
Manufacturing is undergoing a makeover.
Amidst growing pressures from competitors mixed with constantly evolving technologies like IoT and smart factories, the manufacturing industry is changing more than ever before. A recent survey shows 94.6 percent of manufacturers think positively of their company, and believe they are headed for growth on all fronts.
While the manufacturing industry seems to be headed for success, companies must conquer the issue of a labor to make this growth a reality. A number of factors, from the introduction of automation to policy changes and economic growth, have led to an increase in workforce demand, highlighting the need for a skilled labor in the industry. Up to 72.9 percent of manufacturing companies surveyed listed recruitment and retention of a workforce as their number one business challenge, and over 30 percent of respondents note that a shrinking labor pool correlates to lost business opportunities.
The same survey produced the following results on how these companies are handling this challenge: 66.6 percent of respondents want to work the existing workforce more, 65.4 percent of respondents believe the solution lies in creating and/or expanding training programs internally, 56.5 percent of respondents want to partner with educational institutions to create certification programs, and 55.4 percent think the industry should utilize temporary staffing services.
Not only is there little agreement on the best solution for this issue, only one of the above options will help long-term in building a strong workforce. As with any problem, the key to the right solution is identifying the underlying cause of the initial issue.
In this instance, a multitude of factors can be held responsible, including:
- Lack of STEM education: While schools used to place a higher importance on science, technology, engineering and math education, the focus is increasingly shifting toward the humanities, and therefore schools are producing fewer graduates in STEM fields.
- Lack of training programs: Vocational schools are considered an outdated educational trend. Once incredibly popular, skill-based learning centers, apprenticeships, and on-the-job training programs are no longer as widespread as in previous years.
- The increasing age of the workforce: The individuals that made up the traditional manufacturing workforce, those that built the manufacturing industry post-WWII, are retiring in increasing numbers.
- Manufacturingβs image problem: The manufacturing industry has a reputation of being dismal, boring and outdated. Todayβs millennial workers seek employment opportunities that excite them, and until manufacturing can change its image, it will remain unattractive to the new workforce.
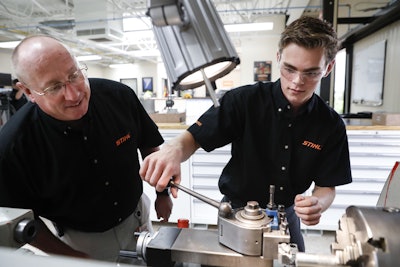
After identifying the problem points, it is much easier to decide on a solution. Of the above issues, manufacturers can do nothing about the aging population, but can easily solve the other factors through the adoption of technology, which will help stretch resources, allow workers mobility options, and ease communication.
Employing Technology
There is no easier way to attract the millennial workforce than by adopting and utilizing technology. Millennials grew up as digital natives; not only are they adept at using technology, but they find comfort in it, and are attracted to companies that utilize it fully. Implementing technology is the key to increasing interest in the manufacturing industry. Technology is evolving every day, with new tools coming to market that help with a growing number of industry processes. A few examples:
- Creating Greater Labor Efficiencies β Applying data analytics to labor use allows for highly accurate demand-based scheduling. This means labor is used only when it is required, decreasing the need for overtime, lowering cost, and creating an environment where workers are engaged and satisfied. With technology that predicts production or distribution demand, manufacturers can accurately forecast labor needs and staff accordingly, without overworking their employee population. This enables manufacturers to produce the same results, at a lower cost, with a happier workforce.
- Allowing Mobility β Technology, particularly cloud-solutions, allows for real-time data to be updated, reported, and stored from anywhere. This gives workers the freedom to complete work-related tasks on their own schedule, from their chosen work space. Moreover, these technologies allow for remote employees to work virtually alongside their colleagues, expanding the hiring pool tenfold, as location is no longer must be a deciding factor in the hiring process.
- Facilitating Communication β As with any job, communication between employees and employers can make or break workforce satisfaction. Technology-enabled communication can take place at a faster pace and from any location than ever before. Employers must ensure the ability to book off a shift, adjust schedules, and communicate leave with ease. Automating backfill processes, which consider certifications, compliance, skills and overtime, eliminates the need to hire additional workers and increases employee satisfaction by 12 percent,
Modern living β and working β is impossible without technology. By integrating new technologies into the manufacturing industry, not only will employers attract the new, young workforce, but also increase productivity and expand opportunities for business beyond what was previously thought possible. Technological adoption is simply a win-win.
Robert Means is the Vice President of Workforce Management Suite at Infor.