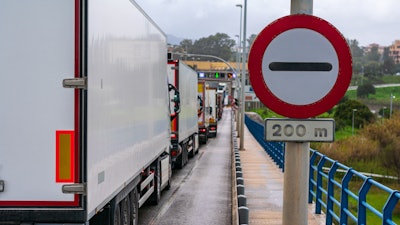
In June 2022, the U.S. Customs and Border Protection (CBP) implemented the provisions of the Uyghur Forced Labor Prevention Act (UFLPA), which restrict imports of products made in Xinjiang Uyghur Autonomous Region of China into the U.S. if they are produced using forced labor.
According to the Center for Strategic and International Studies (CSIS), CBP detained more than $1.3 billion worth of products at the border under the UFLPA in one year. CSIS added that at least 679 shipments have been denied entry and nearly 2,000 are still being held.
Industrial Media recently interviewed Trevor Stansbury, the president of supply chain transformation at Exiger, a SaaS company that helps corporations, government agencies and banks manage supply chains, to understand the impact of the Uyghur Forced Labor Prevention Act (UFLPA) on manufacturers and how they can identify forced labor in their supply chains.
Nolan Beilstein (NB): If more than $1B in forced labor shipments have been seized, how big is the market for products made using modern slavery?
Trevor Stansbury (TS): The industries impacted by forced labor are vast, and the $1 billion in CBP-seized shipments tied to forced labor represents the tip of the iceberg. To start to get an idea of the real scope of the problem, you have to consider the industries implicated and the markets they represent. In many cases, the pricing and product costs in these markets have been distorted by the long-term presence of forced labor in the supply chain.
Take, for instance, the $230-plus billion solar power market. A considerable share of the solar panels in the market have been made using forced labor from Xinjiang. If you extrapolate this example to the many industries that have become dependent on inorganically cheap goods, then the total market impact of forced labor likely reaches hundreds of billions.
NB: What are manufacturers struggling with the most since the UFLPA went into effect?
TS: One of the most difficult challenges for manufacturers has been, and remains, tracing the ultimate source of their goods, inclusive of material-inputs β things like metals, plastics, electronics, cotton, chemicals, powders and wires.
Historically, manufacturers have focused their attention on their direct suppliers - often referred to as Tier 1 suppliers. But with the combination of UFLPA and other international statutes aimed at securing supply chains, itβs no longer enough for manufacturers to merely know who their primary vendors are.
To navigate todayβs regulatory, economic and risk landscape, manufacturers need to be able to illuminate every level of a multi-tier supply chain for products, parts and raw materialsβ¦all the way to the proverbial βhole in the ground.β
Bills of material age quickly so this requires not only more sophisticated technology to capture the data, but a means to keep it up-to-date and accurate over time. It also requires manufacturers to address harder underlying challenges that if ignored, often frustrate their efforts - like how to align stakeholder interests by creating incentives for transparency. This typically requires a combination of proverbial βsticks and carrotsβ to garner the cooperation of suppliers below the direct or Tier 1 supplier.
NB: How can manufacturers better spot forced labor in their supply chains?
TS: First, if you donβt have a scalable, repeatable way to document and then monitor the outside, so-called n-tier suppliers, and individual parts and materials that go into a product or piece of equipment, then itβs impossible to discover when and where forced labor can enter your supply chain.
Armies of people and the proverbial βmother of all spreadsheetsβ wonβt hack it. This means that manufacturers must obtain item-level, and not just entity-level visibility, right down to the material-input level if they want to confidently root out forced labor in their supply chains.
The only realistic way for manufacturers to get this kind of visibility and granularity, is to leverage big data analytics and artificial intelligence. Modern supply chains are complex, interdependent and often span hundreds and sometimes thousands of external stakeholders. Automated product and software attribute characterization, network mapping and AI offers the only scalable solution to this problem, allowing manufacturers to tap into comprehensive open-source data to analyze supply chains on a probabilistic basis.
After manufacturers achieve visibility, the next step is continuous monitoring. Supply chains change every day and itβs vital that manufacturers implement solutions that allow them to monitor providers on a daily basis to ensure compliance with statutes like UFLPA while minimizing their exposure to supply chain disruptions.
The good news is that βitemβ and βentityβ-level supply chain visibility can often lead to transformational changes that yield preferential service levels and prices. In other words, measurable return on investment.
For example, we have seen several multinational corporations that have leveraged the kind of visibility I am talking about to not only achieve legal, regulatory and trade compliance objectives, but as a means to collaborate with their suppliers on the purchase of common or strategic materials from certain trusted and verified sources.
In those cases, UFLPA, USMCA, Conflict Minerals, REACH RoHS or Buy-America compliance may have been the original objective; but the 3-22% savings and service-level improvements achieved through βdirected buy contracts,β ended up being a differentiating competitive advantage.
NB: What can manufacturers expect from the UFLPA enforcement in the future?
TS: Weβre experiencing the preliminary stages of whatβs likely to evolve into a mature, global regulatory regime. The CBPβs updates to documentation requirements and the accelerating rate of enforcement actions suggest that manufacturers can expect stricter enforcement and compliance demands in this area.
In the past year, weβve also seen CBP expand the scope of issues itβs focused on β evolving from a targeted focus on Uyghur forced labor to a broader emphasis on all human rights abuses.
Another noteworthy trend that has emerged from early UFLPA enforcement is the industry-specific scrutiny. Weβve seen investigative reporting and congressional attention drive CBP enforcement in sectors like auto and solar. While enforcement actions target individual bad actors, this spotlight effect is likely to drive more scrutiny for all players within a given industry.
NB: What can manufacturers do to smoke out and remove forced labor from supply chains? Will they?
TS: In light of the current enforcement landscape, manufacturers must make every effort to proactively isolate forced labor from their supply chains. One obvious tool at their disposal is the revenue they represent to their vendors.
As a condition of purchase, manufacturers should require their vendors to disclose make/buy relationships for the parts and materials that go into what a vendor suppliers. Vendors should be required to validate their bills-of-material, making future business dependent on transparency into all make/buy relationships.
They should also embrace the possibility that these kinds of programs can actually improve buyer/supplier relationships, yielding more strategic relationships, enabling cooperation and collaboration on the purchase and supply of common material inputs, the standardization of material forms and sizes and, ultimately, an overall improvement in prices and service levels for everyone.
Vendors, in turn, must be provided meaningful incentives to be transparent and to provide required BOM and n-tier supplier information: It will help them maintain their business with manufacturers and help them avoid the potentially devastating consequences of a reported violation of the UFLPA or similar statutes in Australian, Canada, Germany or the UK.