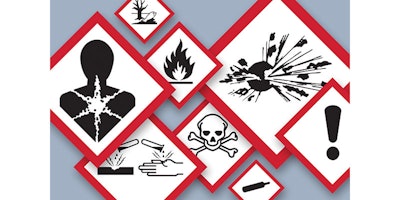
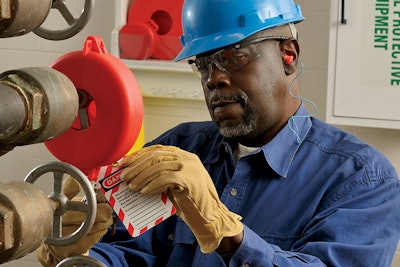
Most environmental health and safety (EHS) professionals are aware that the Occupational Safety and Health Administration (OSHA) releases its annual Top 10 list of frequently cited violations at the National Safety Council Congress and Expo every fall. However, since OSHA’s Top 10 is a compilation of the most cited violations for all industries — including agriculture, construction, maritime and general industry — most food and beverage manufacturers find portions of the list aren’t relevant to them.
To help better understand which violations are most common for this sector, it’s important to look at the most-cited standards in the food and beverage manufacturing industry specifically.
During fiscal year 2016 (October 2015 – September 2016), OSHA completed more than 600 workplace inspections and issued more than 2,200 citations for industries listed under the North American Industry Classification System (NAICS) Codes 3111–3119 for food manufacturing and NAICS Code 3121 for beverage manufacturing. The 2,200 plus OSHA citations resulted in a total penalty amount of an attention-grabbing $8.3 million based on the second week of January 2017 totals.
By reviewing this list, EHS professionals may be better equipped to critique their own facilities for potential deficiencies within these focus areas.
The most frequently cited safety violations in the food and beverage industries for FY 2016 were:
1. CFR 1910.147 Total Violations: 328 Total Penalty Amount $1,759,662
The Control of Hazardous Energy (lockout/tagout) standard covers the servicing and maintenance of machines and equipment in which the unexpected energization or start-up of the machines or equipment, or release of stored energy, could harm employees. This standard establishes minimum performance requirements for the control of such hazardous energy.
Compliance Hot Topics
- General procedures; energy control program; periodic inspections; and training
2. CFR 1910.212 Total Violations: 198 Total Penalty Amount $980,273
The scope of the General Requirements for All Machines standard is to protect the operator and other employees in the machine area from hazards such as those created by point of operation, ingoing nip points, rotating parts, flying chips and sparks.
Compliance Hot Topics
- Machine guarding to protect employees in the machine area from hazards; point of operation; anchoring fixed machinery; general requirements; and exposure to fan blades less than seven feet above the floor
3. CFR 1910.119 Total Violations: 148 Total Penalty Amount $839,754
The purpose of the Process Safety Management (PSM) of Highly Hazardous Chemicals standard is to prevent or minimize the consequences of catastrophic releases of toxic, reactive, flammable or explosive chemicals.
Compliance Hot Topics
- Written PSM program; process hazard analysis; and training of contractor employees
4. CFR 1910.1200 Total Violations: 144 Total Penalty Amount $191,856
The Hazard Communication standard ensures the hazards of all chemicals produced or imported are evaluated, and that information concerning their hazards is communicated to employers and employees.
Compliance Hot Topics
- Written program; training; and developing and maintaining safety data sheets (SDS)
5. CFR 1910.305 Total Violations: 122 Total Penalty Amount $197,488
The scope of the Wiring Methods, Components and Equipment for General Use standard addresses temporary wiring, flexible cords (extension cords), cables and the grounding of electrical equipment.
Compliance Hot Topics
- Substitute for fixed wiring; openings effectively closed; flexible cords and cable strain relief; covers and canopies; and conductors entering cutout boxes or cabinets protected from abrasion and effectively closed
6. CFR 1910.178 Total Violations: 111 Total Penalty Amount $227,028
The Powered Industrial Trucks standard contains safety requirements relating to design, maintenance, training and use of various powered industrial trucks including fork trucks, platform lift trucks and motorized hand trucks.
Compliance Hot Topics
- Safe operation; evaluation for operators performance at least once every three years; certification; truck repair and maintenance; and training
7. CFR 1910.219 Total Violations: 110 Total Penalty Amount $374,194
The Mechanical Power-Transmission Apparatus standard covers the requirements for guarding the components of power-transmission equipment.
Compliance Hot Topics
- Unguarded projecting shaft end; and sprocket wheel and chains seven feet or less above work surface were not enclosed
8. CFR 1910.23 Total Violations: 90 Total Penalty Amount $371,238
The Guarding Floor and Wall Openings and Holes standard outlines the requirements for guarding these type openings.
Compliance Hot Topics
- Open-sided floors and platforms four feet or more aboveground level not guarded with standard railings and toeboards; and standard railings not consisting of top rail (42 inches high), intermediate rail and posts on floor platform runway or ramp
9. CFR 1910.303 Total Violations: 78 Total Penalty Amount $197,632
The Electrical – General standard outlines the safety requirements for designing electrical systems.
Compliance Hot Topics
- Installation and use; guarding of live parts; working space requirements; service feeders and disconnects legibly marked to indicate its purpose
10. Section 5 (a) (1) General Duty Clause Total Violations: 66 Total Penalty Amount: $350,289
This provision under the Occupational Safety and Health (OSH) Act requires employers to furnish their employees with a workplace free from recognized hazards that could cause death or serious harm. This catch-all standard covers all hazards where there are no established standards.
Compliance Hot Topics
- Ergonomics and musculoskeletal disorders; and combustible dust
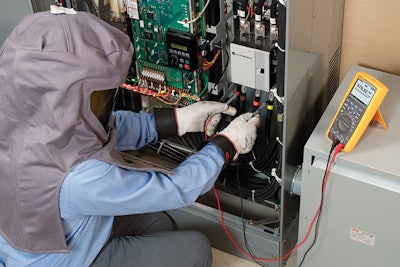
OSHA Penalties Adjusted as of August 2016
On Aug. 2, 2016, the Department of Labor updated the penalties for OSHA and other labor agencies to account for inflation. The maximum penalty increased by 78 percent.
This was the first adjustment since 1990; however, going forward, the agency may adjust its penalties for inflation yearly based on the Consumer Price Index. Below is a listing of the previous and new penalty maximums.
Type of Violation |
Previous Maximum Penalty |
New Maximum Penalty |
Serious |
$7,000 per violation |
$12,471 per violation |
Failure to Abate |
$7,000 per day beyond the abatement date |
$12,471 per day beyond the abatement date |
Willful or Repeated |
$70,000 per violation |
$124,709 per violation |
Are You Ready for an OSHA Inspection?
Being totally compliant with every OSHA regulation is a difficult feat to accomplish. However, identifying major gaps in your safety and health program is a reasonable expectation.
One way to prepare your company for an OSHA inspection is to have a mock OSHA audit completed at your facility. You can conduct the audits using internal resources who are familiar with your equipment, facilities and work processes.
Another school of thought is to utilize a fresh set of eyes to review your establishments. OSHA has an On-site Consultation Program which offers free and confidential safety and health advice to small and medium-sized organizations, with priority given to high-hazard companies. On-site consultation services are separate from enforcement and do not routinely result in penalties or citations. On-site consultants are state or university employees who work with employers to identify workplace hazards and provide advice on compliance with OSHA standards. They can also help develop safety programs to help reduce injuries and illnesses.
There are also fee-based, independent consultants who conduct thorough mock OSHA audits. Their inspections simulate an OSHA inspection with opening conferences and a review of your injury and illness logs. They can then conduct a wall-to-wall inspection or just review certain processes or areas of concern such as training records or written programs. Employee interviews and closing conferences are also included. Detailed final reports are provided for identifying next steps and follow-up.
Conclusion
It is understood that under the OSH Act, employers are responsible for providing a safe and healthful workplace.
The underlying goal of every safety professional is to maintain a safe, compliant workplace. To achieve these goals employers need to be proactive and focus on prevention.
If you recognize any of these violations as problem areas in your workplace, make sure you evaluate products, services and resources that can help you comply with OSHA’s workplace safety standards and reduce the impact of potential costly fines.
About the Author
John M. Eliszewski, MS, CSP, HACCP, QSSP is a Technical Safety Specialist at Grainger, a leader in safety services and solutions, offering technical support and training to help customers comply with workplace safety regulations and safeguard facilities. For more information on creating a safer working environment, visit http://safety.grainger.com.
*Note: Due to OSHA’s final rule on Walking and Working Surfaces standard which became effective January 17, 2017, 29 CFR 1910.28 (b)(3) and (b)(7) now covers guarding of floor holes and openings.