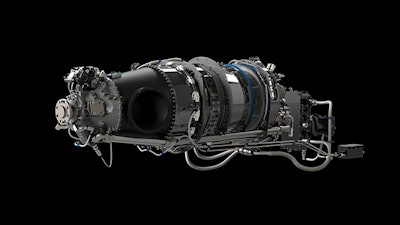
Pratt & Whitney Canada, a business unit of Pratt & Whitney, is rolling out a new engine model for its PT6 E-Series engine family, designed for Daher’s latest single-engine turboprop airplane, the TBM 960, and promising less scheduled maintenance.
"The PT6E-66XT engine, driven by more than 100 digital data inputs, offers the optimal combination of precision, performance and efficiency for an elevated and simplified flying experience," said Nicholas Kanellias, vice president, General Aviation, Pratt & Whitney Canada.
The digitally enabled single lever simplifies engine operation and allows for more precise auto-throttle and reduces operation and pilot workload. The engine control system reviews and processes all the engine and many aircraft parameters, making fine adjustments to fuel flow and propeller blade angle to deliver optimal power and efficiency during all phases of flight.
Pratt & Whitney said the control system uses the data to deliver constant engine performance along with increased engine take-off and climb power (+45 SHP mechanical horsepower) and increased thermodynamic power (up to 4% at International Standard Atmosphere conditions). The PT6E-66XT is also digitally connected through its Data Collection and Transmission Unit (DCTU), making full-flight engine data accessible on multiple platforms including mobile devices. Once the aircraft lands, engine flight data can be wirelessly downloaded, providing operators and maintainers with insights into engine performance and health.
The engine's scheduled maintenance intervals have been increased, including time between overhauls from 3,500 to 5,000 hours. The electronic control system removes hardware from the engine, resulting in a combined 40% reduction in scheduled maintenance.