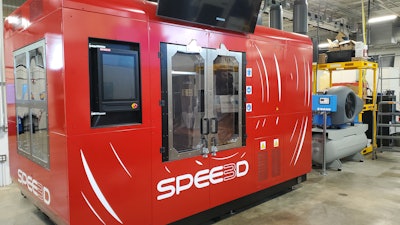
The Kummer Institute Center for Advanced Manufacturing at Missouri University of Science and Technology announced it purchased a large-format metal 3D printer from SPEE3D.
The purchase was based on feedback and input from manufacturers, who report that the process of acquiring traditionally manufactured parts has become increasingly difficult due to irregularities in the supply chain. The WarpSPEE3D printer is already being used for project work, which is helping S&T deepen the knowledge needed to help manufacturers transition into new production methods, such as geometry constraints, material properties and heat treatment requirements.
"For Missouri manufacturers to succeed on the global stage, additive manufacturing must become the new normal,โ said Dr. Richard Billo, director of the Center for Advanced Manufacturing.
Billo will oversee the Missouri Protoplex, an advanced manufacturing research and development facility that will anchor a planned manufacturing campus at Missouri S&T โ where the printer and other equipment will be housed โ when it opens in fall 2025.
In many ways, additive manufacturing is the opposite of casting, in which metal is heated until itโs molten and then poured into a die or mold. Forging, during which metal is heated to the stage of plastic and then reshaped using automated or manually applied compression, is another popular traditional manufacturing method.
Additive manufacturing is a different process altogether. The WarpSPEE3D builds parts by firing, at supersonic speeds, millions of metallic particles onto a build platform with assistance from a robot that controls the direction of the projection of particles to rapidly build the part.
Preparing an industry for the future
In addition to being used for manufacturersโ projects, working with the industrial-sized printer is giving undergraduate and graduate students at S&T a way to deepen their understanding of challenges confronting manufacturers. The WarpSPEE3D printer provides an opportunity for students to experience additive manufacturing by programming, documenting operating procedures, designing computer-aided drafting (CAD) models to test and developing and executing maintenance plans.
Along with other equipment that will be purchased over the course of the next 24 months, the printer is key to making workforce development more holistic. Plans are underway to modernize how S&T teaches manufacturing to undergraduates by incorporating technologies that will make it possible for students to gain hands-on experience with developing products and methods.
A key mandate of the $300 million gift June and Fred Kummer made to S&T in 2020 is connecting whatโs being researched, discovered and taught at colleges and universities to what the regionโs manufacturers need to compete in a marketplace thatโs increasingly driven by technology. The workforce development required to forge those connections, Billo says, goes beyond training those who operate the machinery.
Achieving common goals
Billo said that one of the driving factors in the purchase of the WarpSPEE3D printer โ as well as other equipment that will ultimately be housed at the Protoplex โ is that the manufacturer of the printer, SPEE3D, considers the close of the sale the beginning of an important relationship.
โFor additive manufacturing to evolve to the level of forging and casting, itโs critical for everyone across the industry, from the manufacturers themselves to the colleges and universities and tech schools to companies like SPEE3D that will develop the equipment, to collaborate on developing standards,โ Billo said. โAdditive manufacturing has made significant advancements relatively quickly, but like many technology-driven industries, itโs in its infancy.โ
It's the obligation โ and the opportunity โ to help an industry evolve in a way that will help Missouri manufacturers that has motivated him to invest in equipment from companies that are collaborators rather than suppliers. By participating in user groups, contributing to the development of industry standards, working closely with other colleges, universities and tech schools, and forging relationships across the supply chain, Billo says itโs more important than ever to prioritize achieving common goals when investing in equipment.