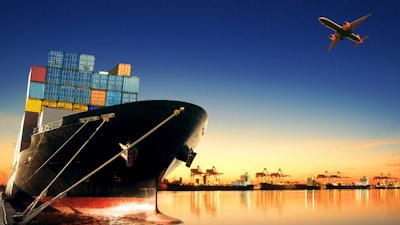
What challenges did logistics professionals not face in 2020? The global pandemic has highlighted troublesome areas that most consumers never knew existed — such as the massive rail and truck shortage at LAX once the ports started to roll again and clogged ports and truck queues in the UK.
Your customers may not care much about the logistics of how goods get from Point A to Point B. What they do care about is receiving their goods on time. This year, long delays were unavoidable as e-commerce volumes soared and carriers lacked the capacity to deal with peak-like volumes. By the time the holiday season rolled around, capacity constraints had bedeviled both retailers and consumers. UPS reportedly refused to pick up packages from several major retailers when they exceeded the limits “Big Brown” imposed upon them.
Delays happen. Mistakes happen. Unforeseen disasters happen. But that does not mean that businesses do not need a strategy to deal with these issues, if and when they arise. If 2020 taught us anything, it’s this — visibility and agility within the transportation network are crucial.
Chicken vs. Egg
For enterprises, shipping and transportation compose a classic chicken and egg scenario — they happen on both ends of the business.
First, companies need to make sure that their suppliers get them the correct items. Then, they need to ensure that these goods can be processed and sent out to customers. Both are equally important — you can’t sell what you don’t have, and you can’t expect repeat business from unhappy customers. So how do you define which has precedence? Where do you find the information you need? How much time does your organization spend simply checking tracking numbers on carrier websites?
Checking a carrier website? Yes, that sounds simple, because it is. But imagine if you were to actually calculate the time that your customer service representatives and logistics people spend hunting for answers as they try to locate a shipment? Chances are, you would be sick if you knew the actual cost associated with tracking.
Getting a tool that can quickly and easily advise your company of at-risk shipments — inbound or outbound — as they happen can add a tremendous amount of value back into your supply chain. This is not really about saving money — although you will certainly do that too — but about freeing up your team to do value-added activities by automating routine tasks.
Shortening the Supply Chain
Now that we have injected some visibility into the supply chain, let’s think about what that information can help us to accomplish. Visibility provides insight into which suppliers consistently have issues. As a result, procurement can now start to evaluate alternatives. With this insight, it might make sense to see if they can shift sourcing to local suppliers. There may be a cost implication, but companies have to look downstream at the costs of poor customer service.
The idea of reshoring is not a new one. While many companies could do it, many can’t — the cost is sometimes too prohibitive. Before ruling this out, you need to know the answer to the following questions:
- Can any of this be contracted out?
- Are there economies of scale at play?
- Can you push some of the fulfillment to more local 3PLs?
- Are there consolidation opportunities such as:
- Carrier service consolidation.
- Zone skipping.
- Holding open orders
Though your site may be the primary fulfillment center, there might be an option to contract out facilities in other strategic areas. Being closer to your customer can help you minimize disruptions.
Keep Your Customer Informed
Network design with new fulfillment centers and 3PL partnerships can get very complex and potentially expensive. However, again we can use visibility tools to allow the business to be proactive instead of reactive.
Let’s say a customer’s order is not going to make it’s scheduled 8:30 a.m. delivery. Two things can now happen. One, you call up the customer and explain the situation; or two, the customer calls at 5 p.m. yelling blue murder because without the delivery, they will have a downed line situation.
By 5 p.m. it’s too late to expedite the delivery, or ask the carrier to rectify the situation. Even if getting the delivery to the customer on time is not possible, keeping her informed will make her feel more valued than if she was ignored. Keeping your customers informed is even more critical when dealing with customs, either import or export. Customs agents only work specific hours. If you don’t catch something early enough in the day, you could potentially lose two days for delivery.
For example, if a full container load is coming into the LAX port and destined for Chicago, you may miss the rail cut. That means you are not only losing the two days at the port, but now two more days to get to the next train. Furthermore, due to time constraints, you may need to find a warehouse to transload and hire an over-the-road truck to make delivery times — all time, effort and expense you had not planned for.
Are you scared yet? Don’t be — these are just some of the issues that supply chain professionals run into every day. However, the pandemic has highlighted some of those areas more than others.
Giving your supply chain visibility into what is happening outside of your four walls is the starting point. With greater visibility, you can start to evaluate and be proactive about increasing the agility and flexibility within those networks. This visibility toolset will allow you to identify bottlenecks. You don’t know what you don’t know, and those bottlenecks might all be in the “transportation” side of things, but what specifically? Is it your customs broker, the carrier or your internal staff? Now you will have the information to do a positive identification and make adjustments.