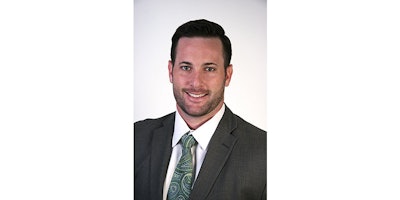
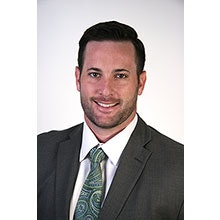
Nearly five of every 100 employees in the food manufacturing industry experience injury or illness due to a work-related accident, according to the Bureau of Labor Statistics. While no level of preparedness can eliminate 100 percent of workplace accidents, employers can greatly reduce the risk by creating a detailed accident preparedness plan. And that plan should be supplemented with frequent employee education on safety regulations so everyone is prepared if an incident occurs.
Here are four things to consider when creating your accident preparedness plan:
Immediate Actions
The actions taken in the moments following a safety incident can be the difference between life and death for an injured employee. Because employee well-being is the top concern, it’s crucial to get an injured employee to safety as quickly as possible without putting anyone else in danger. Quickly assess what care is needed and if someone needs to call 911. It’s also important to conduct an investigation at the time of the injury, assessing the scene and interviewing those who witnessed the accident, while the memory is still fresh in their minds. Details like this can be captured in your accident response plan. But don’t stop there — train your employees on these procedures regularly to ensure everyone understands their roles in the event of an accident.
Post-Accident Paperwork
Imagine you have a supervisor with 35 years of experience at your company. One day she is walking through the plant, not paying attention, and trips over a water hose as it’s being transported through the facility. The next thing you know, your supervisor is at the hospital with a broken kneecap. Now you are down one supervisor on the job, and you have a workers’ compensation claim to handle. After she is safe and your internal investigation is complete, what is the next thing you should do?
Paperwork.
To start, you should complete an incident report detailing the events of the accident. Any claims should be reported to your workers’ compensation insurance carrier within 24 hours of the incident. Additionally, OSHA’s recordkeeping regulation requires that employers fill out and maintain records of work-related injuries and illnesses using the OSHA 300 form.
By keeping all necessary forms and contact information in a centralized location, you can spend less time hunting down documents and more time handling other tasks. Consider including the forms in the appendix of your accident response plan or include notes on where such documents may be found. Also note in the plan exactly what should be recorded. Then train employees on how to provide detailed and accurate information in each report.
Return-to-Work Program
Three of every five accidents in the food manufacturing industry result in an employee’s absence from work, according to the Bureau of Labor Statistics. With these absences come the indirect costs of employee replacement and training. To keep these costs low and productivity high, consider establishing a return-to-work (RTW) program as part of your accident preparedness plan.
According to a study by RTW Knowledge, employees will return to work earlier if their supervisor understands their pain, shows concern and works with them to adjust the workplace to accommodate their injury. Train your supervisors on injury management and your return-to-work program. Communication and empathy skills are key. Let them know the resources and options available to them — like the ability to temporarily move an injured employee to part-time or light-duty work if it allows the employee to return early.
Because not all employees will return to work after a major injury, it’s also important to keep a list of job responsibilities and potential job candidates on hand. Consider promoting from within and cross-training so employees can easily transition from one job to another.
Preventative Measures
In addition to addressing workplace accidents and injuries, your accident preparedness plan should include information on how to prevent such events from occurring. Evaluate the cause of previous accidents and establish corrective measures to prevent similar incidents from happening again. This information should be properly recorded and shared with employees. Re-train all employees regularly — especially once a new modification has been made.
Further, by encouraging an open environment within the workplace, supervisors can urge employees to submit their ideas for improvements and additional safety protocols. Consider a behavior-based safety program that rewards employees for practicing company policy. On average, the recorded workplace injury rate decreases by 29 percent in one year after implementing a behavior-based safety program — and 72 percent after five years, according to the American Psychological Association.
Creating an accident preparedness plan can help you save lives on the job. Plus, the safer your business looks to insurance carriers, the fewer workers’ compensation claims you are likely to have — and therefore the lower the premium carriers will give you.
About the author
Parker Rains, based in Nashville, Tenn., is vice president of middle market business insurance firm, Fisher Brown Bottrell Insurance, which is a wholly owned subsidiary of Trustmark National Bank, a publicly traded financial services company with over 200 locations and over 3000 associates in Mississippi, Florida, Tennessee, Alabama and Texas. You can reach Parker at [email protected], and visit Fisher Brown Bottrell Insurance online at www.fbbins.com.