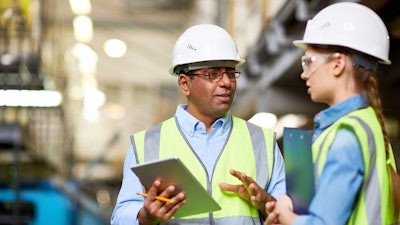
The rising unemployment rate is often a key topic in the political discourse in Washington. In April 2020, it reached a modern day record of 14.80 percent. But for manufacturers in America, and many parts of the developed world, the crisis is in reverse – acute labor shortages.
The generational "skills gap" in manufacturing is shaping up to be a major headache – as more Baby Boomers and Gen-X workers approach retirement age, there are not enough young workers waiting in the job market to replace them. The sector could face up to 2.4 million unfilled positions by 2028, according to a Deloitte study. A preference for white-collar jobs, misconceptions about career and wage prospects in manufacturing, and a lack of adequate skill training centers are amongst the reasons for this crisis.
While there are no easy solutions, manufacturers are not sitting idly by – many are trying out a mix of stop-gap solutions and long-term alternatives.
Retraining and Re-skilling Existing Workers
While it cannot solve a problem of this magnitude, relying on your existing workers can work in the short term. Existing workers can be improved either through in-house skills training/retraining or through sponsorship of courses at external educational institutions. There are several advantages to this approach. It fosters a feeling of loyalty that will help improve employee retention, and it is also less risky, as you are dealing with familiar, experienced professionals instead of fresh unfamiliar newcomers.
Delaying Retirement
Age is just a number – in professional sports, many athletes have played far beyond the average retirement age. This is also possible in manufacturing to an extent, provided the company is willing to make some important safety adjustments. German manufacturers like Porsche are already investing in equipment and workplace changes to make work more comfortable and safer for older employees. Swivel chairs with telescoping features allow workers to do tasks without standing for hours.
Tools connected to armrests, redesigned slip-resistant floors, exoskeletons for heavy lifting, specially-designed robots that work in tandem with humans ("cobots" or collaborative robots) – German manufacturers are leading the way in this arena.
Internships and Apprenticeships
The newer generations simply don’t have any kind of exposure to the manufacturing sector. Many job seekers are intimidated about applying for manufacturing positions because of a total lack of relevant experience and knowledge. Companies who link up with educational institutions, especially technical institutes and trade schools, can tap into a promising pool of talent. More advanced apprenticeships can also create a mutually beneficial arrangement – the apprentice candidates get valuable training that improves their career prospects, while the manufacturer can assess unknown candidates before offering a full-time employment contract.
It is also high time that manufacturers tapped into new sources of talent outside colleges and universities. They should take a leaf out of the U.S. military recruitment strategy and offer a second chance to ex-convicts. Boeing is a great example of a big manufacturer that already offers employment opportunities to ex-felons.
Another approach is to switch to skill-focus when hiring. Instead of looking at educational qualifications and certificates, manufacturers could start looking for individuals who have vocational skills. If they align with any vacant job on the factory floor, they could be hired and deployed with minimal training.
Army veterans and individuals laid off by other industries are also excellent sources of new employees. Sectors like retail and hospitality are struggling as a result of the ongoing pandemic. Millions of new job-seekers have entered the market from these industries. Manufacturers should consider offering jobs to promising individuals, even if they have no experience in factory work.
Leverage Software and Data Analytics
Many facilities suffer from the inefficient deployment of workers, with delays in work order processing, long idle times, frequent equipment breakdowns, spares shortages, and a general lack of critical data-based planning. Upgrading a factory using modern tech like IoT sensors, computer maintenance management software (CMMS) and AI data analysis could remove a lot of these issues. A CMMS in particular is a very cost-effective option that can streamline maintenance processes and help managers accomplish more with a smaller workforce.
Improve Remuneration and Perks
These days, tech companies lead the way in offering generous pay packages and innovative perks. Manufacturers should follow suit and get creative in the way they offer perks, bonuses, and other benefits to new hires.
For instance, many young workers struggle with student debt – companies that offer some help in dealing with such loans could attract a lot of attention from new-gen job seekers. Tax benefits, special sign-on cash benefits, and beefed-up healthcare/medical plans are all options.
Granted, none of them are cheap or economical – but management will have to make some compromises in this regard to have any chance of effectively addressing the labor shortage. Without decent wages, employee retention will always be an uphill battle.
The labor shortage in factories is not a crisis that was created overnight. Consequently, there are no “silver bullet” solutions to the problem. Manufacturing will have to use a holistic approach, with a mix of short-term bandages and more systemic, long-term changes to address the issue.
Bryan Christiansen is the founder and CEO of Limble CMMS.