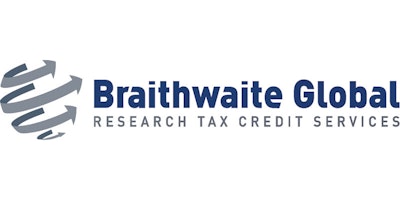
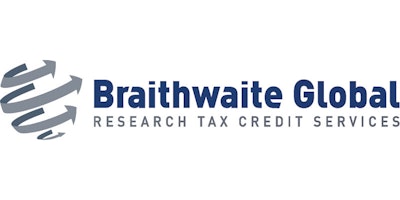
Most companies in the food and beverage industry understand the amount of time and resources that go into the innovations and efficiencies required to remain competitive in this ever-changing market. What many food manufacturers might not realize is there is a mechanism in place to reward and encourage that innovation. The Research and Development (R&D) tax credit, more commonly known as the Research Tax Credit (RTC), was designed as an incentive for U.S. companies to increase research spending. The credit was initially established as a temporary tax incentive that originally expired in 1985 and was temporarily extended 16 times since inception until it was finally made permanent as tax regulation in December 2015.
With the Research Tax Credit now being made permanent, the timing has never been more right for food manufacturers to take advantage of these often substantial credits that provide a dollar-for-dollar reduction in a companyβs tax liability. In addition to current year tax savings, the credit can generate a refund of taxes previously paid for open tax years (generally the prior three years). On top of all this, the credit can also be used as a carry-back for one year and a carry-forward for 20 years if your company does not have immediate utilization for these credits.
If this isnβt convincing enough, the rules for calculating and claiming the RTC have relaxed regarding qualifications and, more recently, regarding how it is calculated. So if your company has looked into the RTC in the past but was scared away by stringent qualification standards or the difficulty of the calculation itself, these recent changes might make you take another look. These changes help to enhance one of the most generous tax incentives available to U.S. taxpayers:
- The alternative simplified credit (ASC) method can now be elected on amended returns instead of just original filed returns. The ASC is equal to 14 percent of total qualified research expenses that exceed 50 percent of the average qualified research expenses for the three preceding taxable years. This method is less complicated and does not rely on antiquated data.
- The definition of prototypes has been more clearly defined.
- There are proposed regulations to clarify the definition of Internal Use Software.
In addition to the federal R&D tax credit, more than 40 states have an R&D incentive program. These state credits typically follow the Federal Regulations but have different tax rates and utilization methods. Taxpayers can benefit from the federal and state tax benefits to continue investing in R&D activities and growing the U.S. economy.
Now, who would think that food manufacturing could qualify for R&D tax credits? There is a misconception that R&D only occurs in laboratories of high-tech research facilities. The definition of R&D activity is quite broad and includes multiple industries and types of activities. The RTC utilizes a four-part test to determine what constitutes as a qualified research activity (QRA).
The first part of the test is that the activity must relate to a new or improved product or process relating to function, performance, reliability or quality. This could be anything from a new formulation for a new or existing product to an improved manufacturing process that improves efficiencies within your manufacturing facility. In an industry fueled by constant innovation and demands from the market, food and beverage companies should have no shortage of these types of activities, referred to as business components.
The second part of the test requires the elimination of a technical uncertainty. This means that the action must be intended to discover information to eliminate uncertainty concerning the capability, methodology or appropriateness of design for developing or improving a product or process. This means that as a food manufacturer, you have questions or challenges that need to be answered and resolved. That question could be whether your facility is even capable of developing a new product idea or improving upon a manufacturing process. More than likely, the uncertainty will revolve around the final design or ideal methodology of a product or process. What this means is that your company may have an initial idea of what they want and how they want to make it, but certain constraints or efficiencies are discovered during development which leads to changes and improvements made to these initial designs and processes. I like to think of this part of the test as the headaches during the development process that lead to changes and improvements to the manufacturing process or the product itself. A prime example of this for the food and beverage industry centers around the challenges faced involving regulatory requirements and activities and many of the changes that have to be made to ensure compliance.
The third part of the test requires a process of experimentation. This means that the taxpayer must engage in an evaluative process that is capable of identifying and evaluating one or more alternatives to achieve a result. Donβt let this one scare you off. This is when people often envision lab coats and beakers. Although those types of activities certainly constitute a process of experimentation, this includes anything from modeling and simulation, to a systematic trial-and-error methodology. In other words, this is the work being done to resolve those uncertainties mentioned above. The key here is the evaluation of alternatives. Did you analyze multiple designs? Did you use engineering simulation models to find weaknesses in a design and then improve on that? Did you develop multiple prototypes and run those through a series of performance or functional tests to determine a final design or ideal methodology for manufacture? Maybe your company has a very defined and formal process for new product development like a stage-gate process. This is a great example of a process of experimentation involving various βgatesβ in the new product development process where a new product has to meet certain parameters before moving on into the next stage of development. But maybe your company has a much less formal and rigid way of developing new products or new processes. These less formal processes of experimentation are no less qualified. Maybe you have jotted down an idea for a product or process on the back of a napkin, and now you and your team have set about to determine how to bring it to fruition. As you go through your development process, you will evaluate various ways of doing things or alternative designs for a product. This is your process of experimentation. Trial and error. Analyzing a prototype and a methodology and determining there is a better way, a better design.
Finally, the fourth part of the test requires that the activity performed must fundamentally rely on principles of physical or biological science, engineering or computer science. This is an easy one. The activities described above must depend on hard science. During your analysis, did you evaluate the physics of your product or look at the biology behind it? Maybe you looked at the thermodynamics involved in the process, or maybe you evaluated your process or formulation to ensure there would be no microbiological contamination. The examples of qualified scientific principles for this fourth test are endless.
So now that we have identified our qualified research activities, how does that translate into credits? These activities generate qualified research expenditures (QREβs) that fall into one of three buckets: wages, supply costs and contractor costs. Qualified wage expenses are identified through direct wages of engineers or primary research personnel along with support or supervisory personnel who affect the research.
The second bucket β supply costs β consist of items used or consumed in the qualified activity and prototype component/equipment costs. This could include ingredients used in the development of a new formulation during the evaluation of various alternatives. Additionally, this would include the materials utilized in the creation of a prototype component part or fixture. There is also the possibility of taking equipment costs for equipment purchased and modified specifically for the development of a new product or process.
The third and final bucket is contractor costs. These costs consist of payments made to a third party to perform qualified research along with fees paid to consultants or engineering firms. An example of this within the food and beverage industry would be any costs associated with utilizing a third party to provide certain tests on new product or equipment as required by a regulatory body. Additionally, if an outside party is building fixtures for the manufacture of a new product, or as part of a new process, these costs could also be taken as either a supply or contractor cost depending on the work.
Finally, it is important to know that there are certain activities excluded from the RTC even if they meet the four-part test and fall into one of the expenditure buckets above. These include:
- Research after commercial production.
- Duplication of existing business components.
- Reverse engineering/duplication.
- Funded research.
- Research conducted outside U.S. & territories.
- Routine quality control.
- Surveys, studies, market research.
As you can see, there are numerous opportunities for companies in the food and beverage industry to take advantage of a robust credit that has been around since the early 1980βs and has never been more accessible for small to midsize manufacturers.