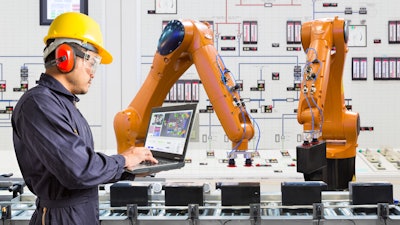
The generational shift moves into high gear in the 2020s. Baby boomers may not all be lounging on beaches, but their numbers in the workforce are dwindling significantly. Meanwhile, millennials (those born between 1981-96) are poised to make up 50 percent of those working by 2022. And Generation Z (born after 1996) has entered the labor pool and will comprise 20 percent of it by 2025, according to statistics published by the Pew Research Center and Inc.com.
With more and more boomers retiring, they’re taking with them long-held beliefs, workstyles, and, in many cases, vast quantities of tribal knowledge. Tribal knowledge is valuable to companies and is not easily transferable. It is often exclusive technical, product, or process information that is stored inside someone’s head. It is rarely recorded in a structured way on web documents or paper.
It’s in a company’s best interest to capture as much of this intelligence as possible to ease the transition to a newer, younger workforce — even if those workers don’t buy in to the way things were previously done. The influx of millennials and Generation Z and outflow of boomers is taking place at the same time as the Fourth Industrial Revolution. This combination of generational and technology changes is destined to leave a knowledge gap, a skills gap, and perhaps a cultural challenge ahead.
The competitive advantage goes to companies that find ways to pass down this expertise and successfully navigate the generational shift. Here are some practical strategies to help:
- Get over any trepidation about machine learning. By collecting data and applying machine learning or natural language processing to analyze it for patterns and conditions, technology is essentially pulling exclusive information out of someone’s head and making it visible to teams. If you have workers writing daily logs or providing voice recordings that recap activities, getting them to tag key information using their tribal knowledge can help machine learning synthesize the unstructured data and turn it into valuable insights. Yes, this requires planning investments in machine learning and AI technologies and building some sophistication in your maintenance systems. But your competitors may already be doing this or planning to. What’s more, many younger workers will only want to work for companies eager to deploy these advanced systems.
- Provide faster, simpler workplace technology. Adding on to Tip No. 1: Management can learn from younger generations and their affinity for applications and tools that are easy to operate and accessible from anywhere. Products from companies like Apple, Google, Amazon, and Microsoft have shaped their views on technology. Many, for example, prefer touchscreen functionality over knobs and dials. While it may be challenging to build the tools they will adopt, it’s time to start. This new “consumerized” or “democratized” technology may lack decades of tribal knowledge, but it is here to stay.
- Revise your thinking on break/fix vs. maintenance reliability. Today, the worker who got up at 3 a.m. to repair a machine is judged a hero. Maintenance teams that are always successfully troubleshooting problems are star performers. But what if machines rarely failed, and maintenance teams were free to attend to the needs of the whole operation, proactively? With computerized maintenance management systems (CMMS) and Industrial Internet of Things (IIoT) platforms, processes can be automated and maintenance more predictive. This enables companies to more efficiently manage assets, free up maintenance resources, and offset the loss of their longtime fix-it gurus.
- Make greater use of screening and diagnostic tools and the 80/20 rule. As veteran maintenance managers will tell you, at any given time, about 80 percent of a company’s assets are healthy and about 20 percent are worth most of the scrutiny. Screening tools such as an ultrasonic leak detector can help you determine the problem assets. Diagnostic tools such as condition monitoring and laser-shaft alignment tools can help you get more quickly to the root of the problem so you can know when to call in the specialists. With insightful data generated by these tools, tribal knowledge becomes less important.
- Transfer knowledge via video. Yes, encouraging the documentation of processes is smart, but doing it via the written word … not so much. Older workers generally don’t like writing instructions and many younger workers don’t care to pore over pages and pages of steps. Try using videos to share knowledge a la YouTube. For example, documenting how to make sensors and software work together to provide asset conditioning monitoring data can be much more effective with a visual dimension. Your videos don’t have to be anything fancy (and don’t have to go on YouTube). Make them simple and consumable and share with only those who need to know.
- Create ways multigenerational workers can learn from each other. At many companies, resentment runs both ways. Older workers may be annoyed at seeing younger counterparts move in with new ideas and ways of working. Younger workers may begrudge the older generation for sticking around and delaying their chances for leadership roles and promotions. It’s not one generation immediately displacing another — there is some overlap, and many seasoned employees will still be around for a while. There’s much to be gained by offering incentives for them to spend time together sharing and learning.
- Cultivate young leadership to drive change. For at least the foreseeable future, companies will need people, as robots will only take over jobs that don’t require much thinking and analysis. Leaders will come from all the generations in the workforce, but the Gen Xers — those between the baby boomers and millennials — may be your best bet for driving change. They get the need for smart technology, but they also respect and value experience and tribal knowledge. In fact, they have much of their own.
Kevin Clark, CMRP, is Vice President of Fluke Reliability. He has more than 25 years of experience in operations leadership, asset management, IT, supply, manufacturing automation, and safety systems. For more on what 2020 will bring watch this Fluke Accelix Best Practice Webinar on-demand.