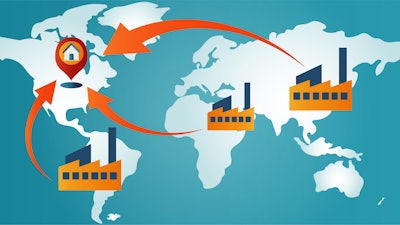
As manufacturers face complex supply chain challenges due to COVID-19, trade wars, and political and social unrest, reinvesting in near-shoring or reshoring operations can help build resilience and agility amid the turmoil. According to professional services firm PwC, shifting production from China could cut operating costs for US manufacturers by 23 percent if they nearshored to Mexico, and 24 percent if they shifted to another low-cost country (LCC) in Asia.
We recently chatted with Kevin Keegan, PwC Strategy Consulting Principal to get his thoughts on global supply chain diversification, technology tools that streamline risk forecasting and vendor visibility, and the practice of dual sourcing scenarios. Check out our conversation below:
Manufacturing.net: Now that we are one year into the pandemic, what are some supply chain lessons learned?
Kevin Keegan: Whether the pandemic created upside, downside, or required new supply chain models, a majority of industrial companies experienced quick stress on their supply chain management capabilities. From conversations with many of our clients, the most frequently mentioned learnings included:
Those that had risk sensing capabilities, end-to-end and consistent supplier terms, and detailed disaster recovery playbooks were able to make needed adjustments weeks before their competitors - saving real cost and/or capturing incremental revenue opportunities
Those that had cross-functional communication channels deep into the organization were able to solve issues faster and with innovations that quickly created new needed capabilities in areas like quick enablement of part substitutions and ready analytics to help improve supply assurance
Year-on-year supply chain management cost as a percent of revenue has been the driving metric for many industrial companies for too long. Over the past couple of decades, creating backup sources of supply and routings were considered a low value investment and were too often underfunded / delegated to third parties.
Truly end-to-end visibility into the capacity and liquidity of first, second tier, and sometimes third-tier suppliers is the only way to have confidence in relatively quick scaling of supply volume
Manufacturing.net: How are companies approaching global supply chain diversification?
Keegan: Currently, we see two ways that companies are working on supply chain diversification:
One is with an eye on the Social element of ESG (Environmental, Social, Governance practices that promote value beyond revenue and profit growth). The Social component here is the mindful promotion of diversity and inclusion in how direct and indirect suppliers are selected - so that those providing services and products to a company promote employment diversity and good employee management practices.
The second is a combination of good Governance and Environment practices. Here, supply chain diversification is defined as the purposeful and integrated achievement of an appropriate set of options for sources of supply, location of transformation and routes to move goods and services that can rapidly be enabled.
- It includes specific guidance on how to govern through disruptions - with clear accountabilities, required analytics and the like. Focus is on reducing risk for both revenue and margin goals in the event of both threats and competitive opportunities stemming from:
- Natural/health disaster
- Changes to trade policy or tax policy
- Labor actions and,
- Changes to the financial, capacity or ownership status of supply chain partners
This second definition can also include setting up supply chain activity to be ‘multi-local’ for purposes of lowering the carbon footprint, increasing the freshness/fulfillment lead time of products/services, and lowering import tariffs.
- It reduces risk of supply availability/risk of revenue and, when governed well, can help manage landed costs through how manufacturing and routing assignments are made in response to spikes in cost or new incentives that become available.
- Diversification also helps with responding to competitive threats. One example is when a government floats an RFP but requires high levels of local content in order to be considered for an award of work. Without the ability to spin up local market capacity, a competitor with better diversity may be able to win the work.
We see industrial product companies are approaching global supply chain diversity through an integrated and structured set of capabilities:
- Establishing a finite set of high probability scenarios for risks along the lines of those depicted above and assessing how, specifically, the existing supply chain structure and governance process is positioned to respond in a way that is timely enough. We see this work needing to be node-by-node and as a system with focus on identifying gaps/‘single points of failure’. In addition to looking at internal capabilities, this work gets into confirming capacity, financial structure and contract terms with key suppliers that would need to spin up or spin down their operations.
- Revisiting scenarios semi-annually or annually depending on the clock speed of the industry (i.e. duration of product life cycles, changes to base of customers or competitors)
- Determining priorities (with an investment budget/risk or investment return profile) to shore up weaknesses and a timeline to enact changes (considering enablers and dependencies)
- Setting progress reporting as a standard part of quarterly executive leadership discussions. Accountability is with the COO or SVP of supply chain.
- Creating executive leadership buy-in (and board awareness) for the diversification plan
- Educating line staff responsible to use tools to see issues/opportunities as they come up and how to respond. This requires playbooks by scenarios and ‘tabletop’ exercises on how to enact needed changes within the diversification levers that are available. This is the case whether it be a simple shift of some supply for a component from one supplier to another or a more complex change to set up an additional shift in a manufacturing site or spinning up a new logistics provider.
- Sharing the diversity they have enabled to analysts and shareholders in quarterly/annual reporting given this work aligns to the creation of long-term value
We are observing that adoption now is being driven by several factors:
- Over the past few decades many industrial product supply chain activities have been outsourced and channeled to singular suppliers often with globally spread out nodes based on where low-cost labor and IP is located.
- In 2019, tariff wars exposed industrial companies that got over-optimized and carried several ‘single points of failure’. The lessons on being priced out of the U.S. market when burdened with the additional import tariffs was significant for some companies across sectors (consumer, industrial products, high-tech)
- In 2020, the dependence on spread-out supply chain nodes without available options to move locations of supply or manufacturing was another driver as was the realization that there was too little transparency in financial solvency for supply chain suppliers and customers. Third, the pandemic revealed that contract terms to protect supply prioritization or inventory exposure risk were often missing or inconsistent.
- Across the last few years, ESG has become an important screening criterion for investors. Lack of supply chain options that improve ESG metrics has also become a driver.
- Collectively, these drivers have catapulted supply chain diversification/resilience to a board-level issue given the impact on share price/valuation.
We are also observing there are several challenges to creating impactful diversification within industrial product supply chain practices:
- Inertia, cost and culture.
- Inertia: It is hard for a company to quickly exit a site, a supplier contract or a capital expense that has several more years of depreciation.
- Cost: It is costly to exit a site (severance, inventory write-downs, investment in risk sensing tools, move expenses, higher overhead to manage more suppliers, loss of local customer goodwill).
- Culture: Optimization and goals for low supply chain cost as a percent of revenue are deeply ingrained in the way companies manage EBITDA. There is a major cultural shift needed to create resilience options, given diversification may drive up some costs but little utilization. While there is conceptual alignment to the risk protection that diversification provides and a nod to the ESG improvement that a diverse supply chain can provide, cost and margin will continue to dominate. Finding the right balance will require leadership from the top – with the right mix of quarterly results and longer-term value creation.
Manufacturing.net: In the last few years, there has been a lot of discussion about bringing manufacturing back to America. Are companies considering re-shoring operations?
Keegan: Onshore or nearshore assembly, configuration and test is beginning to be deployed in several industries (large format industrial products, high tech equipment, and sectors where increased concerns for product security is a factor). This option has been under review and in motion by companies in many sectors where labor content as a percent of manufacturing cost has declined, where fuel costs are significant and have increased, and as import tariffs have become less predictable for their products. More recently, rising attention to carbon footprint impact and reliability of supply have added momentum to this movement.
The U.S. executive order promoting job creation and supply security in several technology areas like semiconductor and battery manufacturing is creating a further set of tax, landed cost and public sector sales considerations to those industrial companies using these technologies and with a large U.S. corporate presence and customer base.
Industrial product companies are thinking through and enacting several supply chain footprint scenarios including expanding regional manufacturing capacity within the USMCA and postponed final configuration within their U.S. based distribution network. In turn they are asking their suppliers and partners to adopt regional strategies that help shift country-of origin profile, lead time and landed cost across sets of products.
We are observing that within industry subsectors there are companies moving quickly in this direction and others holding steady for the moment. What we know is that the incentives and ROI vary by company depending on how they compete (cost versus time), their current tax structures (corporate and indirect) and priorities for use of capital given how expensive it is to make sustained changes in the supply chain footprint.
Manufacturing.net: Looking ahead six months and one year, what should be the main priority for supply chains?
Keegan: While the term ‘resilience’ has been overused in recent months, the priorities we see for many companies as they look at their supply chain have included the essence of this term: increased emphasis on trust and predictability while remaining true to traditional focus on cost, time and quality.
We see that the reinvention of the landed cost equation and supporting supply chain structures is a predictability and trust priority. For some industrial product companies, landed cost now is going beyond part, manufacturing and freight costs to include cost predictability and total cost including import tariffs, costs associated with reactionary supply assurance and carbon offset costs. Likewise, lead time is increasingly focused on the total lead time of transforming raw material to a customer configured item even when volume is above forecast – not just the logistics lead time to get a finished item to a customer. Finally, supply chain quality is no longer just ‘the right product to the right place at the right time’ but is now including measures for excess and obsolete inventory, wasted capacity and stock-outs for many companies.
Security is another rising priority. The pandemic and tariff wars have pointed out that supply chains that are highly optimized for cost can have a latent and real high risk for reliability. Supply chain security is now being thought about in terms of data and intellectual property security, alternate sources of supply and routing are becoming a higher priority for supply chain management across more companies and industries.