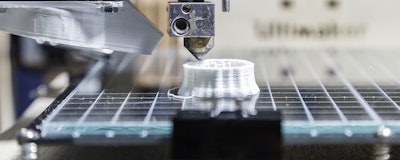
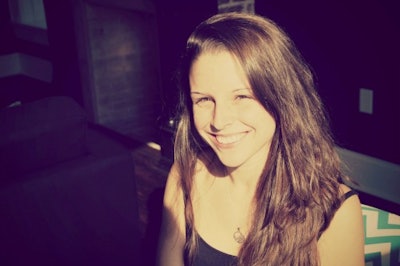
There's no denying that manufacturing in the U.S. has gotten behind in terms of innovation and technology. With so many operations going overseas, the U.S. simply hasn't been focused on the industry enough to introduce any real breakthroughs. But this is all about to change, thanks to 3D printing and the next-gen technology it includes.
The 3D Revolution
Ease and accessibility are driving the 3D revolution, while prompting a renewed interest in domestic manufacturing.
One indicator of this is the increased interest in both consumer- and industrial-scale printers. Basic 3D printers can be purchased for approximately $500. While industrial models cost upward of $30,000, the hardware is still affordable compared to some comparable options.
Perhaps the biggest drawbacks seen in 3D printing thus far revolve around the speed and scale of 3D production. There are also issues regarding user safety and even copyright ownership that are hindering the 3D revolution. Solving these issues will be a challenging obstacle to overcome, but the future remains bright.
Many experts agree that 3D printing has the potential to reinvigorate the manufacturing industry. Some of our nation's top academic institutions are even hosting their own conferences and showcases to tout 3D printing and provide it with some extra momentum.
A new research initiative, developed with collaboration among MIT, State University of New York and Binghamton University, has also stepped forth. They hope to add their own expertise and research capabilities to quicken the 3D revolution even further, and they've already identified a number of shortcomings and bottlenecks within the technology. Independent and homespun research groups like this could be paramount in spreading the word about 3D printing.
Focused on the Future
Proponents of 3D printing have many reasons to be excited about the future. The manufacturing industry as a whole has been growing in recent months, with support for continued growth expected for the future. Couple this with increasing interest in customized goods and the do-it-yourself attitude seen in younger consumers, and it's easy to see how many opportunities there are for 3D printing.
The biomedical sector is making tremendous breakthroughs using 3D technology. A new study projects the medical 3D printing market reaching nearly $1 billion by 2020. This includes prosthetic and replacement limbs, dental treatments, orthopedic appliances and surgical instruments, as well as 3D printers and the necessary software systems.
But the biomedical sector is a complicated discipline. While it is possible to print replacement tissues and human organs using the latest 3D printers, the process isn't as easy as printing a plastic toy for your child. As pointed out by Professor Hod Lipson of Cornell University, 3D-printed tissues and organs require an additional incubation period after being printed.
How You Can Make the Most of 3D Printing
Although experts agree that 3D printing still hasn't reached its full potential, there are numerous steps you can take to make the most of current technology. Make sure to follow tech headlines and recent news for further tips and tricks for implementing 3D printing across your factory floor.
- Begin sourcing materials now. There are numerous plastics and composites available, including ABS, PLA, PVA, nylon, HDPE and many more. For a higher-grade product that is even more durable, you might consider powdered aluminum or steel. Securing a supplier as soon as possible will let you find the best pricing as your needs evolve in the future.
- Train your employees to use the equipment. Some of your staff members might be concerned about their future job security, especially with increasing automation within the factory. Training your workforce on the proper usage, nuances and safety considerations of 3D printing machinery is a great way to provide them with reassurance while also prepping them for the impending change.
- Advertise! Don't forget to promote any new materials you're working with, new hardware you're using or any new services you're offering to your regular customers, as well as the public. You'll want to spread the word about your shop's capabilities in order to corner the market and gain that edge over your competition.
- Forge new partnerships. Use this time to forge new partnerships and relationships with distributors, suppliers, investors and other big names in the niche. Putting these wheels in motion as early as possible is critical when trying to make the most of 3D printing.
Capitalizing on new trends while the technology is still in its relative infancy is key to making the most of 3D printing, both now and in the future. Some of the more tech-savvy manufacturers and business leaders will likely find it easier to make the adjustment than those who rely on more traditional methods, but nearly any factory can be upgraded to take advantage of 3D printing and all it has to offer.
Accommodating the New Business Model
3D printing is taking the manufacturing industry by storm. The benefits of printing 3D objects on the fly and with such a high degree of accuracy stands to benefit nearly every manufacturer around the globe. It's safe to say that we're in for a sudden uptick in 3D-printed goods as the price of industrial and consumer hardware continues to wane, but proactive manufacturers are getting a head start by exploring the technology in its current state.
Kayla Matthews is an independent technology writer at Productivity Bytes.