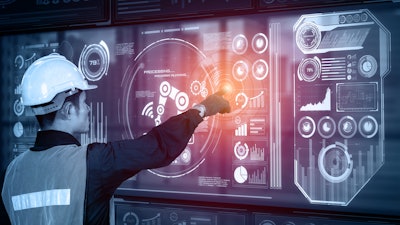
The manufacturing industry has been vexed by uncertainty in the past couple of years, as a result of everything from pandemic restrictions and workforce shortages to supply chain disruptions. The way manufacturers operate has changed a lot because of it, giving rise to new trends toward regionalization and localized supply chains. But partial, reactive responses aren’t enough.
Industry leaders are well aware that the landscape could quickly shift again. Change, in fact, is the only constant in today’s economy. With the accelerating pace of ground-shifting changes affecting industry, it’s more important than ever that manufacturers focus on building resiliency into their business operations and supply chains. To stay competitive and profitable, they must be able to adapt quickly.
Resiliency in an organization depends on flexibility—combining lean and agile principles of manufacturing—but it requires an organization-wide approach. You can’t just add flexibility to one part of your operation. Here are five essential areas companies should focus on to help prepare them for the unexpected.
1. Invest in Advanced Manufacturing
Industry 4.0 technologies, which have received a lot of hype over the past decade, overall have been hit-or-miss when it comes to practical applications, but there are several that have proven to be extremely useful:
- Automation and robotics, for example, have improved conditions on the shop floor while adding speed. They also help manufacturers address what has been a volatile workforce over the past couple of years. The Bureau of Labor Statistics reports that job growth continues trending upward, so manufacturers need to be proactive. Workers these days aren’t interested in performing the same repetitive tasks. Technologies such as co-bots, mobile robots and high-speed automation not only improve efficiency with regard to those repetitive tasks—increasing speed and reducing errors—but they free up workers to focus on higher-level tasks and upgrade their own skills. It helps an organization build in the ability to adapt to changes in the industry.
- Adding flexibility requires more than just automating certain processes. It’s important to design the entire process, including simulating how each production step is automatable. Simulation software can build a virtual representation of factories and production lines in advance of installing machines. It can create a digital thread of the product lifecycle—tracking operating indicators such as yield, throughput and time, for instance—which will allow team members to identify any difficulties that might crop up during production.
- Manufacturers can also employ visualization and lean methods, such as heat maps and value stream maps, to design a flexible approach to operations.
- During implementation, technologies like augmented reality also enable shop floor technicians at multiple sites to collaborate regardless of distance by sharing insights and best practices.
2. Create Diverse and Visible Supply Chains
The disruptions of the past few years underscore the importance of transparency and collaboration among partners in an increasingly diverse supply chain. New concepts are emerging, such as true market demand, which promotes the goal of an industry-wide single source of truth for supply. But for individual manufacturers, it must start with their own operations.
Leading manufacturers are implementing systems to incorporate real-time data from hundreds of internal and external systems, creating a transparent, integrated view of their entire value chains. Such real-time reports can inform manufacturers’ decisions on sourcing, while also being shared with the industry.
3. Focus on Quality
Resiliency in manufacturing depends on quality control that applies to entire lifecycles. A change in one step of the process—perhaps resulting from a new supplier or the relocation of a manufacturing process—can have significant ripple effects downstream.
New product introduction (NPI) test scenarios run through simulation are essential when a company changes setup, introduces a significant product modification, or experiences alterations to the shop floor. Testing can identify the pitfalls that will affect the quality of the final product. Teams should also be sure to communicate with stakeholders when undergoing those changes.
4. Open Communications
For all the advantages that technological innovations provide, the unexpected will still happen, whether within a company or throughout the industry (as recent years have shown). Strong, open communication with internal teams, suppliers and partners is critical to maintain resiliency throughout a product’s lifecycle. Honest discussions about topics such as risk tolerance, delays, the need for design improvements and sourcing challenges should be routine.
5. Encourage Engaged Employees
People are still the beating heart of any manufacturing company. Simulations enable manufacturers to be proactive, and visualizations can detect potential pitfalls. Meanwhile, automation brings unprecedented speed and efficiency. But human workers are still the key to everything. They analyze information from those technologies and make the decisions on how to use them.
Manufacturers should emphasize upskilling and cross-training to improve workers’ knowledge and capabilities. It empowers them to make quick, informed decisions and enables them to work together collaboratively, all of which improves a manufacturer’s resiliency.
Disruptions are to be expected in manufacturing. In fact, if the past few years are any indication, they may just be a way of life. That’s why flexibility and resiliency must be ingrained in manufacturers’ operations. Focusing on Industry 4.0 technologies, a diverse and transparent supply chain, continuously developing talent, proactive quality management and communication will help organizations thrive no matter the challenge.
But they can’t just focus on one or two of those areas—manufacturers must invest in all five if they want to succeed.