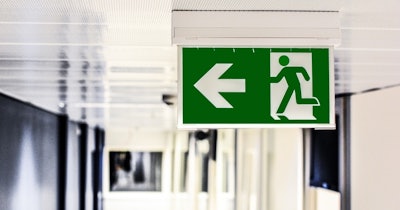
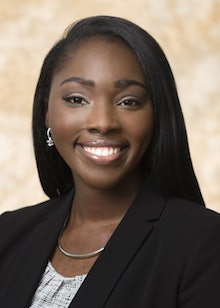
From hurricanes to earthquakes, to wildfires to landslides, manufacturers need not look any further than the traumatic events of 2017 to appreciate the importance of emergency preparedness and having an effective Emergency Action Plan (EAP). According to a recent survey by the National Oceanic and Atmospheric Administration (NOAA), the United States alone nearly set a record with 15 disasters in 2017 thus far, which have all been classified as “billion-dollar events.” With disasters on the uptick around the world, it’s time to make emergency preparedness a priority.
Typically, manufacturing companies involve sophisticated machinery, multiple facilities and key components produced across various geographic areas. In consequence, because it takes only one emergency at one location to cause production delays and/or facility shutdowns, the lack of an effective EAP can be critical to the welfare of manufacturers. To avoid such grave disturbances, this article will address some of the most important aspects you should consider when planning for an emergency to ultimately furnish your company’s survival.
Adequate Evacuation Procedures Are a Must
Since every organization is susceptible to an emergency at any time, sufficient evacuation procedures are essential. An ill-equipped, disordered evacuation can result in physical harm, property damage, exorbitant financial loss and even legal consequences. Considering that emergencies can range from violence, fires, natural disasters, widespread data loss, chemical leaks/explosions and equipment malfunctions, you should have evacuation procedures that are narrowly tailored to each specific type of emergency. For instance, evacuation procedures for a hazardous leak should differ from that of a tornado. Generally, evacuation procedures should include:
- Both primary and secondary exit routes that are clearly marked, routinely inspected and able to harbor the number of evacuating personnel.
- Measures for disbanding vital operations and, when safe, procuring anything that could likely become a danger if left neglected or unguarded due to the evacuation.
- Facility sweeps to assure the safe evacuation of all personnel.
- Methods to preclude entry and/or re-entry by unauthorized individuals.
- Plans for assisting both visitors and disabled employees.
- Strategies for those who do not speak English or the predominant language of the respective area.
Communication Is Key
Another major component of an effective EAP is communication — an EAP is useless if your employees aren’t familiar with it. Before the emergency ever occurs, the plan should be made available to all employees both electronically and by hard-copy. For example, the EAP can be provided in the employee handbook, on a bulletin board, on the intranet or via email. If you fear employees won’t review it unaccompanied, consider having a brief orientation to certify that each individual is aware of the plan of action.
Furthermore, due to the structure of manufacturing companies (size, multisite, interconnectivity, etc.) it is imperative to have proper communication systems in place before, during and after an emergency. Consider the following communication processes:
- Company-wide emergency notification systems that promptly alert employees of foreseen emergencies, unforeseen emergencies and emergencies occurring after hours.
- Emergency contact lists so that employees know who to contact with any questions.
- Reporting measures to account for all employees after an emergency.
- Utilization of safety-check features via social media.
- Departmental team leads to directly assist employees.
- External and internal gathering points.
- Procedures for receiving aid from other organizations that may provide resources during an emergency (governmental agencies, hospitals, medical facilities, community organizations, etc.)
Test It Out
Likewise, an EAP must be well-practiced to ensure its effectiveness. To determine its adequacy, you should implement full scale drills that mimic real-life emergency situations. Drills should be conducted routinely or to the extent necessary to acquaint personnel with drill procedure. Even more so, consider conducting drills unexpectedly and under varying conditions. While performing drills, be sure to document:
- Date, time and location.
- Types of notification systems used.
- Number of evacuees.
- Simulated conditions.
- Amount of time to complete evacuation.
- Any issues or challenges encountered.
- Employee feedback.
Survival and Recovery
Lastly, while recognizing that employee and workplace safety should be every company’s primary focus, avoiding massive loss and quickly resuming normal operations after an emergency should also be included in the planning stage. Therefore, to ensure effective emergency preparedness, manufacturers should not only prepare a course of action for the emergency, but should incorporate methods for survival and a smooth transition in the aftermath.
As discussed above, having an effective EAP is critical, but it is equally important that you have a proper Business Continuity Plan (BCP) to warrant the continued existence of the organization during and after the emergency. Proactively creating an adequate EAP and BCP will help to protect both your workforce and operations. Particularly, the two plans should not be mutually exclusive, but should work collaboratively where the EAP covers workplace safety and the BCP involves the continuum of productivity. Ultimately, the mere purpose of the BCP is to safeguard survival, recovery and restoration. For that reason, the BCP should be representative of your organizational vulnerability with respect to emergencies. To assess the emergency vulnerability of your company, you should analyze:
- Past and/or recurring emergencies.
- Geographic susceptibility.
- Potential emergencies resulting from human error.
- Potential effects on infrastructure and major amenities (telecommunications, water, power, gas, transportation, etc.)
Taken together, without the appropriate emergency plans in place, manufacturers take a gamble of becoming prey to an emergency from which they cannot recover. Accordingly, consider revisiting your current policy to assess its adequacy and be sure to routinely inspect your emergency plans to determine whether any changes and/or updates are needed. All in all, it is paramount to understand the necessity of effective emergency preparedness in order for manufacturing companies like yours to be greater equipped to respond to any emergency, any time.
Miya Moore practices in the Labor & Employment Law section at Burr & Forman.