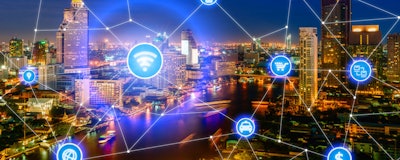
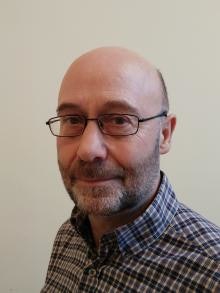
The Industrial Internet of Things (IIoT) involves a wide range of technology from semiconductors to cloud computing and artificial intelligence. Businesses can take advantage of this technology to make their processes more efficient, and they can use the digital technology of the Internet of Things (IoT) to transform their businesses and industries. The potential opportunities for IoT include customer and supplier relationships as well as internal processes.
Manufacturers are defining and prioritizing IoT projects in exactly the same way as they would treat any new technology — “it can be done” doesn’t mean “it should be done”: the proposer needs to build a business case.
But IoT projects can offer whole new business models such product-as-a-service, so the right group of people need to be involved to assess the opportunity and develop ideas to fit their organization’s priorities, timescales, budgets and culture. For example, to introduce its “Sigma Air Utility operator model,” with pricing based on the consumed quantity of compressed air, Kaiser Compressors needed to build instrumented, connected machines. If the machines fail, the revenue stops, so as with all ‘as-a-service’ business models, there is new commercial pressure to build reliable machines and minimize maintenance downtime. This approach needs broad involvement in decision making.
So existing processes to gather requirements and define plans for projects of this type may not be sufficient. As the apocryphal quote attributed to Henry Ford explains, “My customers would have asked for faster horses.” However, what counts as transformational can depend on your point-of-view. For example a new remote access system that allowed authorized process engineers to log in to their factory production lines triggered the comment “It changed my life” from a process engineer. This individual had previously struggled to accept night-shift stand-by duties. For him, the change has been transformational — even though the remote access needed is hardly new technology. Now, he volunteers for the night shift “…and if I can’t handle it online, I can usually guide the onsite team to fix problems.”
Remote access is entry-level IoT. The next step is to feed asset data into analysis and control systems. Taking an IoT approach rather than a traditional machine-to-machine approach pays off here, because in addition to solving remote and multi-site communication questions (an internet connection is all that’s needed), it also simplifies connection to suitable analysis software hosted in the cloud. The IoT approach supports many configurations, so, for example, if low latency response must be guaranteed, an IoT approach can integrate local (so-called ‘edge’) servers. The spectrum of capabilities was recently summarized by Brett Murphy of RTI as a range from ‘monitoring’ at the simple end, to ‘optimization’ where data from one or more assets can be analyzed and the results used by an operator to adjust settings for better performance, up to ‘autonomy’ where the IoT software makes the adjustments automatically.
These monitoring, optimization and autonomy examples are happening inside a manufacturer’s organization, and can be local to the production groups. They can be transformational because they may open up the next step for lean manufacturing initiatives.
However, it can be easier to see transformational effects from projects that offer something new to customers. Field service and asset management are the low-hanging fruit here. For example, GE Digital and PTC have formed a partnership to provide innovative solutions to companies like Elekta. Here, the transformation is due to the connectivity of the machines Elekta sells to its customers, not the connectivity of the machines it uses in its factories.
Predictive maintenance can be relevant both to machines in the factory, and also to products sold to customers. Rolls-Royce, introduced its TotalCare Services some 20 years ago. TotalCare employs a “power by the hour” model in which customers pay for service based on engine flying hours. Rolls-Royce analyzes engine data to manage customers’ engine maintenance and maximize aircraft availability. For security and availability reasons, ground-to-aircraft communications are independent of the Internet, using a specific Aircraft Communications Addressing and Reporting System (ACARS). Since its introduction, the scope of TotalCare has grown in parallel with the growth in sensors-per-engine, and the capacity to analyze large volumes of data per engine per hour. Now, the Efficiency Insight service includes Engine Health Monitoring, and tracks the health of thousands of engines operating worldwide.
Previously only relevant to low-unit-volume, high-unit-cost industries such as aerospace, the dramatic falls in sensor and communication costs have broadened the potential of these concepts to other industries. For example, food processing machinery makers Minerva Omega created the startup DSC Nexus, which has brought IoT capabilities to machinery, including slicing machines found on retail meat and cheese counters. For these relatively low cost machines, sensing is achieved by monitoring the electric current/voltage profiles during start up, during no-load, and while cutting. So a new power cord with an integrated sensor and Wi-Fi connectivity is all that’s needed to retrofit an existing machine. When the electricity waveform demonstrates it’s time for a new blade, appropriate operator or technician action can be scheduled.
While predictive maintenance takes center stage in the industrial machinery sector, there are other highlights in other sectors. The common theme is business justification based on achieving goals familiar to manufacturers since long before IoT:
- Reduce costs and improve operations
- Achieve competitive advantage by offering customers a better experience
- Open up new revenue streams.
The balance of these three goals varies, but they are always there, whether it’s connected car in automotive, cloud services for voice control of consumer goods, or smart metering and smart grid architectures in utilities. In agriculture, use of equipment across the whole business network is changing, from the supply of agricultural machines to the operation of fleets in the field using GPS, automated harvest collection and product identification and tracking. In construction, the trend towards off-site manufacturing and on-site assembly is being taken to the next level in OPTIMISED, a €7m EC (European Commission) funded H2020 Factory of the Future project focused on advanced manufacturing. According to Graham Herries, the EU ‘OPTIMISED’ Project Coordinator, this will apply a range of IoT technologies including RFID, edge computing, drones and deep learning to item tracking, personnel management using wearables, all based on building information modeling (BIM) management. In retail, IoT is helping deliver every supply chain manger’s dream of visibility and Walmart, working with IBM, is taking the opportunity to integrate ‘blockchain’ technology for distributed ledgers to ensure food security through supply networks.
As success stories such as these — from the ‘early adopters’ — become more common, the technology will be taken up by the majority in that industry, and it will become mainstream. But there are still challenges that need to be overcome, and different possible futures for industry.
Alan Griffiths is Principal Analyst at Cambashi.