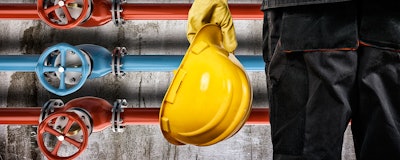
Despite attempts to ensure greater workplace safety in manufacturing, the industry still falls short. In the United States, there are more than 300 work-related fatalities each year in the manufacturing industry, according to the Bureau of Labor Statistics. In addition, approximately 12 million people employed in the industry and nearly 400,000 non-fatal injuries are still being reported annually.
While organizations continue to take measures to try to ensure employees are safe on the job, these actions are often reactionary in nature. Instead of just bandaging up an issue, manufacturers need to take a strategic approach to creating a proactive safety culture using software solutions. A software platform allows safety managers and plant operators to gain a holistic view of safety in the organization. With a safety solution, every employee is held accountable for implementing effective safety protocols and following the correct procedures while on the factory or plant floor.
By implementing a software solution, manufacturers can benefit from greater transparency and increased productivity. Cloud-based solutions also helps to streamline regular upkeep at a manufacturing facility for effective risk management. A safety software platform is also an effective tool for employees at all levels to utilize to help build a strong culture of workplace wellbeing.
Increased Transparency And Efficiency
With safety management software, plant managers and operators can obtain real-time visibility on performance within the organizations. With a single solution for safety management, there is also reduced time for tedious manual reporting in spreadsheets. Safety software allows manufacturers to easily and accurately track safety metrics such as Lost Time Accident (LTA) and Lost Work Day Case (LWDC). Using intuitive dashboards, a software solution offers detailed accident and incident recording and notifications can be sent automatically to key stakeholders within the organization.
Safety managers can also easily pinpoint key indicators of an on-the-job injury and take proactive steps to ensure there are no reoccurrences. Action items for the preventative step – such as installing anti-slip flooring in an area with a high rate of falls – are automatically assigned to key personnel. The safety management platform can then track and validate the completion of each task to ensure accountability.
Streamlined Operations And Maintenance
Creating a strong safety culture includes regular inspection and maintenance of manufacturing equipment to ensure they are performing at optimal levels. With a software platform, operations teams can instantly update the status of equipment they have inspected using a tablet. If there is an inspection and an employee notices that a safeguard is not in place or equipment is not working properly, then a corrective action is immediately assigned and the relevant team is notified immediately. The team is given a specific timeframe to complete the corrective action to reduce the possibility of any worker being harmed on that specific job preventing loss time due to an accident.
If equipment is malfunctioning, safety software can also send an alert to employees to ensure they do not attempt to use the equipment and hurt themselves. A great benefit of mobile software solutions is that they can operate online or offline which is ideal for a plant or factory where Wi-Fi can be spotty. This ensures greater accuracy in maintenance and operations reporting to expedite pressing issues in real time.
Training Management
A robust software solution can help to improve safety performance and adoption throughout the organization as it creates more widespread accountability. With ever-changing regulations, it can be challenging for safety managers and plant operators to monitor new training initiatives for every single employee. Using an effective training tool, managers can easily track training and reduce the risk of non-compliance.
There are elevated levels of severe injury cases in manufacturing and often, many are related to ergonomics. Using safety software, employees can schedule training and learn how to correctly unload equipment or utilize the right Personal Protective Equipment (PPE) while on the factory floor. Managers can also track attendance and completion of course modules and send automated reminders if they are missed. Using safety software, organizations will see boosted employee morale from taking steps to ensure incident and injury mitigation.
One organization needed a solution to manage its global network of manufacturing facilities in a single platform. Let’s explore how AVX is utilizing safety software to prevent workplace injuries.
AVX Leveraging Software To Create Standardization In Safety Management
AVX Corporation is a leading manufacturer and supplier of a broad line of passive electronic components, interconnect devices and related products. The company recently adopted a global, cloud-based enterprise software solution from ProcessMAP. With more than 10,000 employees at 20 manufacturing facilities across North America, Europe, Asia and South America, AVX was challenged with creating a consistent and standard process to ensure workplace safety and risk management. The company also had to manage an insurmountable amount of data from all of its global facilities to ensure ongoing process improvement.
As AVX employees handle high-tech electronic components for customers in the automotive, aerospace and medical sectors, creating a strong safety culture is essential. Leveraging ProcessMAP’s Incident Management, Audit Management and Action and Task Management solutions in five languages, AVX is able to gain a holistic view of enterprise safety and easily analyze trends using its data analytics platform to predict and prevent injuries. AVX benefits from real-time reporting, tracking and management of worker injuries and illnesses, as well as streamlined audit data mining and benchmarking. With in-depth business intelligence, AVX can manage safety initiatives and implement corrective and preventative actions to mitigate risks. In addition, the software solution also ensures AVX is OSHA compliant.
Creating a strong safety culture starts from the top. Management should build a culture that focuses on the safety and health of its employees, especially in manufacturing where employees have a high-risk of injuries. With a greater emphasis on improving safety performance and investing in the right tools, manufacturers will benefit from improved productivity, higher efficiency and no downtime. Ultimately, manufacturers that utilize safety software create an empowered and engaged workforce – which is an organization’s greatest strength.