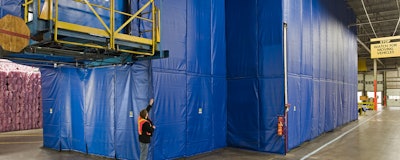
In any industrial workspace, air quality is an invisible factor that must be controlled. Several important aspects of in plant safety, including employee health and material quality, are directly impacted by indoor air quality (IAQ). Managing IAQ is easier said than done, as facility managers face several challenges, especially when controlling dangerous fumes in workspaces.
While the industrial or chemical processes involving volatile liquids are necessary to facility production, the fumes produced are difficult to control in large, open-air warehouses. Due to the fact that fumes or vapors can stratify in calm air due to the difference in density, particles are more likely to spread in an air space due to molecular diffusion.
To combat these obstacles, the four following facility layout tips can help facility managers control and minimize the dangerous build-up of fumes, ultimately improving the facility’s indoor air quality.
1) Implement Traditional Exhaust Systems
The process of removing the fume and vapor particulate from a facility is the first step to improving indoor air quality. Specifically, the volatile and diffusive fumes produced by cutting, grinding and mixing processes are most problematic, typically requiring local exhaust systems with fume hoods to adequately protect most warehouses.
Poorly designed buildings and facilities with inefficient ventilation system maintenance often suffer from sick building syndrome (SBS) due to the stagnant (or dead) air. This surprisingly common problem causes previously healthy employees to experience a range of physical issues; symptoms may include headache, dizziness, nausea. While these health issues typically vanish after leaving the building, workers battling these challenges are more likely to make mistakes, increasing the risk of accidents.
Even when area exhaust systems are added, facilities with open-air layouts will have challenges with the dispersion of noxious fumes and vapors.

2) Divide Workspaces With Fabric Curtain Walls
One way to address those challenges is to maximize the effectiveness of area exhaust systems with the implementation of curtain walls made from vinyl-encased antimicrobial batting. Working together, the contained area forces fumes and air particulates to be funneled efficiently toward the static exhaust system.
Anytime a space is to be exhausted, the smaller the space can be made, the smaller the exhaust equipment can be as specified. Partitioning around a source of fumes with a curtain wall takes full advantage of this relationship. As an added bonus, lower air velocity through filter media increases the effectiveness of the particle separation device and minimizes cleaning and replacement.
Curtain walls are also relatively easy to re-configure if a space needs to be enlarged or reduced, or the shape of the space footprint needs to change. No “de-constructuction” is required. Curtain walls are easily installed, can be trimmed around conduit, piping and ductwork, and can be anchored to the floor to withstand pressure differential across them. Depending on the application, a curtain wall can be suspended from the room ceiling or they can be supplied with a standalone framework to hang from. They are available as stationary, as well as sliding (suspended from roller track), and can be fitted with strip curtains, personnel doors, or high-speed industrial doors for full range of access to the space.Curtain walls also act as a very effective physical barrier on their own, blocking transfer of diffused vapor particles from space to space. Deploying these walls does not require facilities to sacrifice safety or functionality either. Curtain walls can be single layer fabric or multilayer insulated. They can easily be fitted with clear vision panels for visual communication between spaces. Flexible, yet very durable, they can withstand contact from machinery or product by bending, not breaking, in contrast to a hard permanent wall.
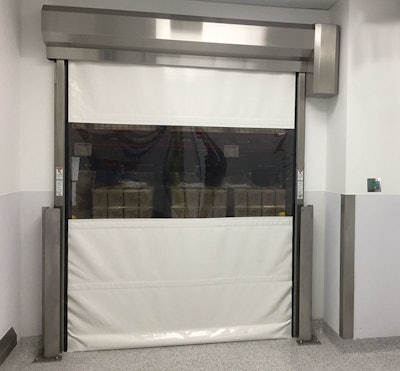
3) Airlocks And High-Speed Doors
The primary function of most industrial doors is to provide tight environmental separation, yet allow people and equipment to quickly and safely move from one area to another. In some instances, they are also an integral part of airlocks that form buffers between production and finishing areas.
Maintaining an air pressure differential between rooms, by pushing air from the cleaner side to the less clean side of the opening, is often desired when dealing with fumes. The ability of high-speed doors to accommodate site-specific needs is another consideration. These could include features such as vision panels, push plates or other activation devices, as well as magnetic locks and — perhaps most importantly — interlocking systems. Look for door systems that allow for wireless interlocking of airlocks.
A new generation of roll-up doors has come on the market in recent years featuring anti-microbial materials and other upgrades. These new features — along with their ability to operate at high speeds (up to 65 inches per second) and provide tight sealing capability — include ease of cleaning and durability.
Doors able to stand up to repeated cleaning with chemical solvents are at an advantage in most operations that involve particulate matter and fumes. They typically have a smooth, hard, non-porous surfaces resistant to microbial and fungal growth. Doors should also have a tapered surface and edges that all but eliminate “harborage” of dust or other contaminants and no sharp angles – as they can also harbor microbes. Some doors are even cGMP- and FDA-compliant.
Additionally, they should be corrosion-resistant (which is often a problem with older door systems); should use stainless steel side frames and shrouds; and should incorporate a lubrication-free design, since lubricants can attract particulates. It is also advisable to avoid doors with exposed fasteners and coils, as they will take longer to clean and could harbor contaminants.
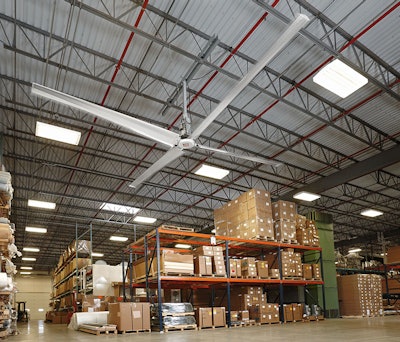
4) Let HVLS Fans Mix Facility Air
Many facility managers know high-volume, low-speeds fans are ideal for their ability to control temperatures, but there’s another benefit HVLS fans provide that many facility managers didn’t expect before installation – their ability to enhance indoor air quality.
The same reason HVLS fans are great for balancing temperatures from ceiling to floor are related to why they’re great at noticeably improving air quality. In a process called destratification, HVLS fans gently circulate the air from the ceiling downward to the ground. Once it reaches the ground, it recirculates upward, only to be pushed back down.
This action not only creates more even temperatures across from top to bottom, the mixing of air ensures that particulates don’t build up in concentrated areas. Employees and visitors in facilities that use HVLS fans will not only experience a cooling effect of 5 to 6 degrees F on hot days, they’ll also be breathing in fresher, cleaner air.
Unlike traditional high-speed fans, HVLS fans circulate larger volumes of air greater distances with their unique blade design. By generating air speeds of just 2 to 3 mph, a 24-foot HVLS fan can cover more than 22,000 square feet of floor space, which equates to approximately 20 floor fans.
The implementation of HVLS fans in a curtain wall-divided area will optimize the workspace for efficient and effective air movement and quality.
A Smart Investment
These four tips for improving air quality through facility layout can reinvent workspaces. Controlling and minimizing the dangerous buildup of fumes and vapors boosting employee health and material quality. Working in tandem, exhaust systems, curtain walls and HVLS fans are wise investments for any facility manager looking to improve indoor air quality and in plant safety, overall.