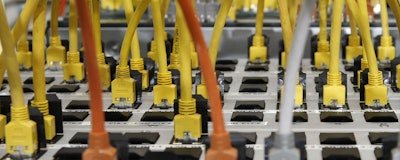
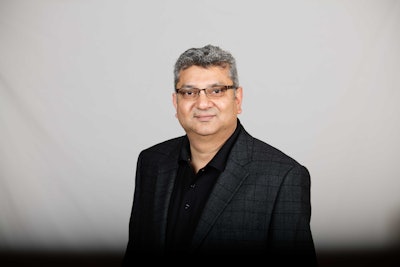
Every industry today has some degree of unwillingness to embrace new technology. Quite simply, companies often fall victim to the mentality of “that is how we have always done it” in regards to current IT systems and operations. So, why disrupt what’s been working in exchange for the latest and greatest technology?
A recent study titled, “Manufacturing 4.0: A Playbook for Navigating the Journey to IT Modernization & Transformation” by Frost and Sullivan, in conjunction with NTT DATA Services, found the manufacturing industry is in need of change. Fortunately, many in the industry are ready for this change — and know it is coming with or without their participation.
Thirty-eight percent of manufacturers believe their facilities are currently operating under a somewhat de-centralized management structure. Within the same group of respondents, 39 percent claim that within the next five years management styles will shift to a collaborative structure that involves employees, customers and suppliers.
The roadmap for manufacturers to improving IT systems is the implementation of Manufacturing 4.0 (M4.0), which encompasses the best practices for achieving IT modernization.
Embracing Change
Manufacturing organizations tend to shy away from implementing new technologies as they are comfortable with current systems and assets as long as the existing tools continue to function.
However, the industry is progressively changing its attitude and implementing newer technologies primarily due to two factors. When asked the most important business factor driving your company’s move toward M4.0, the largest group of respondents, 32 percent, named operational efficiency as the motivator, while the runner up, 17 percent of respondents, chose increased competition due to globalization.
Key strategies for managing factories of the future include updating hardware and software, as well as moving away from a disconnected system with various vendors and models. Manufacturers need to move toward a homogenous environment that allows connected systems with smart production processes. This holistic approach allows the overarching system to share a common data fabric in the IT upgrade from a holistic perspective.
In addition, embracing new technologies can open new revenue channels and business models. Developments in intelligent machines, the Internet of Things, big data, shop floor analytics, modeling and simulation, mobile, cloud and 3D printing technologies allow manufacturers to rethink traditional operations and engineer new ways to improve profitability. For example, instead of selling tangible products, manufacturers can shift to providing “performance as a service.”
Implementing the next generation of technology will create a paradigm shift in not only the work, but also the workforce. However, M4.0 requires leadership to be more responsive and innovative to implement a higher level of connected, collaborative systems.
To embrace this change, future-focused leadership behaviors and mindsets are required. Some companies are establishing a point person, such as a chief disruptive officer, specifically trained for technology disruptions. These go-to specialists facilitate change and make improvements at all levels of business.
Levels of Embracing Digitization
The Manufacturing 4.0 study also found that companies fall into three categories — many of which are having difficulties navigating the roadmap to digital transformation but others are industry trailblazers.
- Non-digitizers (45-50 percent): Companies who identify as non-digitizers are constrained by money and status-quo. The cost of embracing IT modernization and capital spending is a major factor to consider, and ultimately, the driver behind missed opportunities.
- Selective Digitizers (35-40 percent): This lukewarm stage has standardized certain IT solutions, but the value-chain is still siloed and fragmented. These companies acknowledge managing change is a challenge and makes them reluctant to embrace new processes.
- Enterprise Digitizers (<10 percent): At the highest level, enterprise digitizers have a willingness to digitize and to partner with solution providers to achieve a strategic technology vision.
Best Practices
No matter a manufacturer’s level of digitization, achieving IT modernization doesn’t happen until change is embraced and implemented. To become a factory of the future, keep these best practices to ease transformation in mind:
- Create a solid foundation by modernizing the shop floor with updated assets to create a future-proof enterprise.
- Align in-bound supply chains with external market demand to achieve performance optimization that is demand driven.
- Establish an open-channel interface between the factory and points of sale to meet mass customization.
- Shift from site-specific efficiency improvements to enterprise-scale efficiencies with the use of cloud technology.
This roadmap to IT modernization is simple, but the 4-step process isn’t easy. The manufacturing industry has a long road ahead, but change is coming and it is approaching quickly.
The good news is many manufacturing companies are inspired to change and see the benefits of doing so, and may even be the early adopters setting an example for the rest of the industry. The aforementioned research found that at least 42 percent of respondents believe transforming manufacturing operations is a game changer. Are you ready for this new era in manufacturing?
Sameer Deshpande is Senior VP of Discrete Manufacturing at NTT DATA Services.