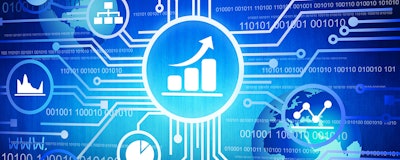
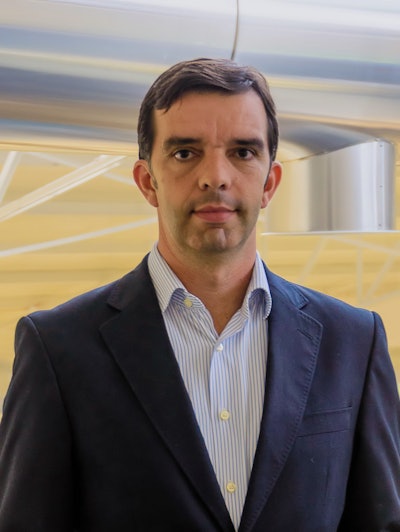
Industry 4.0 is based on autonomous Cyber-Physical Systems (CPS) which are fundamentally physical objects with embedded software, communication and computing power. The CPS will include manufactured products with their own intelligence and self-management capabilities.
Alongside smart products will be manufacturing equipment that is software enhanced to form Cyber-Physical Production Systems (CPPS). These machines will have their own computing power and leverage data from a wide range of embedded sensors and actuators.
This combination of CPS and CPPS is likely to trigger significant changes in manufacturing production and control with focus moving towards completely decentralized systems. Industry 4.0 advocates that the shop-floor will become a marketplace of capacity (supply) represented by the CPPS and production needs (demand) represented by the CPS. Hence, the manufacturing environment will organize itself based on what could be seen as a multi-agent system. This decentralized system, with competing targets and conflicting constraints, will generate a holistically optimized system, ensuring only efficient operations will be conducted.
The direct consequence is that centralized systems will simply cease to exist and for Manufacturing Execution System (MES) providers this will become quite a challenge!
Some of the questions arising are:
- How will MES cope with the marketplace formed by smart materials and smart equipment?
- Will we have a small MES running at each smart material or equipment?
- How will the MES ensure that manufacturing processes are followed, when the products and machines are taking decisions autonomously?
Companies operating in an Industry 4.0 mode will still need MES — just a different kind. Let’s call them MES 4.0.
MES 4.0 will be a completely new generation of systems, which must be able to cope with all the new challenges (and opportunities) Industry 4.0 presents. They will need to allow companies to build a solid, yet flexible infrastructure for the long-term transformation to Industry 4.0.
Let’s be clear here though: MES will remain a critical element in the manufacturing IT landscape. It must, however, cope with many new challenges, which I’d group in the following categories:
- Logical Decentralization
The MES may remain a physically centralized application, but logically acting in a decentralized way, granting autonomy of behaviour to the different shop-floor entities. Moreover, and because Industry 4.0 will not happen overnight, the MES must support concurrently centralized and decentralized models.
- Cloud and Advanced Analytics
CPS and CPPS generate huge amounts of data which need to be stored and processed. Cloud computing is an obvious infrastructure to give the speed and agility needed to handle this. Advanced Analytics are needed to fully understand the performance of the manufacturing processes, quality of products and supply chain optimization.
- Connectivity and Mobile
The connectivity in Industry 4.0 creates a true democratization of the production process. To embrace the complete efficiency this offers, visualization and control of the wide spread, autonomous elements cannot continue to be handled by fixed workstations.
- Vertical Integration
The manufacturing processes cannot be bypassed, so the MES must ensure that engineering, quality, compliance, logistic or any other type of processes are followed, despite the autonomous decisions taken by the smart shop-floor elements.
- Horizontal Integration
In Industry 4.0 the MES solution must be truly modular and interoperable so that all functions or services can be consumed by CPS smart materials, CPPS smart equipment or any other shop-floor entity and extended further into the wider supply chain.
Francisco Almada Lobo is CEO of Critical Manufacturing.