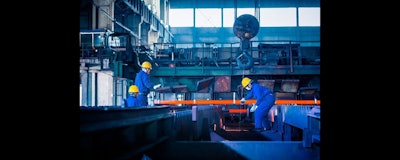
Sustainable worker safety is at the forefront of automated industrial production where everyone is accountable for their actions. This is precisely why it is important to minimize manufacturing errors when improving the efficiency of production operations.
Here are 8 steps that you can take to prevent potential hazards and improve manufacturing plant safety:
No. 1) Make Structured Safety Goals Mandatory For Everyone
Creating a culture of safety is only possible when every employee is free of any health risk and safe from accidental injuries even when the nature of operations is highly variable. Safe operations can be ensured when safe working becomes a behavior across functions and processes in the value chain. When every operation runs on structured safety goals and everyone takes up the responsibility of making operations safe, every action becomes symbiotic.
No. 2) Establish An Operating Model That Maintains Safety Standards
Every organization needs to establish a safety model where every initiative aiming to improve processes and procedures is executed in line with worker health and safety. Manufacturing plant safety must be the prime concern of every facility manager who plays a key role in every decision and action that impacts operations. The management team must implement safe standard operating procedures and must disseminate information at every level across departments from the top down.
No. 3) Align People, Procedures And Products With Safe Operations
Business operations must be aligned at every level while keeping safety as the focus of every process even as standards keeping evolving and business practices keep changing. People must work effectively while adhering to predefined processes and procedures where safety is an operational backbone.
No. 4) Develop An SOP For Supervisors
Supervisor management styles have a huge impact on the behavior of the maintenance crew and their performance. Supervisory efficiency can be enforced through one-on-one coaching, clarity of roles, and active management of responsibilities. Making the shift to safe operations requires facility managers to participate in the supervisory process and guide the production and maintenance workforce at the point of execution.
No. 5) Build Critical Performance Indicators
Facility managers can develop accurate ways of measuring the safety of operations by integrating critical performance indicators into operating systems. Traditional safety measures need to be combined with the right tools and reinforced across all business operations in addition to tracking all safety break points and near hits.
No. 6) Train Everyone On Legal Accountability
To achieve sustainable safety it is important to ensure that everyone is accountable for their actions and takes responsibility. Since every State is subject to different jurisdictions having unique liabilities including personal liabilities, every stakeholder involved in the production and maintenance process must be well aware of those liabilities. Documentation can help ensure that everyone involved works in a safe environment and is protected by the management. A safe culture should be in the company’s DNA and practiced in every process only then it is possible to gain a competitive advantage that comes from how safe operations are planned, implemented, practiced and managed.
No. 7) Design The Facility Layout For Worker Safety
The facility layout plays a vital role in ensuring worker safety as there are countless ways workers can suffer injuries. Whether your production facility is being built from scratch or undergoing renovation, worker safety can be enhanced by ensuring that the design includes a separate designation for traffic flow for pedestrians and machines like forklifts. All the doors must be strategically placed depending on their functioning and the safety of the swing direction. All physical impediments, exits, and obstructions must be made clearly visible with appropriate signage. All flammable and combustible products must be stored appropriately and facility managers must ensure strict compliance with process safety management requirements. In case of leaks and spills, emergency procedures and best practices must be implemented. All fire extinguishers and fire hoses must be placed throughout the production facility and all the employees must be trained on fire safety.
No. 8) Evaluate Equipment Safety
Conveyor belt safety is a critical cog in the manufacturing plant safety culture. Being economical and adaptable, conveyor belts are the most widely used systems across industries. They not only make distribution and transportation of goods quick and easy but also eliminate the need for manual labor. Since they are an essential part of automated industrial operations, facility managers need to be very careful in choosing the right system. For this you need to factor in the nature of your operations, the scope of your production facility, the budget, the time-frame, and the environment in which the system needs to operate.
In a nutshell, you can decrease the risk of accidents surrounding any type of conveyor belt by ensuring that it includes emergency buttons or pull cords to stop the system immediately. Installing interlocking guards will protect employees from overhead belts and falling products.
Fortunately today every industry recognizes the importance of manufacturing plant safety and proactively prevents hazards. If you want to work towards achieving truly safe operations, follow these 8 steps in your management style, maintenance schedules, material handling procedures and facility design to ensure every worker is protected and practices in a safe environment at all times.
Erich Lawson is passionate about saving environment by effective recycling. He has written a wide array of articles on how modern recycling equipments can be used by industries to reduce monthly garbage bills and increase recycling revenue. You can learn more about environment savings techniques by visiting Northern California Compactors, Inc blog