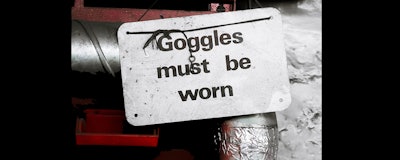
La Mesa, CA — With the start of a new fiscal year, a lot of manufacturing companies will be focused on profits and ROI. We should not be forgetting one of the most important aspects of our businesses, which is the safety of our employees.
If we want to keep our profits up, especially in a time where the manufacturing industry is experiencing a significant skills gap, then we need to make sure our skilled workers are protected. Safety and productivity go hand-in-hand, and this is why it’s important to get some extra help through software and hardware automation solutions.
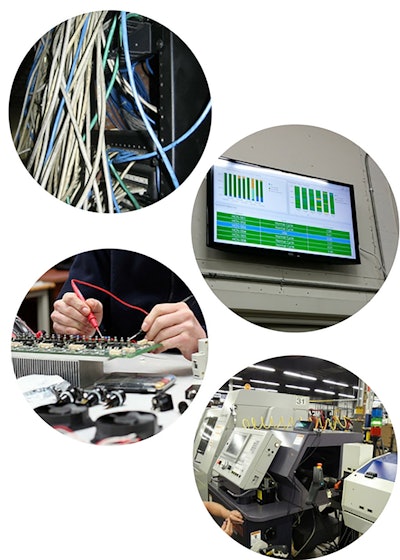
Here are 3 of OSHA’s Workplace Safety Violations from 2017 and what solutions you can use to counteract these specific issues in 2018:
No. 1) Ladders: If your cabling is in hard-to-reach places or up high, your employees likely dread grabbing a ladder or crawling into a space to see what’s going on with them. For the height problem, ladders were the No. 6 OSHA issue in 2017 with 2,200-plus citations. If there are too many tangled up in a certain spot, it can also be a magnet for dust, dirt, and maybe even critters to house themselves in, which can be hazardous to your employees’ health. This is why replacing a rat’s nest of cabling (no pun intended) can be fixed by upgrading to a wireless system for program transfers on your shop floor.
Fact: Even when you have ladders and other approved equipment for employees to get up to high spots, some employees may try to “improvise” to get to these hard-to-reach places. This is why fall protection training is the No. 9 OSHA issue, with 1,500-plus citations in 2017.
No. 2) Lockout/Tagout: When a machine is being worked on, proper procedure needs to be followed so other workers know not to switch the machine on. Because of improper lockout/tagout practices, OSHA reported 2800+ citations pertaining to this issue, making it their No. 5 issue in 2017. If workers have a good machine monitoring system on the shop floor, they can input a universal note reminding everyone a specific machine is to remain off until further notice. This note can be seen across the shop floor on monitors, helping with safety and monitoring utilization, which is a win-win.
Fact: It’s also worth mentioning that lights-out manufacturing, with machine monitoring as a crucial piece of this process to monitor OEE, can also help to lower workplace injuries. This is possible when some production can be done without manpower, taking pressure off of workers to try and complete what they feel to be unrealistic production expectations. Stress can definitely lead to accidents on the shop floor.
No. 3) Electrical Wiring Methods: While we touched on cabling issues previously, it is also extremely important that anything involving electricity on your shop floor be safe. OSHA agrees, since electrical wiring methods was their Number 10 issue in 2017 at 1,400-plus violations. If you have any doubts about how your machines are connected, if you have properly shielded cables, or if you are using the correct adapters, you should involve a manufacturing integrator. They can often come on site to do a free evaluation with recommendations or can make evaluations through photographs. They can make sure you are saving as much energy as possible and could point out potential hazards.
Fact: Aside from potential employee accidents, did you know that inferior cabling can also lead to dropped program transfers? Ask us about a case study we did with one of our customers on this very topic.
Amanda Rosenblatt is the Marketing Coordinator for Shop Floor Automations. The MFG Integrator will be celebrating their 20th anniversary of being in business in March of 2018.