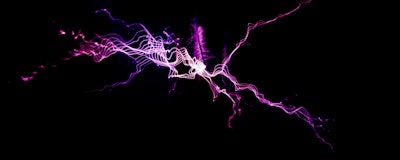
In your plant, there’s a good chance your facility’s electrical equipment is constantly being changed or updated (moves and adds) and maybe even improved. Thus, your electrical safety program should also address these changes.
In keeping up with new technology and evolving safety concerns, safety standards are periodically revised. Updated standards should be viewed as a benefit to facility and safety managers, bringing opportunities to modernize your electrical safety program and to stay up to date on existing trends in electrical safety.
Below, we outline the top five reasons for modernizing your electrical safety program:
1) Changes In Standards
If there’s ever a constant, it is change. The NFPA Standard for Electrical Safety in the Workplace (NFPA 70E), is updated every three years. While NFPA 70E isn’t adopted into federal law or OSHA regulation, but OSHA has a history of citing it as a best practice when electrical incidents occur.
OSHA’s general duty clause requires employers (your facility) to provide employees with a place of employment that is “free from recognized hazards that are causing or are likely to cause death or serious harm.” Because OSHA regulations are not frequently updated, they will often reference consensus standards (like NFPA 70E) as a best practice when issuing citations to the general duty clause.
Therefore, even though NFPA 70E is a voluntary standard, and compliance is not required by law, it effectively describes electrical hazards and best practices to mitigate them. Thus, failure to comply with this or similar guidelines can result in OSHA citations.
2) Training Will Always Be Important
For any worker who may exposed to electrical hazards, training is key. Employees performing electrical work need to understand the requirements of the electrical safety program, including the ability to recognize electrical hazards, know safe work practices and the procedures for protection against these hazards.
Non-electrical workers should also be trained to identify electrical hazards and recognize when electrical work is being performed so they do not put themselves or the electrical workers at risk. Training should be ongoing — do not underestimate the importance of retraining. Workers leave, new workers are added, and sometimes people simply forget what they have learned, or they may become complacent as tasks become routine.
Additionally, retraining is important if you consider the Normalization of Deviance phenomenon, which is described as “when people within the organization become so much accustomed to a deviant behavior that they don’t consider it as deviant, despite the fact that they far exceed their own rules for the elementary safety.”
3) Facility Updates And New Equipment
Electrical equipment in a facility is often moved, added, or reconfigured to keep up with changing production demands. Often, these changes may include updates to safety technology. Thus, the electrical safety program should be updated to address those changes.
So, when new equipment is added, a circuit is moved, protective devices get replaced or settings are changed and, generally, when any electrical wiring or cables) are modified in any way, it’s time to update your arc flash hazard analysis and revisit the safety program.
Retrofits and additions to existing equipment or reconfiguration of lines, are also a great time to evaluate if new electrical safety technology can be incorporated and will signal it’s time to update the electrical safety program.
4) Near Misses
According to the National Safety Council, almost 75 percent of all accidents are preceded by a near miss. It’s important to document and record near misses, minor accidents and close calls, especially those that have the potential for injury.
The overall safety culture in the facility gets stronger when reporting near misses are encouraged and not punished. If it’s not reported, the opportunity to mitigate hazards by taking corrective actions, including updates to the electrical safety program, are missed.
5) Employee And Facility Worker Expansion
A modern electrical safety program is all about teamwork. When a facility’s employee base has grown and/or when shifts are added, it’s a good opportunity to take the time to update the electrical safety program to demonstrate to employees — new and old — that the safety culture is strong.
Converse to expansion, if a plant experiences a reduction in staff, or significant employee turnover, this can lead to employees being asked to do other tasks for which they may not be adequately trained.
Therefore, changes that also affect the workforce should be a reminder to revisit the electrical safety program to assure that all workers are not only properly trained but understand their roles in advancing the safety culture.

Rachel Bugaris is a Business Development Manager at Panduit Corp, where her work focuses on electrical safety solutions for the workplace. She has a background in Research and Development, designing products ranging from absence of voltage testers to arc resistant equipment. Rachel participates and has held leadership positions in several IEEE committees, including the Electrical Safety Committee, Petroleum and Chemical Industry Committee, Pulp & Paper Industry Committee, and standards working groups (IEEE C37.20.7, IEEE 1683, IEEE 1584, UL 1436). Rachel has a Bachelor of Science in Mechanical Engineering from the University of Notre Dame. She is a member of IEEE and SWE. She has multiple patents and has written several technical papers on electrical safety topics.