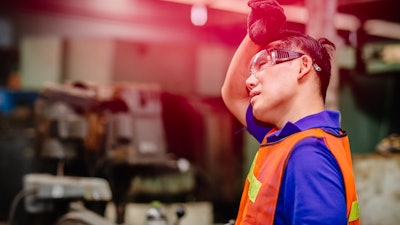
Heightened risk and strenuous operating conditions occur as temperatures rise, a combination that can have harmful outcomes. Heat often leads to impaired cognition and fatigue — both of which can increase the possibility of a serious injury or fatality (SIF). As experienced workers take vacations and time off, part-time and temporary workers less familiar with specific safety and operating procedures fill the void on-site, compounding the complex process of occupational safety hazards.
For Similar Content: Subscribe to Daily Newsletters
When these new workers arrive, who are less familiar with the signs of heat exhaustion and fatigue, the potential for heat-related injuries can increase. In fact, the Occupational Safety and Health Administration (OSHA) finds that 50-70 percent of fatalities in outdoor settings occur in just the first few days of working in the heat.
Summer is a clear hotspot for SIFs, however there are ways to combat the additional risks brought about by changes in the seasons.
Keeping Cool, Staying Safe
Leaders on the manufacturing floor are responsible for worker safety, but it does not mean they are alone when it comes to making improvements. OSHA, for example, recently released a draft standard focused on preventing heat hazards, and prescribes helpful guidelines for things like cooldown areas for workers and proper hydration measures.
Remember that while worker safety is foundational in these efforts, taking extra precautions for the heat is also a good business strategy. A manager that determines which jobs or tasks might take longer in the summer months can properly adjust staffing and output expectations, instead of being surprised by a slowdown.
As an alternative to navigating siloed OSHA guidance and advice on how to beat the heat, here are three immediate changes you can implement to better protect workers.
- Include summer heat in risk assessments. Summer heat is as predictable as winter snow, so each season risk assessments should include a thorough review of the jobsite for hazards that exist during the summer months. A list of areas to cover include measuring indoor temperatures in every area of a worksite, identifying areas for shade and shelter, ensuring equipment and tools are rated for expected temperatures, stocking personal protective equipment, and providing adequate drinking water access.
- Have a documented heat plan in place — and it needs to be enforced. With the surge in temporary workers that occurs during the summer, education should be a pillar of this plan. What clothes are recommended for doing particular tasks in the heat? How can workers spot the signs of heat exhaustion? What strategies exist to help workers develop a stronger tolerance to the heat? Answers to these questions should be part of the documented processes in place. Project and site leaders need to commit to encouraging frequent water and shade breaks, and also be able to spot signs of exhausted or heat-affected workers. For more in-depth guidelines, OSHA maintains a comprehensive library of materials on the subject.
- Encourage a culture of safety and vigilance. Conducting proper risk assessments for heat exposure, and having a comprehensive, documented strategy are good steps toward ensuring safety is ingrained in a company culture, but workers who bear the brunt of the risk on a daily basis should be empowered to voice concerns. Leaders must have an open ear for safety concerns, and any safety plan must allow for a clear line of communication for this to occur. Workers, whether temporary or long-time, should be encouraged to raise concerns about conditions, and leadership should be agile enough to make necessary changes if danger is found.
No one is powerless against the heat this summer, but there are many precautions that can be taken to mitigate risk. It will take leaders who prioritize planning, preparation, education and action to protect their workers.