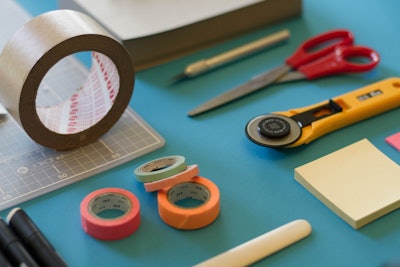
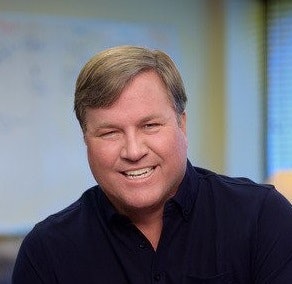
As manufacturers in the United States enjoy substantial job growth, the resulting need for additional skilled workers has left the industry struggling to keep up. Innovative technologies, strong economic development and retiring baby boomers are driving a widening shortage of qualified job applicants in the space, especially for positions that require more technical skills. A recent report from Deloitte revealed this gap is expected to grow from about 488,000 jobs left open today to as many as 2.4 million in the next decade, with a potential economic impact of $2.5 trillion. To address this shortage, manufacturing employers must begin integrating training opportunities and the latest technology into their onboarding process to expand skill sets for placement of qualified labor now and into the future.
Artificial intelligence, robotics and the Internet of Things now play a critical role in manufacturing production. While many felt this epidemic change would eliminate jobs throughout the industry, in reality it has spurred some of the most substantial growth in decades β the U.S. had as many people working in the manufacturing sector in December 2018 as it did 69 years ago.
As technology and customer demand evolve, the prevalent skills gap and employee shortage issues plaguing the industry will continue to compound if manufacturers donβt establish and train stronger talent pools to fill these skilled positions. Implementing predictive analytics technology that looks for inefficiencies and workforce gaps and identifies employee candidates likely to excel can eliminate the guesswork in finding the most qualified individual for the job. Harnessing the abundance of data coming in from various sources (machinery, employees or parts,) and turning it into real-time measurement effectively monitors and identifies supply chain inconsistencies and allows for proactive hiring measures. This notion, coupled with the capability of the gig economy, can save industry manufacturers and suppliers valuable energy and resources and ultimately increase profitability.
For context, the gig economy is a term used to classify a growing sector of the workforce who operate as freelancers or independent contractors for short-term, flexible engagements. In todayβs increasingly competitive workforce landscape, the gig economy provides manufacturers with a scalable solution to combat the workforce shortage problem and grow their businesses.
This new workforce can be streamlined through the following avenues:
1. Unlock the value of predictive analytics to advance recruitment and productivity
Employee quality and retention are extensively impacted by predictive analytics. The technology can lessen areas of vagueness in a candidateβs background and assist in recognizing personal and professional attributes that would contribute positively to the companyβs mission and profitability. In short, predictive analytics uses historical data to forecast future outcomes.
Looking post-hire, and reviewing key performance metrics can determine the number of freelance workers needed to meet production goals while continuously monitoring productivity and quality performance.
2. Engage the millennial workforce
While the baby boomer generation has dominated the manufacturing workforce for many years, 10,000 members of this generation reach retirement age each day, and this is expected to continue into the 2030s. Millennials are now the largest generation in the U.S. labor force, and they have started a movement that has shifted how the workforce operates. Almost half of working millennials are freelancers, a rate higher than any other generation, proving manufactures must be more strategic in how they manage their millennial workforce in order to thrive.
The manufacturing industry can leverage the gig economy to locate employees with the right skill set using a variety of omnichannel recruiting strategies. Gone are the days when an employer could share an open position to a job board online and wait for qualified applicants to come to them. Instead, recruiters must closely examine their key markets and deploy strategies such as geo-targeted paid and organic social media campaigns, out-of-home advertising, employee referral bonus programs and collaboration with state and local employment centers to engage potential candidates. They must also continuously analyze labor and wage data regionally to maintain competitiveness.
3. Emphasize continued education using mobile engagement
Employees with the analytical, technological and problem-solving skills required for high-demand jobs are an asset to manufactures, and the value of these employees can by equipping them with continued training resources. Manufacturers should consider mobile learning management apps that aggregate all training data and logistics, a two-way employer/employee digital dialogue and provides employees with the continued education and worksite information they need to be successful. Gig workers use mobile, and this type of app will ensure these employees arrive on the job with a comprehension of their tasks and job safety knowledge. Providing employees with continued learning opportunities not only helps promote their growth it also creates a more prosperous workforce at the employerβs disposal.
Mobile technology can also provide employers with real-time analytics such as tenure, attendance, and performance reviews in optimizing operations from placement to production and beyond.
The gig economy is altering the way people view and perform work, and manufacturers and top-tier suppliers must be ready to respond with innovative policies and programs. By capitalizing on the principles of the gig economy, paired with innovative predictive analytics and engaging mobile platforms, manufacturing businesses can minimize their strain on existing employee resources and maximize productivity and earnings.
Pete Butler is chief executive officer and founder of MS Companies, a data-driven technology company.