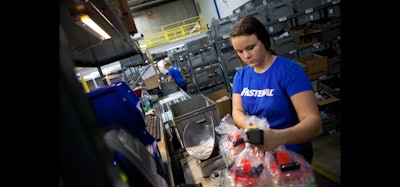
In manufacturing and logistics, the driver shortage has been one of the most intriguing and evolving topics to follow. However, manufacturing faces another shortage, the shortage on the plant floor. According to Polytron, the manufacturing skills gap is estimated to grow to 3.5 million unfilled manufacturing jobs in the next 10 years, up from previous estimates of 2 million vacancies.
Unfortunately, fewer workers leads to high pressures on consumers, existing technologies, engineers, skilled workers and oversight. In other words, the manufacturing skills gap is brewing a cauldron of dangers and profit losses, and you need to understand a few things about bridging the gap in factory settings.
Training Can Be Part of Workforce Development Strategies
The role of training in the factory remains a top factor for bridging the skills gap. Newer employees do not have the traditional exposure to manufacturing that previous generations encountered. Instead, today’s entry-level employees know more about computers and technology, but they lack many physical skills needed in factory settings. Consequently, manufacturers should look at training as an opportunity to mold the next generation for skilled positions.
In addition, some national organizations may provide the training necessary to potential employees, reports Plant Engineering. The Society of Maintenance and Reliability Professionals (SMRP) is one of the organizations, and this organization can help companies assess current operations and predict what specific skilled laborers will be needed in the coming years. As a result, manufacturers can get ahead of the growing skills gap now.
Apprenticeship Programs for Workers About to Retire
Apprenticeship programs are an extension of training in the factory setting. Of course, apprenticeships can begin outside of the manufacturing sector as well. But, existing employees can begin teaching factory-specific skills to new employees directly in the work setting. Furthermore, this may actually be more cost-effective than many realize.
For example, companies already requiring employees to work overtime may see overtime hours decrease when an additional pair of hands is available for work. Essentially, existing staff members may be able to teach and get their duties completed within normal working hours. As a result, the company would incur a lower cost than simply paying an existing employee to work overtime, and with additional political pressures on companies to pay higher wages, implementing apprenticeship programs could easily pay for itself.
Meanwhile, more retiring employees will only lead to greater stress on the factory, asserts Polytron. So, companies need to take advantage of their employees while they are still working.
Creating Relationships Between Youth and Manufacturing Leads to Interest in the Industry
Part of the factory skills gap is the result of a disconnect between today’s youth and the current manufacturing workers. Manufacturing had a way of disappearing from mainstream job ideals over the last 50 years. While this opened the doors to millions of new job opportunities and industries, including the digital revolution, it has left a vacuum in factory settings.
Today’s youth are not interested in what has become a stereotypical environment of mills, monotonous tasks and ongoing “building.” Even those this is nothing more than a stereotype, today’s youth want to be engaged. Take the smartphone for example. It has replaced what was considered engaging to young people at the turn of the century. So, what has your company changed to make it more attractive toward this same group of people in the last decade?
Chances are good that not much has been changed that is easily identifiable by the public. Youth wants positions working with technology and experiences relating to secondary educational opportunities. This concept has been applied previously through the creation of the Boy Scotts of America Welding Merit Badge, explains Plant Engineering. Ultimately, modern manufacturers must get out of the age-old practices of waiting on people to suddenly apply and become more apt and connected to people before they even graduate high school. As a result, more youth will see how their current extracurricular or even vocational activities in school can be applied in real-life work environments.
The Industrial Internet of Things Should Be Applied on and Throughout the Plant Floor
The Industrial Internet of Things (IIoT), or otherwise known as Industry 4.0, is capable of lessening the impact of the manufacturing skills gap as well. Connected devices can be used to reduce demand for reactive maintenance and repair professionals, which will reduce overall demand on other skilled workers. In other words, keeping as many machines operating efficiently will ensure an even distribution of workload in the factory.
Similarly, IIoT has the benefit of directly linking the cornerstone of today’s youth, digital technology, to real-world positions in manufacturing. Essentially, youth will be more apt in learning the skills needed to manage the technologies they have become so familiar with while growing up, and this can be leveraged even more by companies that thoroughly implementIIoT standards throughout their manufacturing centers.
The battle to bridge the manufacturing skills gap does not end with simply getting more people into today’s factories. Manufacturers need to seriously rethink their current community outreach and hiring strategies. But, hoping for the best will only result in an even bigger problem in the future. Instead, companies can take action by knowing what internal and external resources can be leveraged to attract new workers to the plant floor.
Adam Robinson oversees the overall marketing strategy for Cerasis. This blog was originally published here.