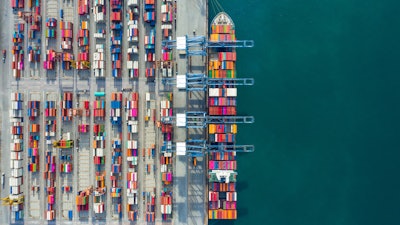
Blocked shipping channels. Weather catastrophes. Conflict. They are all disruptive and each one causes risks to the supply chain, including some with long-lasting effects.
Although your shipment of parts may not be directly involved, you have to be concerned about additional impacts that carry down from those risks.
We live in a global community. Any kind of interruptions to your supply chain can and will cause chaos. The question becomes: what are you going to do about it?
Here are Five Steps to Create Supply Chain Sustainability:
1. Risk Assessment
Identify vulnerabilities in the MRO supply chain – a risk assessment – and identify your tolerance for that risk. How critical is that spare part? What is the lead time? What is the cost? Are there multiple suppliers available? Can the part be commercialized? Reengineered? These are just a few questions that need to be asked.
Under normal circumstances, a supplier must meet a customer’s need for a part. That begins a chain of events where inventory is pulled from somewhere and then distributed by air, land or sea to a global community. That is your process.
Failure Mode Effects Analysis (FMEA) is the preferred method used in identifying risk. It is preventative, structured to identify and address potential problems or failures before adverse events occur. Among the steps in FMEA is the identification of potential problems and the impact or severity that would result. That is your risk.
Root Cause Analysis (RCA) is another option. However, while RCA is also structured to assess problems, that assessment does not happen until after the problem occurs. It is already too late.
Understanding your tolerance in the process is also necessary. How long can you tolerate not having the needed part? Does production cease without it? Is safety compromised when the part fails? Your assessment should consider that level of tolerance, as well.
2. Identify critical spares
Do you know your critical spares? Where are they? Sometimes it depends on who you talk to.
The plant manager may indicate their most critical spares are at the end of the process with the finished product. Finance may focus on the continuous material feed and the parts associated with that part of the system. The engineer looks at where the product is transformed from a raw product to an intermediary product. Talk to maintenance and they will say everything is critical.
At the end of the day, they are all right. It is truly based on the individual’s viewpoint, which may not be the full picture. You must base your identification of critical spares on the objective truth and not the personal truth.
A critical spare could have long lead times, require custom fabrication or could severely compromise production or safety when it fails, create downtime, have sourcing issues or grow obsolete.
You have a chain, and that chain is only as strong as the weakest link. That is what you are looking for when you try to identify critical spares.
Ultimately, your system and process requires:
Comprehensive ill of materials
Accurate min/max refill levels
Preventative maintenance schedules
Part failure analysis
Mean time between failures
Supply network
Process control charts
Machine and condition monitoring
These are the elements you need to consider when identifying critical spares.
3. Create a strategy
Now that you have the facts, you need to create a strategy. As part of that strategy, you must first define the goals and objectives, as well as the steps you plan to take to accomplish those goals.
Your strategy must incorporate the previous steps of risk and critical spares. Again, this is a system, and you are building upon the process.
This strategy needs to cascade down company-wide to departments and individual teams, no matter how tangential they may be. It needs to be clear. Everyone needs to know what you are doing and why.
4. Use Data
Data from your system of record is critical. It is used to understand your need. That data is used to stock inventory based on facts and figures, i.e. insight, and not on emotions or individual truths.
You also want to be careful. That data system may not monitor or store the information you need. If that’s the case, you just defined one of the risks involved.
Now, how much tolerance do you have for not having that information available? Can you afford having your maintenance team waste time searching for parts? Or your purchasing team struggle with order the right product without the proper information?
When identifying critical spares through a strategic planning and measurement process, it is important to be careful and collect only information you need. Too often, systems fail because they only evaluate what is coming from the system. If it is not in the system, that is fine, but you have to collect it in order to evaluate it.
5. Build a Process
Process and systems drive behavior. Everyone’s desire is to hit the bullseye. More often than not, that mark is missed. Still, that too, is part of the process, the continuous improvement.
We implement the process and systems to drive to the desired behavior. Here is a brief outline of steps to consider in building that process:
Develop an assessment
Define organizational needs and goals
Assess existing process and systems
Analyze gaps and create your plan of approach
Design future state
Design
Redesign process flows
Draft new procedural and supportive documents
Develop training materials
Communication plan
Change management
Implementation
Provide training
Support approval of process documents
Project and communication management
Maintenance
Maintain process and training material
Organize user evaluation meetings
Helpdesk and operational support
It is imperative that you also identify and understand the variability involved. That is the stuff that needs to be eliminated.
Remember, this is a journey. There are going to be improvements and setbacks. It is ok that the system is seemingly out of control. You’re going to take that system, eliminate errors and bring it under control.
As you walk through these steps, it’s not 1-2-3, etc. then you’re done. This is continuous improvement. Go back and repeat the process, recognize the feedback loops, understand the changes made and understand where you are and how you can improve. It is never-ending.
—
John Saleski is Senior Continuous Improvement Manager for Synovos, the leading global MRO supply chain management services provider and part of Electrocomponents plc.