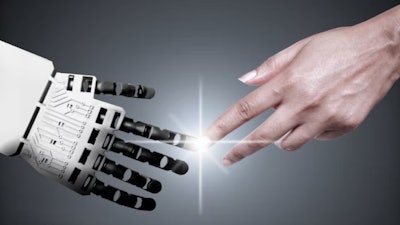
Despite the promise of the Autonomous Factory, most everyone knows that a factory without people will not be possible in the foreseeable future. Nevertheless, calls for an expansion of robotics, advanced automation and interconnectivity through the Internet of Things (IoT) are rising. Globally rampant job resignations, the general labor shortage, and the pandemic's aftermath fuel this demand. While automation can offer relief for understaffed workplaces, it is all about finding the right balance.
Above all, businesses must focus on decisively improving human-machine collaboration.
There are many arguments in favor of robotics, automation, and artificial intelligence over humans. Machines make significantly fewer mistakes and can be substantially faster at some tasks, and, of course, machines don't need breaks. However, even this superficial take illustrates where the issue in this debate resides: Humans and machines are juxtaposed as competitors, if not more so, as adversaries. This is a cardinal error because it positions robots and artificial intelligence as a replacement or alternative for the human workforce. However, both should come as a compliment.
Robotics Are No Piece of Cake
The right technology can usher in a new stage in digital transformation, but automation is no piece of cake. Take warehousing and logistics, for example. An analysis by Research and Markets concludes that the costs for commissioning 50 to 100 robots lands somewhere between $2 and $4 million dollars[1]. An investment of that magnitude roughly equals the average annual earnings of 95 warehouse workers in the United States [2].
There are other challenges. Automation, robotics, and artificial intelligence are incredibly complex systems that are extremely costly and require long project runtimes. They often mandate process redesigns and reconfigurations. Thus, a considerable amount of your business flexibility may evaporate. Finally, it must be emphasized that technical systems are not immune to errors.
Autonomous vehicles, for example, do not always recognize every obstacle or the route they have to take. This can lead to serious accidents, especially in warehouses. For these reasons, many businesses are slow to invest in automation systems.
Human Advantage
The introduction of new technology within a workplace often exposes resistance to change. Many employees react skeptically, do not go along with the project, and in the worst cases, boycott it, thus causing it to fail. The fear factor plays an important role, as does the need for training. A recent study of international warehouse workers by Accenture revealed several recurring concerns: workers were worried about losing their jobs, having inadequate training resources, and dealing with downtime or errors caused by technology malfunctions[3].
It’s critical to listen and act upon workers’ concerns when implementing new systems. Humans remain a crucial success factor in the warehouse and bring cognitive decision-making and reasoning that is crucial in dealing with variants, fluctuations and short product life cycles
Traditionally, picking, storing and retrieving parts and packages in a warehouse and logistics environment were tasks performed entirely by humans. However, these activities are strenuous. You have to lift loads all day, pull a cart and, above all, walk a lot. The travel time in order picking is estimated between 40 and 60 percent of the total picking time and is the most time-consuming step of the entire picking process [5].
In the mid-1990s, cobots, or collaborative robots, were invented to interact with humans in a work environment to free workers from having to perform more repetitive, complex, or hazardous tasks. In warehouse environments, cobots save travel time, carry heavy loads and help with storage and retrieval.
Cobots are usually implemented to provide support, particularly in common picking scenarios such as single- and multi-order picking, batch picking, pick & pass, or pick & pack. In addition, the associated investment volume usually remains at a fraction of what organizations have to spend for a conventional industrial robot. Many manufacturers set the entry price at approximately $5,000, but realistically businesses should expect $15,000 [6]. Some preconfigured cobots can be implemented in a few days, while others typically take about three months.
However, even cobots have their limits. Bulky goods and alternating formats can affect performance. Furthermore, interface problems remain. After all, cobots are not fully autonomous systems. They are designed to work with humans - humans who have to document and confirm activities and process steps. A job usually done exclusively by barcode scanners. Of course, cobot manufacturers install scanners in their devices, but this limits the flexibility and agility of the employees.
Wearables - Smooth Operators
That's why looking into other solutions, such as wearable barcode scanners, makes sense. They bring the advantage of keeping the worker's hands-free at all times, saving up to six seconds per scan, depending on the environment.
If a barcode scanner with an integrated display is in use, supplementary work instructions can be issued via the display, such as the next assignment. Above all, it is essential that the wearable does not become a shackle. In practice, glove or back-of-hand scanners have proven to be particularly advantageous.
However, it is also important that the scanners have sufficient battery life. They should manage at least one shift without recharging. This requires around 3,000 scans. Furthermore, the scanners should be easy to operate, ideally supplemented by flexible access and connectivity solutions. These are particularly important for providing the necessary flexibility and additional leeway.
Wearable barcode scanners can carry another important advantage if they are equipped with sensors that can read, process and refine additional meta-data. Such data includes the place of use, the number of steps, and the total number of scans and their duration. With the help of suitable analysis software, it is possible to obtain an accurate picture of the shop floor, an as-is-view, if you will.
This view complements the top-down or as-expected perspective of a WMS or ERP system, and will let organizations identify hotspots or blockers. In addition, so-called time-motion studies can obtain valuable insights into the lead times of orders, and whether sufficient personnel are on-site at the respective workstations.
The debate about automation must be put on a rational basis. Technology is not a means to replace human workers, but to provide them with relieve. This message needs to be firmly anchored, especially given the current labor shortages and disruptions in global supply chains. The idea of augmenting workers with wearable barcode scanners and cobots can provide efficiency leaps, but above all, it leads to immediate results and creates profitable incentives for organizations. Not to forget, it also comes in handy in recruiting scarce human labor.
Axel Schmidt is the senior communications for ProGlove.
[1] https://www.globenewswire.com/news-release/2021/09/07/2292728/28124/en/Global-Industrial-Robots-Warehousing-and-Storage-Robots-Markets-Analysis-Forecasts-2015-2020-2020-2025F-2030F.html
[2] According to the job portal Indeed, a warehouse worker in the U.S. earns about $42,000 per year: https://www.indeed.com/career/warehouse-worker/salaries
[3] https://hbr.org/2022/02/research-how-do-warehouse-workers-feel-about-automation
[4] https://ec.europa.eu/research-and-innovation/en/horizon-magazine/concerns-linger-over-workplace-robots-even-they-deliver-benefits