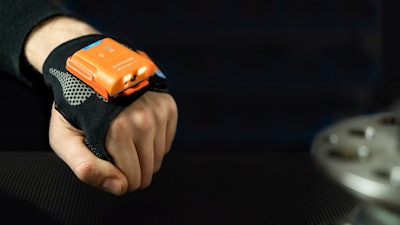
With increasing regulation across all industries, from data privacy legislation to technical specifications and product certification requirements, consistent traceability within often large and complex supply chains has never been more important. This is not only for compliance reasons, but also accurate forecasting to ensure companies deliver on promises made to customers.
Traceability ensures a stringent flow of data so suppliers and manufacturers can provide detailed information about what happened to a product, by whom and at what time. This is essential for industries such as the automotive industry, which sometimes needs to recall a model due to a defect. Traceability is also vital in the food industry: It helps ensure food safety standards are upheld. But as supply chains become longer and more fragmented, how can businesses keep up with increasing demand for faster product turnaround combined with a growing need for traceability?
ProGlove
One solution: wearable technology. Applications such as barcode scanners can help to streamline supply chain processes and keep quality at optimum levels โ not only addressing the need for traceability, but also transforming worker efficiency levels.
Increasing complexity
Consumer demands for a wider range of products requires manufacturers to handle and process an increasing number of parts and components for assembly. Moreover, regulations in some industries add further complexity to the process. This can present increasing challenges for businesses, especially those that operate with complex product variants and short product life cycles, which can block the possibility of a fully automated facility.
While the rapid growth of e-commerce business models may have simplified the retail world for consumers, it has increased the volume of work for vendors โ by as much as five times according to some research. As businesses move closer towards โjust-in-timeโ supply chains, focus and pressure is firmly on logistics operations to deliver efficiency within the supply chain. Moreover, the number of shipping formats available creates an added roadblock to automation and the surge for rapid fulfilment that comes hand-in-hand with peak periods only adds further complexity.
ProGlove
Augmenting the workforce
In order to meet compliance needs and unlock crucial efficiencies that can help businesses meet fluctuations in increased demand, organizations need to be able to access and capitalize on real-time data. Research from IDC predicts that more than a quarter of data created will be real-time in nature by 2025, and this is where barcode scanning plays a fundamental role.
The concept of barcode scanning within the supply chain has been around for years, enabling companies to increase visibility by tracking items along the product journey from manufacturer to the end point. Yet, the use of a conventional pistol scanner is fraught with challenges, such as the significant time lost for each worker due to the repetitive nature of picking up, using and holstering the scanner for each individual item.
Given the format of the traditional pistol scanner, the devices are also liable to breakages as they are easily dropped to the floor. And as the devices are not ruggedized, replacements are regularly required. This unreliability can be frustrating for workers as well as for organizations, as workers cannot operate with optimum efficiency.
Another drawback of the pistol scanner is that it can be easily lost by workers. This could be around the warehouse or factory, but itโs also possible that a worker may leave the scanner inside one of the boxes they are packing. Finding a scanner is an unexpected surprise for the customer, to say the least, but also results in economic losses for the company because they need to replace the lost scanner.
ProGlove's wearable barcode scanner.ProGlove
Instead, wearable technology with in-built scan functionality can deliver a number of benefits to address these challenges. Minimizing unnecessary and tiring repetitive actions and improving accuracy significantly increases the volume of work undertaken by each worker. With adjustable feedback options, such as acoustic signals, vibration and LEDs on the back of the hand, a worker receives immediate confirmation of correct product selection. This feedback not only minimizes delays and errors, improving productivity, but also minimizes worker frustration.
Display screens can also be connected to wearable terminals to provide workers with additional information, such as the location of the next pick. Unnecessary activity is removed as every movement is directly related to the task at hand. Augmentation of the workforce can rapidly make workers more efficient.
Wearables as a way forward
Regulations, technical evolution and customer demand all create an urgent need for accurate and efficient barcode scanning to deliver traceability and efficiencies within the supply chain. Organizations need to consider implementing solutions that streamline these processes and maintain optimal levels of quality.
Supply chains will continue to get longer and more complex, and many retailers face added pressure to fulfill promises made to customers. Fragmentation in supply chains is also on the rise, with a number of suppliers and components relied upon to work in harmony to make the entire supply chain function properly. Wearable technology can be a critical link to deliver productivity and efficiency and allowing organizations to quickly adapt to fluctuations in demand, giving them a much-needed competitive edge.
Axel Schmidt