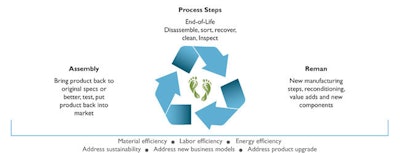
Lately, there has been a lot of buzz about the new and emerging technologies in manufacturing that are likely to produce major industry changes in the coming months and years. One such area of technology, as identified by the Advanced Manufacturing Partnership (AMP) group, is remanufacturing.
But what exactly does that mean?
Over the years, the industry has come to realize that one-way, non-circular processes that take products from manufacturers to landfills are no longer sustainable. This is because the negative environmental and economic impacts of simply discarding manufactured products that reach their “end of life” have become too great to ignore.
Manufacturers are seeing the need, as well as the potential business value, from turning the outdated process into a cyclical process where products get reused, rather than dumped into already-overflowing landfills. The advancement of technology over the years has allowed for remanufacturing to salvage and reuse old parts without compromising the quality of the remanufactured product. “Reman” systems are applying innovative thinking so that new processes, stringent quality checks and re-engineered supply chains can return worn, discarded, end-of-life products to a “like-new” state with comparable performance and warranty (see figure below).
Good examples of sectors that have recognized remanufacturing as a profitable model are the automotive, construction/mining and the aerospace industries. Over the past 70 years, auto manufacturers have been taking apart an increasing number of old vehicles and sending their parts to various remanufacturing centers to be recovered and reused. The auto industry was also among the first in the U.S. to form its own Automotive Parts Remanufacturing Association (APRA) and the Motor & Equipment Remanufacturers Association (MERA), encouraging other industries including electrical, electronics and medical equipment to follow their lead.
Benefits of Remanufacturing
Today, although the automotive, mining and aerospace industries still account for more than 50 percent of remanufacturing, companies in almost every major business sector are implementing the process. And the Remanufacturing industry is only expected to grow.
According to recent estimates by Nabil Nasr, director of the Golisano Institute for Sustainability and the founder of the Center for Remanufacturing and Resource Recovery at the Rochester Institute of Technology, the U.S. remanufacturing industry boasts over 500,000 employees and generates more than $100 billion worth of sales year round.
In addition to the already mentioned benefits, remanufacturing business model also offers the following important advantages to both manufacturers and consumers alike:
- Remanufacturing allows to embrace greater range of selling options like leasing, renting, exchange of core deposit, part or system remanufacturing and direct sales;
- Allows for variable cost structure as the burden of extending the product life rests with the supplier as the product is not always owned by the end user;
- A closed loop remanufacturing models allows for better control of the installed base and improved service revenue;
- It results in products that are cheaper but with comparable warranty;
- Reduces the demand for raw materials caused by increased consumption;
- Ensures the product is upgraded before it is brought back to the market, increasing its commercial value;
- The disassembly of products required before Reman provides OEMs insights into how to redesign the manufacturing process to bring down warranty costs;
- Minimizes damage to the environment -- prevents many products and the hazardous materials they contain from ending up in landfills and waterways;
- Reman offers the best solution to address the “extended producer responsibility” and the new regulations and legislations coming into force for sustainability around the globe.
The Complexities of Remanufacturing
Most manufacturers never used to include reverse logistics as a major operation or necessity because they did not need control over the end-of-life state of the product. Most often they would assign the task of product returns to either the customer or to their channel partners. However, reverse logistics is becoming critical with the rise in Reman industry. This means that manufacturers now must be able to identify, procure and ship used, worn or discarded products from locations that cannot be identified in advance. Adding to the uncertainty is the fact that each part can take a different route back to the plant.
For Reman to be successful, the manufacturer must be able to accurately forecast demand and match the data with the flow of returns. However, even after predicting returns versus demand, there are no guarantees on the extent to which individual disassembled components may be usable, and, depending on the wear and tear, the yield can be very different.
These complexities around production planning, scheduling and control require customized MRP systems and solutions, especially on the manufacturing plant floor.
Some of the key factors needed to ensure the future success of reman, include:
- Clear demand for the product and high intrinsic value;
- Product with moderate technology evolution;
- Robust reverse logistics in place with integrated sales and service options;
- Product design suitable for reman -- quick, cheap, with safe disassembly;
- Existing technology available to restore the product;
- Ready availability of design information;
- Reman product should be stable over its lifecycle.
Conclusion
During the past decade, this industrial process that restores worn or end-of-life products to a like-new condition has become an integral part of the global economy. Although remanufacturing is still facing challenges in product design, marketing, production, materials management and reverse logistics, its business benefits far outweigh the risks, creating an industry that is poised for major growth.
Further from a business perspective the major benefits of remanufacturing besides being profitable and counter cyclical, the model offers greater resilience to market fluctuations because of the combined product and service oriented business model due to its inherent closed loop structure.
Finally, Reman allows businesses to not only salvage used products to perform like new, but also increase the savings in terms of natural resources, energy, material and engineering resources while extending service lifecycles of their products. And as every manufacturing operation tries to find ways to achieve zero waste in the near future, remanufacturing will surely be one of their answers.
Rajesh Krishnan is a director in Wipro’s Manufacturing & Hi-Tech strategic business unit. Rajesh has over 25 years of product design, manufacturing process and systems experience. His work includes developing and delivering technology enabled business transformation solutions for the North American markets to Fortune 1000 clients. In addition to sustainable manufacturing, Rajesh also focuses on the development of lean systems and is a patent holder for many of his product designs. He holds a Masters’ degree from Advanced Manufacturing Technology Center, Auburn University and a Bachelors’ degree from Bangalore University in mechanical engineering.