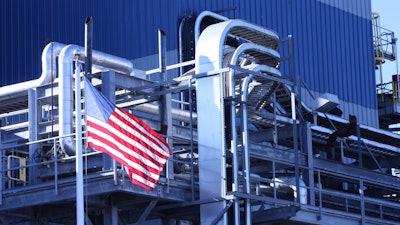
Economies around the globe have been faced with an unparalleled crisis as the COVID-19 pandemic spreads across continents, endangering people’s lives and forcing governments to put their citizens on lockdown. As small businesses shut their doors, nervous about the impact these closures would have, big businesses and manufacturing plants felt the impact, too.
China has seen a significant decrease in their exports, as have many other countries, but because the world is so heavily reliant on their products and parts, this may open the door for other countries to increase their manufacturing and exporting of goods. Automation, encouraging higher education and cutting costs are some of the important ways the U.S. can ramp up manufacturing. Here are some predictions on how the country can increase its manufacturing during this economic crisis.
In the past several decades, yes, traditional manufacturing jobs have begun to dwindle as robotic machinery and automated programs began replacing humans in factories, but the manufacturing industry itself still has an important impact on the global economy. Over the last 50 years, the industry has experienced a decline as other less developed countries were able to increase their own capabilities, which were successful because products can be made at a lower price due to inexpensive labor and access to raw goods.
The greatest problem facing the U.S. manufacturing industry right now is a lack of available workers who have been trained properly. In the past, our manufacturing plants relied on people to perform more mundane tasks that can now be completed by robots. There is still a lot of room for workers in the industry, but education needs to shift toward teaching people how to create and use programs and robotic machines that run the factories. With a greater number of people able to automate the industry, there would be a significant uptick in our ability to export in greater numbers.
How to Improve the Future of Manufacturing
Because the country has laws dictating a strict minimum wage, as the cost of living continues to increase, it costs the U.S. more money to manufacture products. For other countries like China and Vietnam, expenses are lower because of their lower labor costs.
In order for the U.S. to produce products at a reasonable rate, we need greater levels of automation. Some of the equipment can be costly up front, but in the long run, automation increases manufacturing speed and reduces labor costs. According to Justin Rose of BCG, one of the three largest consulting companies in the world, the U.S. has the potential to automate about 60 percent of its tasks, which would greatly increase the country’s ability to export at a higher rate.
Along with greater levels of automation is a need for people who know how to use, fix and create these tools.
A 2018 report conducted by Deloitte found that 89 percent of manufacturing jobs were unable to be filled because of a lack of educated workers. This means that shifting the way that we educate our youth will greatly impact our ability to ramp up manufacturing. Without workers learning the skills to work factory programs and machinery, we won’t be able to achieve levels of success and work towards more cost-effective ways to run our manufacturing industries.
There needs to be a greater push for coding to be added to classroom curriculums and an emphasis on learning trades or particular skills that manufacturing companies are currently seeking.
Another important element to increasing domestic manufacturing is through reduced overhead. Manufacturing involves a lot of exporting and shipping, which means these companies fly through packaging materials like shipping barrels, cardboard boxes and packaging styrofoam. To help reduce costs, look for the cheapest prices possible on these items. Implementing the use of eco-friendly, recycled packaging is another great way to reduce costs and help the environment. You can even find biodegradable styrofoam peanuts to keep parts safe during transport.
Domestic Supply Chains
Although one of the challenges facing the U.S. manufacturing industry is supply chain globalization, it is possible to shift back toward domestic suppliers. The reason that the supply chains have been outsourced over the last several decades is that parts from other countries are significantly cheaper, but over the last few years, things have started to even out a little more, making it only slightly less expensive to receive essential parts from other countries.
If the U.S. can find and use domestic suppliers offering materials as an inexpensive price, the country can build up the manufacturing industry.
Cory Levins is the business development director for Air Sea Containers.