prior to the PSSR, it is returned to the draft stage for revision. Following a successful PSSR, the change is approved and physically implemented. Following implementation, the change proceeds through the post-startup review to ensure the change has been implemented effectively and according to plan. Any necessary follow-up actions are identified and implemented prior to final approval and closure. It is important to remember that this diagram is for general reference, as individual change workflows will be determined by the complexity of the change, number of approvals, and personnel involved, and other change-specific factors.
Best Practices and MOC Software
MOC programs that rely on paper or rudimentary software systems to manage the multitude of change-related documents, communications, and action items can quickly become disorganized and inefficient, especially for petroleum and chemical processors who must perform a high volume of MOC activities every single day. In such high-risk industries, it’s not difficult to see how this inefficiency could result in the same lack of process control and oversight that the CSB has cited as the cause of so many process-related disasters.
To overcome these inefficiencies, advanced MOC software solutions are available to help owners and operators in the petroleum and chemical processing industries efficiently and accurately manage the variety of risk analyses, workflow assignments, approvals, PSSR, and post-startup reviews, training, notifications, and action items necessary for an effective MOC program, all within one simple and easy-to-use system.
An effective MOC program should provide a transparent, accessible, and traceable system for ensuring that process-related changes are performed only after full assessment of risks and controls, and with appropriate authorization from responsible personnel. MOC program benefits extend well beyond compliance with PSM, RMP, and other standards, and an increasing number of facility managers are recognizing the value of MOC to address a wide range of changes that may present safety or environmental risks.
Multi-tenant cloud solutions that can be accessed anywhere, whether on-site or in the field, provide the greatest value for complex facilities with large numbers of personnel and extensive change management requirements, as well as for multiple distributed facilities where standardized, uniform MOC procedures are a must. The best MOC solutions even allow users to submit and modify change requests, perform risk analyses, conduct inspections, issue approvals, and manage action items directly from their tablet or smartphone.
Petroleum and chemical processors should consider technology resources like a dedicated MOC software solution if they want to maximize MOC program and PSM system performance at their facilities. Not only do such solutions help simplify compliance, reduce costs, and provide a solid framework for a highly-refined MOC program—they ultimately help you ensure the safety and security of your facilities, your workers, and the communities you serve.
Greg Duncan is an EHS & Sustainability Expert at VelocityEHS, the global leader in cloud environment, health, safety (EHS), and sustainability software. To learn more, visit www.EHS.com.