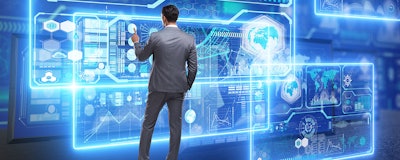
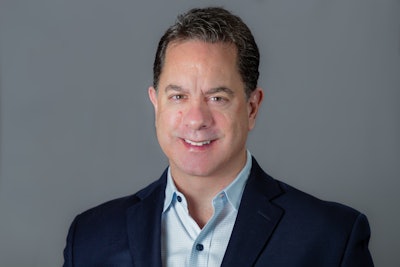
Manufacturing remains a critically important part of the world’s economic engine, but the roles it plays in advanced and developing economies has shifted dramatically. In developing countries, manufacturing operations deliver unprecedented new employment opportunities that are transforming societies. Of course, manufacturing remains important as a job creator in the developed world too, but in more mature economies, manufacturers drive productivity and efficiency gains and innovation.
Big Data is essential in achieving productivity and efficiency gains and uncovering new insights to drive innovation. With Big Data analytics, manufacturers can discover new information and identify patterns that enable them to improve processes, increase supply chain efficiency and identify variables that affect production.
Manufacturing enterprise leaders understand the stakes. A Honeywell Process Solutions-KRC Research study found that 67 percent of manufacturing executives planned to invest in Big Data analytics, even in the face of pressure to reduce costs. The majority understand that Big Data analytics are required to compete successfully in a data-driven economy, and they are making investments in data integration and management assets to achieve digital transformation and gain a competitive edge.
Obtaining Asset Performance and Efficiency Gains
Since manufacturing profits rely heavily on maximizing the value of assets, asset performance gains can lead to big productivity improvements — even if asset performance is only improved on the margins. By the same token, a reduction in asset breakdowns can reduce inefficiencies and prevent losses. For these reasons, manufacturers focus on maintenance and continuously optimize asset performance.
Machine logs contain data on asset performance. The Internet of Things (IoT) adds a new dimension with connected assets and sensors capable of measuring, recording and transmitting performance in real time. This data is potentially of great value to manufacturers, but many are overwhelmed by the sheer volume of incoming information. Data analytics can help them capture, cleanse and analyze machine data to reveal insights that can help them improve performance.
In addition to enabling historical data analysis, Big Data can drive predictive analytics, which manufacturers can use to schedule predictive maintenance. This allows manufacturers to prevent costly asset breakdowns and avoid unexpected downtime. Big Data analytics can have a significant impact: The Honeywell-KRC study found that Big Data analytics can reduce breakdowns by up to 26 percent and cut unscheduled downtime by nearly a quarter.
Improving Production Processes and Supply Chains
In an increasingly global and interconnected environment, manufacturing processes and supply chains are long and complex. Efforts to streamline processes and optimize supply chains must be supported by the ability to examine every process component and supply chain link in granular detail. Big Data analytics give manufacturers this capability.
With the right analytics, manufacturers can zero in on every segment of the production process and examine supply chains in minute detail, accounting for individual activities and tasks. This ability to narrow the focus allows manufacturers to identify bottlenecks and reveal underperforming processes and components. Big Data analytics also reveal dependencies, enabling manufacturers to enhance production processes and create alternative plans to address potential pitfalls.
Making Product Customization Feasible
Traditionally, manufacturing focused on production at scale and left product customization to enterprises serving the niche market. In the past, it didn’t make sense to customize because of the time and effort involved to appeal to a smaller group of customers.
Big Data analytics is changing that by making it possible to accurately predict the demand for customized products. By detecting changes in customer behavior, Big Data analytics can give manufacturers more lead time, providing the opportunity to produce customized products almost as efficiently as goods produced at greater scale. Innovative capabilities include tools that allow product engineers to gather, analyze and visualize customer feedback in near-real time.
By giving manufacturers the tools they need to do a deep dive on processes, Big Data analytics allows them to identify points within the production process where they can profitably insert custom processes using in-house capabilities or postpone production to enable a partner to execute customization prior to completion of the manufacturing process.
According to a Deloitte review of the rise of mass personalization [PDF], the ability to postpone production gives manufacturers new flexibility that allows them to take on made-to-order requests. Deloitte also notes that the ability to postpone production can “help reduce inventory levels and ultimately increase plant efficiency.” A streamlined manufacturing process is not only beneficial in its own right — it gives manufacturers a way to maintain efficiency while performing customizations.
Manufacturing’s Big Data Toolkit
So, what are the tools manufacturers are successfully using today to optimize asset performance, improve production processes and facilitate product customization? Here is a brief overview of essential Big Data analytics tools:
Data storage — the first step in putting Big Data to work is to have the ability to gather and store information. Manufacturers use data storage tools to maintain vital information on equipment, production processes and supply chain operations — data they can analyze to drive improvements.
Data cleanup tools — Big Data arrives in a variety of formats from a range of sources. It comes in structured and unstructured forms. To render it usable, manufacturers need a way to ensure data quality and integrity. They need data cleanup tools that allow them to transform unrefined information into a readable, unified dataset that multiple stakeholders can use. They also need data cleanup tools to standardize data and put it into formats that can be used by multiple applications and systems.
Profiling tools — Manufacturers need transparency into production and supply chain operations, and profiling tools can capture information up to the metadata level. This allows manufacturers to keep an end-to-end inventory of critical data, enabling them to maximize the value of their information.
Data mining tools — Success in manufacturing depends on being able to quickly access information to make the right production and supply chain decisions. Data discovery tools allow manufacturers to get the information they need when they need it.
Data mapping tools — Manufacturers must be able to understand how information flows through systems, processes and supply chains. Data mapping tools are ideal for helping manufacturers identify dependencies and pinpoint potential bottlenecks. They can also enhance security by enabling manufacturers to identify risk and leakage.
Data analysis — Analytics give manufacturers insight by identifying patterns, measuring impact and predicting outcomes. The ability to analyze equipment failures, production bottlenecks, supply chain deficiencies, etc., enables better decision-making.
Data visualization — Seeing is believing, and data visualization tools provide a picture of analytics results with unmatched clarity. User-friendly graphs and charts enable manufacturers to more readily comprehend the story the data tells and make needed changes.
Data monitoring — Data quality is of paramount importance, so manufacturers need a way to ensure compliance with data quality standards, oversee equipment performance and review production process efficiency. Monitoring tools enable manufacturers to automate quality assurance processes.
These are the primary tools manufacturers are using to put Big Data to work for them. By deploying these tools, manufacturers can maximize machine performance, optimize production, streamline supply chains and generate productivity and efficiency gains.
The Bottom Line on Big Data
As the most successful manufacturing leaders already know, Big Data analytics are no longer a “nice to have” option for manufacturing enterprises. Companies must find a way to improve efficiency and generate insights, and Big Data analytics provide the competitive edge companies need to succeed in an increasingly complex environment.
Those who are seeking a competitive advantage through Big Data analytics should look for holistic solutions that seamlessly integrate and manage critical data. When evaluating Big Data solutions, manufacturing leaders should ask about capabilities specific to their sector, including ways in which data management and integration can help them optimize forecasting, inventory management, procurement, stock replenishment, fulfilment, supply chain and other critical functions.
With the right data integration and management platform, manufacturers can finally leverage their data’s strategic value, improving operations, increasing profits and strengthening relationships with customers, partners and suppliers. Putting Big Data to work has never been more critical, and the time to get the data integration and management tools to unlock data’s value is now.
Rob Consoli is CRO at Liaison Technologies.