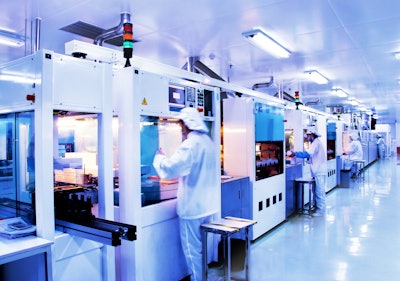
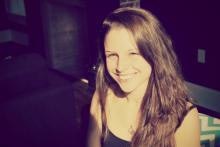
The ideal factory or manufacturing plant is one that is not just automated regarding development, but also when it comes to maintenance and operation. Even just a minor malfunction of major systems can have sweeping ramifications on productivity and efficiency. That’s why the regular maintenance and servicing of factory hardware is so crucial to operations.
Imagine a system that enables you to predict or identify problematic hardware before anything even goes wrong. You could effectively take action to repair, service or replace the equipment, eliminating the need for downtime entirely. Statistically, that would reduce your downtime to nearly zero percent. Believe it or not, that’s where plants and manufacturing systems of the future are headed. In fact, Fraunhofer demonstrated a prototype of a system just like this at this year’s Hanover Trade Fair, held April 23 to 27.
The cognitive predictive maintenance system will employ battery-operated acoustic sensors to process the audio signals of machines and hardware in real time. That information is then extracted and sent to a remote evaluation unit which can identify problems regarding the condition and performance of the equipment. In layman’s terms, it will use common audio signals to determine whether hardware will soon be on the fritz. While Fraunhofer’s system is just a prototype in its current form, it’s easy to see how this technology is poised to make a significant impact in the manufacturing industry.
Why the Future of Manufacturing Needs Predictive Analytics
A report from Stratistics MRC predicts the global predictive analytics market will grow from $3.89 billion in 2016 to $14.95 billion by 2023.
The obvious benefit of predictive analytics for any industry — manufacturing included — is that you gain insights and information early. For hardware maintenance, this is ideal because it means you can quickly identify problematic machines and service them before they experience a major malfunction. It’s also great for managing project and development scope because you can view information like inventory and material supplies, demand, efficiency and much more.
Let’s say you’re getting ready to put a new product or component into production, for example. You can use historical, performance and contextualized data to discern whether you’re likely to experience problems. You know even before kickstarting the process what you’re likely to encounter, and that allows you to come up with more efficient and precise strategies.
With modern plants growing in size — some occupy a land area of 2.8 million square feet — it’s becoming much more difficult for plant managers to identify problems or hardware errors with any kind of urgency.
But predictive analytics is about so much more than just early insights.
Identify Best Practices for Improved Efficiency and Revenue
So much data coming in brings along many new opportunities and insights you might not have gained otherwise. What this does is allow you a finer management and analytics view for improving your processes and systems. For example, if you notice a team is experiencing regular delays or productivity issues, you can address the problem right at its source. Maybe the team needs newer, more reliable hardware, or more in-depth training on how to use the equipment.
The same thing is true of the product development and manufacturing process.. In the past, plant managers were forced to use manual and more traditional means for identifying ineffective product specifications. Plant managers would either look at the hardware and machinery in use, the design of the product and its nuances or your crew and operating systems to ensure there weren’t any shortcomings. Even after all that, which could take some time, rebooting the entire process could mean a rinse-and-repeat scenario with even more delays.
Predictive analytics software, tools and related data can help you better identify these obstacles, and take action sooner, without the usual prolonged delays and downtimes you’d see with traditional plant management.
A More Accurate Look at Incoming Data
It’s likely you rarely put your incoming data under scrutiny. It’s possible, therefore, you’re bringing in the wrong or completely ineffective data for what you want to achieve. Without the proper assessment tools, however, you can’t accurately discern whether your data is truly valuable. All you know is whether the incoming information is useful.
Part of the natural order of implementing data analysis and predictive analytics means adopting the kind of tools and applications that can help you gain better oversight over your systems and operation. It’s not just about massive streams of data coming in, but instead about the right data that is both useful and relevant to your teams and processes.
By employing tools that rely on machine learning and data analysis and restructuring your operations to follow statistical process control methodologies, you will be able to proactively control operations, better manage quality and identify bottlenecks. More importantly, you will better understand the data that’s flowing in, how to use it and ways in which you can improve or evolve existing systems.
The Future of Manufacturing: An Environment of Continued Growth
All manufacturers and plant owners are interested in both quality control and optimized operations with reliable processes and systems. You must balance elements like factory or plant uptime, timely measurements and maintenance, product or quality control, staff productivity and much more. And you must track, optimize and maintain all these things over the course of your business lifecycle.
Predictive analytics and the data that flows in from such systems will allow you to better manage all these common and core components, but also enables you to strive for continuous improvement. What is more vital to success than continued growth and development?