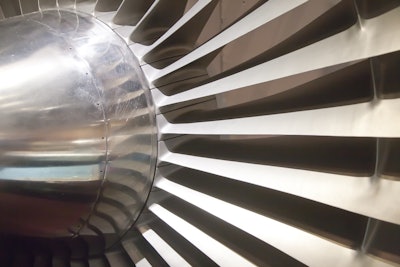
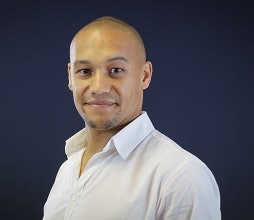
“You’re only as strong as your weakest link.” We’ve all heard the phrase, and it would be easy to apply the concept to obsolete parts in the supply chain. However, this doesn’t have to be the case.
Despite having a turbulent few years, manufacturing in the US is starting to revive. In fact, Pam Lopker, president, founder and chairman of QAD, recently stated that the sector is “enjoying a resurgence… fueled by tremendous progress in automation, engineering and quality management."
Lopker went on to explain that advances in automation are creating highly efficient facilities that can produce higher quality goods at a faster rate and this is keeping “US manufacturing at the forefront of global industry.”
That said, national industry has its work cut out. Fueled by the same advances in physical technology, like collaborative robots as well as a wealth of new digital tools, the international manufacturing market is also growing and changing.
According to an IDC report, FutureScape: Worldwide Manufacturing Predictions 2018, 60 percent of manufacturers will be reliant on digital platforms that will support up to 30 percent of their overall revenue by 2020. The report also predicts that by the end of 2020, 80 percent of supply chain interactions will happen across cloud-based commerce networks. This will also increase the resiliency of the supply chain and decrease disruptions by up to one third.
In theory, this is great news for American manufacturers using technology to provide a more reliable supply chain. However, there’s no denying that, as technology is advancing at an alarming rate, it is a challenge to keep up.
Rate of Change
Not only has the manufacturing sector had to keep up with consumer expectation and demand, but manufacturing processes have also undergone a complete technological revolution in recent years.
The first Industrial Revolution began in 1765 with the emergence of mechanization; the second followed a century later, with the development of electricity, gas and oil; and it was yet another century until the third revolution made its impact with the rise of electronics. And here we are, well into the swing of Industry 4.0 — the Fourth Industrial Revolution less than 50 years after the third.
If this timeline is any indicator, we’ll be hitting Industry 5.0 much sooner than we think — perhaps even before everyone has caught up with 4.0.
Quora contributor Don Stuart wrote an interesting article earlier in 2018 that explains why it feels that technology is advancing too fast for humanity.
“The story of mankind has been technological advancement outpacing human institutional ability to adapt quickly enough,” said Stuart. He explains that this is a problem that has always existed, even when the rate of industrial change was once every 100 years. He states, “The problem we’re running into is this: Rate of Change has been increasing, as the complexity and power of our technology has been increasing.”
Naturally, this has an impact on product lifespan and in turn, the supply chain.
Impact on the Supply Chain
The most obvious example of this can be seen in telecommunications. The original iPhone was released in 2007, and since then Apple has released 14 different iterations of the device, each touting new and improved capabilities and rendering earlier models obsolete.
While it may not be happening at quite the same rate, the scenario is similar for original equipment manufacturers (OEMs) of industrial machinery. It’s vital that these OEMs can offer their customers the most advanced solutions for the Industry 4.0 era, but resources are not infinite.
Therefore, parts, components and machines are becoming obsolete much quicker than before — traditionally, legacy equipment would remain largely the same, often for several decades When this obsolescence does occur, it creates a potential weak link in the supply chain that can bring operations to a grinding halt.
With this in mind, it is vital for manufacturers to develop an obsolescence management plan to ensure they can avoid unwanted downtime while replacement components can be found.
Consider this as an example. A bottling plant has a labelling machine that is reliant on a Schneider AC brushless servo motor, but the part breaks and cannot be repaired. This is a part that Schneider no longer manufactures. With the machine out of commission the plant comes to a halt. In this instance, there are several choices available to the business, but the time spent deciding on the best course of action only compounds the delay.
Establishing a thorough strategy to handle the impact of obsolescence involves creating an action plan for how to respond quickly should an obsolete part break (among many other things, which you can read about in EU Automation’s Book of Obsolescence Management [BoOM]).
For example, the bottling plant could opt to reverse engineer the servo motor and engage a specialist to manufacture a new one. However, this is time consuming and expensive. A much simpler solution is to speak to a specialist that can simply find you an exact Schneider AC brushless servo motor, like EU Automation.
Remember, discontinued doesn’t mean extinct. By incorporating an obsolete parts supplier that can source any discontinues parts or machines into your supply chain you have combated the potential break in your supply chain, without much effort at all.
America’s manufacturing sector is well-positioned to take center stage in manufacturing’s global renaissance, but businesses will miss out if they only focus on this big, technology-driven picture. You’re only as strong as your weakest link, but obsolete parts don’t have to be your downfall.
Leroy Spence is electronic obsolescence sales and business manager at obsolete parts supplier EU Automation.