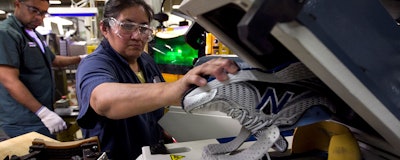
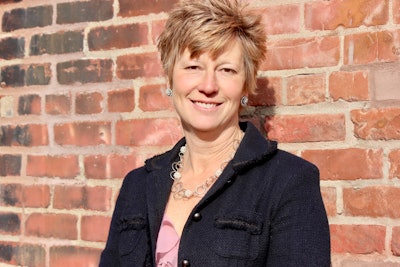
Improving workplace safety is a top priority for most business owners. Working with and around dangerous manufacturing equipment comes with the inherent risk that you may get injured in an accident. When accidents and injuries occur it is bad for the workers, the business, and of course, the injured party. In 2015, OSHA began requiring companies to report any severe, work-related, injuries. The first year of this reporting saw over 10,000 severe injuries, including 2,644 amputations.
Benefits Of Implementing Technology
By using ever-advancing safety technologies, companies can find better ways to track, report, and prevent accidents. Modern safety technology comes in many different forms and can benefit your company in a variety of ways. Having a safer workplace results in an increase in your overall equipment effectiveness, a decrease in unexpected downtime, and a significantly lower injury rate.
In the past, the best way to make a manufacturing workplace safer was to create physical barriers between the equipment and its operators. While this certainly produces higher levels of safety, it can also lead to a slower rate of work and make fixing machinery a more timely procedure. There are newer ways to think about how to solve safety problems. With new, affordable technologies the status quo shouldn’t be acceptable any longer.
Improved Training With 3D Visualization And Augmented Reality
Two of the biggest new technologies that are helping to reduce the need of physical barriers in the workplace are 3D visualization and augmented reality. By creating 3D videos of the workplace and machinery, employees can be trained better than they could be either in person or with regular 2D videos.
With 3D video you have the capability of zooming in to microscopic levels, and zooming out to a scale that could not be achieved with a regular video camera. You can also use 3D video to look inside the machinery so that employees can see all components of machines individually, and understand the inner workings of any piece of equipment. All of these capabilities allow manufacturers to provide high quality training videos to all new and existing employees.
Augmented reality is when computer generated images and data appear on a screen, over what the user is seeing in real life. This technology can be used on phones, tablets, computers, or eyewear. By using augmented reality, employees can see all of the necessary data when being trained on how to use new equipment, and when trying to fix the equipment. This prevents workers from having to get too close to equipment that could be dangerous should it malfunction, or because of a new employees lack of experience.
Drones As A Safety Tool
Drones are serving much of the same purpose as 3D visualization and augmented reality in that they are helping to keep workers away from dangerous situations. One of the most obvious uses of drones is to get to high up, difficult to reach places. Drones can also be sent in to areas that may pose health and safety risks because of chemical spills or extreme temperatures. By sending back high quality data and images of specific situations, or providing broad views of an entire worksite, safety managers can conduct any type of inspection without putting a worker at unnecessary risk.
Incident Tracking and Reporting Can Be Easier
Looking at just the last four decades in particular, other than changes in compliance standards, not a lot has evolved with how workers’ comp is managed. Typically the words innovation and compliance don’t end up in the same sentence. Many organizations still handle workplace safety and claims the same way that they have for years—paper, email, and spreadsheets—yet as consumers, we use technology every day and wouldn’t make it through a day without it.
The collection of data via mobile apps or wearable technology in the workplace can help to prevent injuries by recording leading indicators—such what issues are consistently showing up as a potential threat, where/when is it happening or even what an employee was doing, and where they were when the injury occurred. With this information, future incidences of a similar nature should be able to be prevented or at least made less common.
Another important use for data collection is helping with compliance. As worker safety standards increase it is important to be able to show safety inspectors relevant data, and be able to report on injuries and accidents properly. A key use for this data is in complying with OSHA’s severe injury reporting requirements. Any company that meets OSHA’s requirements that does not submit the required injury and illness data becomes susceptible to civil penalty and citation.
Not only do these technologies show what went wrong when an injury did occur, but they can also prevent injuries in real time by providing workers with real time data and alerts.
As safety technology continues to improve, it is important for the manufacturing industry to stay up-to-date and implement a technology strategy that can help reduce accidents and injuries in the workplace. Technology can improve efficiency, effectiveness and save lives. Don’t let complacency with the status quo prevent you pursuing solutions. You will be more informed and your daily burdens of paperwork and administration will be reduced, allowing you to focus on the most important asset: the people.
Nancy Koors is the Co-Founder and COO at iReportSource.