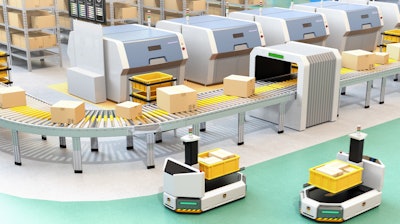
The recent pandemic introduced a great deal of chaos and uncertainty into every aspect of our lives. In business, and especially in global operations, it launched the warehouse industry into disarray. Warehousing had been accustomed to conducting repeatable processes that could be measured and managed and operations managers had confidence in what to expect day-to-day.
If the distribution center anticipated that 10 trucks were going to show up at the facility on a Tuesday morning, then 10 trucks would indeed show up – loaded with the expected goods, put in the expected staging area and distributed to the predetermined location within the warehouse.
COVID disrupted all of that.
If a facility expected 10 trucks, perhaps 17 or maybe seven trucks arrived with an array of goods. A number of factors contributed to the chaos – supply chain disruptions, truck driver shortages, lack of visibility due to outdated technology or even the shortage of warehouse workers. The warehousing environment became more dynamic where people at the facility had to be ready to tackle anything, and to do things differently, without preparation, and without repeatable processes.
When we consider the disruptions that have taken place in warehousing it is no surprise that safety has become a top-of-mind issue. Take a look at the statistics when it comes to safety in the warehouse.
According to the Occupational Safety and Health Administration (OSHA), there are more than 110,000 forklift accidents each year and 80 percent of those involve a pedestrian. A single one of those accidents can cost a facility $180,000 or more in direct and indirect costs. The TT Club, the international transport and logistics industry's leading provider of insurance and related risk management services, has reported that collisions caused by handling equipment, such as forklifts and lift trucks, are the second most common cause of freight damage and inventory loss and accounts for almost 13.6 percent of all claims. And lastly, $135 million in immediate costs each year have been due to forklift accidents, according to the National Institute of Standards and Technology.
So, how can facilities ensure they are making safety a priority? Here are the top three investments that warehouse and distribution centers should consider to help save time and money while creating a culture of safety.
Invest in Advanced Technologies
Warehouse facilities should consider investing in technology solutions such as artificial intelligence, automation, databases that manage metrics and historical information and remote diagnostic capabilities. Investing in easy-to-use and easy to deploy technologies can help reshape operations without having to reengineer a business.
Advanced technology tool sets give forklift operators an increased awareness of what's around them, without their head having to be on a swivel looking out for people walking in front of them or the need to slow down or change direction to avoid an unsafe condition. It allows a worker to focus on the task at hand.
In addition, technologies like remote diagnostics can allow a facility to collect data on each forklift operator and/or analyze the data remotely. Think about a facility with 25 to 1,000 forklift vehicles in a warehouse. If a facilities manager had to assess every forklift in order to really understand and analyze its safety history, it would take a significant amount of time. The more intelligence that's built into a forklift, a hand-truck or an overall system, the better equipped a facility is to ensure that it is being proactive when it comes to safety.
Invest in Labor
Employee turnover rates can certainly impact the overall operation of a warehouse. Lack of employees causes so many issues that can potentially impact the safety of a facility. Or employees might feel they need to work faster to make up for the lack of people available to do the work.
This can cause workers to feel unsafe and create unnecessary and avoidable accidents. And, when workers don’t feel safe at work, they don't want to go, and the problem becomes cyclical. When people feel safe in a way that doesn't inhibit their work, they want to stay, and they feel valued. Investing in enough labor and paying employees a decent salary is critical to keeping them onboard. Also consider rewarding workers who do make the facility as safe as possible. If they have a good “score-card” that shows they are incident-free, there could be perks associated with those that put safety first.
Invest in Training
Lack of training employees can lead to safety issues that cause unnecessary worker’s compensation and lawsuits. Without proper training, operating machinery or materials handling in a distribution center or warehouse can be extremely dangerous. Workers need to be trained on operating big heavy equipment and only people who are properly trained and authorized should be able to access these vehicles.
As operations invest in training their skilled workers, there should also be an appropriate balance between speed to move material, which is ever so important nowadays, and adhering to these safety protocols. Facilities also need to invest in training their people on how to understand and work with advanced technologies previously mentioned such as AI, automation, and remote capabilities. Every facility should have a minimum training requirement regulated by the industry and OSHA. Investing in additional training – and the proper training—should be at the forefront for all warehouses today.
Investing in technology, skilled labor and training will create a more repeatable and predictive environment in today’s warehouse and distribution centers. This will have a positive impact on warehouse safety and will ultimately save companies money and time as the industry continues to search for a new normal across operations.