
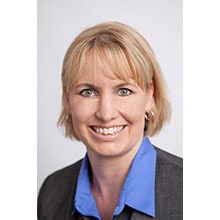
From the initial installation of your inline product inspection metal detector, the validation, ongoing verification and regular monitoring of this critical control point (CCP) can have significant impacts on your business. Here, we explore the difference between some of the terms and how, in some cases, with the latest metal detection technology, the frequency of testing can be reduced to deliver huge untapped production potential.
Validation Procedure
All metal detection equipment must be validated at the time of installation by the manufacturer or their representative. They should show, through the provision of objective evidences, that the requirements for the specific intended use or application have been met. If substantial modifications subsequently occur, a revalidation of the machine should be carried out.
Verification Procedure
Any metal detection system should be periodically verified (typically at 6-to-12 month intervals) in order to demonstrate due diligence. In addition, verification will ensure that it continues to operate in accordance with the specified sensitivity standard and it continues to reject contaminated product on detection of metal. The procedure also ensures all additional warning/signaling devices are effective (e.g. alarm conditions, reject confirmation). The procedure should ensure installed fail-safe systems are functioning correctly and that all current safety standards are being complied with. The verification procedure should ensure that the company/line/product sensitivity standard and metal detection policies are being complied with. It is important that all metal detection equipment must be independently verified as minimum, on an annual basis.
Verification Audits
Such audits ensure that equipment complies with the manufacturer’s recommendations and good practice. Experienced metal detection experts can often spot potential problem areas — and suggest solutions — before such problems become apparent to the user.
Performance verification should be undertaken by the equipment manufacturer or their appointed agent and be able to demonstrate evidence of competency by providing valid and up to date training certificates relating to the equipment concerned (make and model).
Having "Built-in Performance Routines" within the system can aid the discipline and record-generation of testing procedures. The routines can automatically request a test at an agreed pre-set time interval. Failure to test the equipment at the agreed time interval could cause a range of different outcomes. Hard-copy documentation (which proves that testing has been carried out) can be provided through a local printer; alternatively, it can be downloaded to a central PC, using a detector with network connectivity capabilities.
Annual Verification
The annual verification is similar to verification audits, although the former are more in depth. These annual checks must be in line with general HACCP-based requirements, fully documented and should include as a minimum the metal detector manufacturers initial build parameters — not accessible to the user. The annual test should also include electrical and mechanical installation checks, system functionality checks including adherence to the specified critical limits, product related information checks, fail safe functionality checks and customers test piece verification checks.
Finally, verification should also ensure that line personnel are trained and knowledgeable in undertaking the Standard Operating Procedure (SOP) regarding the local verification and monitoring tests. A summary of the verification tests must be completed and an indication of the performance since the last test and any potential degradation in the previous year and the following year should be commented upon. The verification is only completed when the test engineer also verifies how the system is being verified and monitored by auditing a member of the production personnel (at random) with respect to carrying out the regular metal detector tests as detailed in the manufacturing sites SOP for monitoring CCP’s.
System Monitoring (Testing)
In ensuring that the metal detection system continues to detect and reject in accordance with the documented standard, the purpose of the test is to ensure that there has been no significant change in the detector’s performance level since the last successful test. These changes could occur as a result of alterations to machine settings, product signal and metal detector functionality.
The selection of correct metal contaminant types for testing is important; the significance of a change in machine settings, product signal or metal detection functionality can vary depending upon the type of metal contamination. For example, it is feasible that the phase of the product may change to the extent that stainless steel operating sensitivity is maintained, whilst ferrous sensitivity is lost. If, however, testing is only conducted with stainless steel, there will be no indication of loss of operating sensitivity to ferrous contamination.
Guidance is sometimes given on non-ferrous and stainless steel ball sizes that can be detected, based upon actual ferrous ball size detected. The actual sizes are very much application specific. In reality, the relationship between one contamination type and another is complex and based on a combination of test ball size, material, detector operating frequency and if the product is wet or dry in nature.
Best practice would be to perform monitoring tests on all three metal types (ferrous, non-ferrous and stainless steel) that could form potential sources of contamination.
Predictive Analytics
There is a more robust and valid approach to determining that the metal detection system is continuing to detect and reject in accordance with the sensitivity standard. This approach is to undertake continuous monitoring or checks for changes in the key operating parameters of the metal detector system. If the key operating parameters can be continually monitored for stability using condition monitoring, there is scope for potentially reducing the frequency of testing beyond the existing time period. This would bring an attractive benefit of increasing the user’s Original Equipment Effectiveness (OEE).
Some commercially available metal detectors do offer a continuous monitoring feature such as Predictive Analytics. However, when considering its use, ensuring the system will automatically alert users when there has been an unexpected change in the monitored parameter is important. This should prompt a verification test and a "stop" alarm if there is an unacceptable change. If the system remains within specification until the auto-alert is activated, then the end user can reduce the test frequency, saving labor as well as recovering lost potential production, as the line is not being stopped to assess if the detector is in specification.