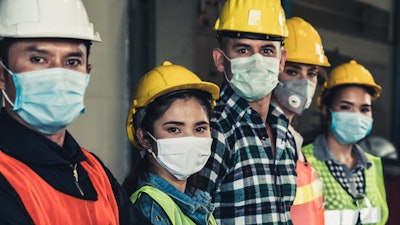
Labor shortages have disrupted almost every industry since the pandemic began, and with the Great Resignation ongoing, staffing needs persist. The skilled labor shortage has been particularly hard on the manufacturing industry.
According to the Wall Street Journal, around 70,000 to 90,000 workers or more will need to be added by 2025 to meet the workforce needs for fabrication expansion in the U.S. alone. The need to fill vacancies, cover shifts and maintain operational efficiency are high priorities for manufacturers, which may mean the safety of their current staff gets lost in the shuffle.
Current employees are working harder and longer to fill the gaps left by COVID and the Great Resignation. At the same time, many companies are also hiring less experienced candidates amidst the struggle for talent. These new hires increase safety risks since they don’t have the benefits of operational experience and onsite knowledge in the event of a safety incident.
To communicate effectively, fill open shifts and keep employees safe, manufacturers should leverage technology to check in on their team’s wellbeing. Especially amidst staffing shortages and the ongoing pandemic, here are three best practices manufacturers can implement to better protect and communicate with employees.
Communicate updates quickly and frequently
During the labor shortage that manufacturers are currently experiencing, there are fewer employees available to respond to incidents in real time. Technology can address this challenge with solutions like mass notification systems that send pre-crafted messages to relevant employees based on incident type.
For instance, if a certain piece of equipment is out of service, a mass notification system could provide updates to impacted employees who need to use it via SMS, email, voice, desktop notifications or other channels.
This ensures every employee is up-to-date even if they have different work schedules and communication preferences.
With a solution in place before an event occurs, manufacturers can quickly communicate to affected employees. For example, employees at a given site can be sent targeted notifications for their facility, but be filtered out of communications only relevant to other locations.
This helps get employees the information they need to stay safe and efficient. If a safety protocol needs to be initiated, a mass notification system can keep employees informed on what is going on and what is expected of them so they know what steps to take to minimize the risk.
These tools don’t have to be only for urgent communications. They can also be leveraged to help employees feel connected and informed on workplace updates. As the pandemic has made it difficult to maintain networks, communication is key to keeping everyone up-to-date on policy changes, safety protocols and COVID-19 requirements such as vaccines or testing.
Implement daily health checks
As manufacturing employees work overtime, burnout and exhaustion can lead to the high turnover rates many industries are seeing. In physically demanding roles, it’s important for employers to prioritize their teams’ wellbeing.
In fact, a lack of respect towards floor and production workforce members was cited as one of the main reasons manufacturing employees left their jobs. Manufacturers can lower turnover and its associated costs by checking in on how their teams feel each day and following up when needed.
To this end, a daily health questionnaire can be sent directly to employees’ phones as a reminder that their employer cares about their wellbeing. These are also critical tools in fighting the spread of COVID-19 by screening if employees are sick before they come to work their shift.
With this data, manufacturers can see when symptoms were reported and by whom if they need to do contact tracing. In the end, it is easier to deal with the absence of one employee than it is to have them come in and infect the entire team.
Daily health checks can be automated to easily check-in on employees’ mental and physical health. With the right tool, these checks don’t require added time from managers and they can get the information they need about their team to address any concerns as they arise.
Use polls to fill shifts
Once manufacturers have visibility into healthy staff who can come into work, they can use polling features in mass notification solutions to share available shifts and coordinate coverage.
Employees will get a message on their preferred method of communication letting them know a shift has opened with the option to respond if they are able to come in.
Finding coverage during the manufacturing labor shortage is challenging and teams need the right tools to streamline the process as much as possible. In the past, managers may have reached out directly to each employee to ask if they can come in, a time-consuming and inefficient process.
Automating that process allows manufacturers to reach the right people faster and ensure employees receive the information on time.
When there are gaps in critical roles, employees are stretched thin and may be responsible for too much at once which can lead to avoidable mistakes. Streamlining the shift coverage process is critical, because ensuring a fully staffed team means improved safety.
Maintain productivity without compromising employee safety.
While the ongoing labor shortage continues to pose challenges for manufacturers, with these best practices in place, manufacturers can work to protect the health and safety of their employees while managing staffing needs.
---
Terri Mock is the Chief Strategy and Marketing Officer at Rave Mobile Safety.